We ensure reliability of your machines with our technical services
We keep your Sonderhoff mixing and dosing machine ready for durable operation by proactive services to avoid error-related downtimes and maintenance-related production interruptions. Because we know that the productivity of a machine is largely determined by its reliable availability. We support you with our service so that you can plan your production process reliably.
You decide which services you need:
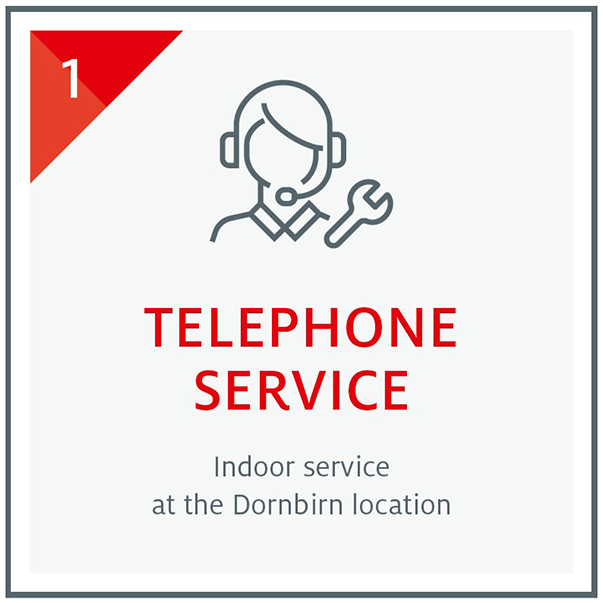
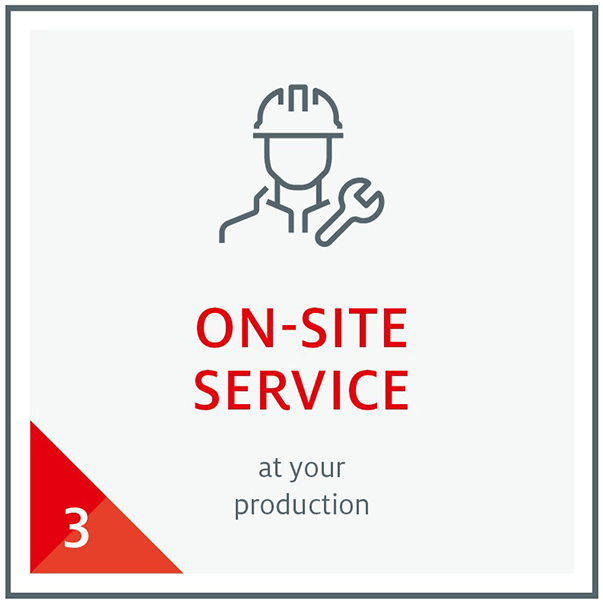
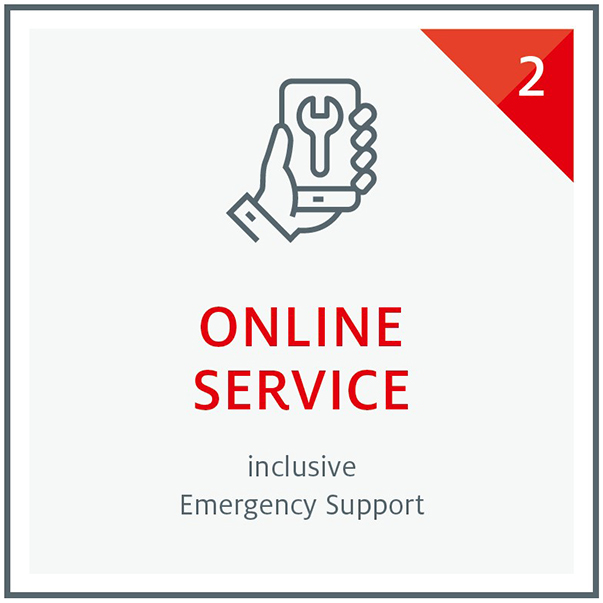
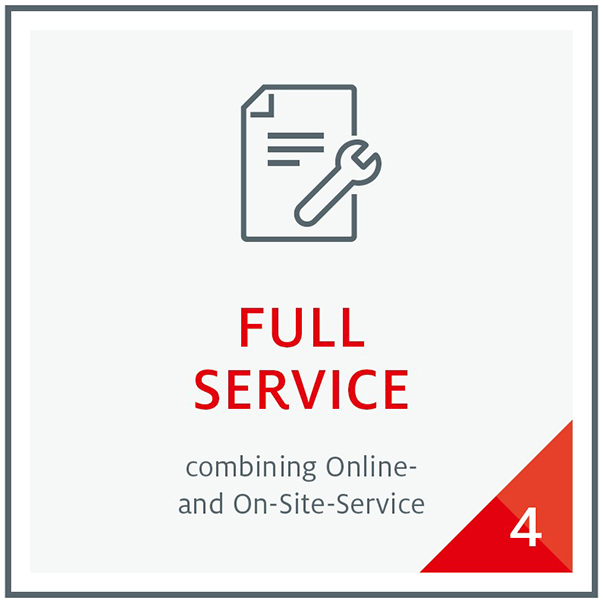
Our various service packages are another reliable pillar of our system solutions.
Option 1:
TELEPHONE-SERVICE
Telephone-service is the backbone for all our services, which can be planned in advance ensuring continuous machine operation.
We support you on the phone in troubleshooting and programming the control of your mixing and dosing machine. We accept orders for the repair of defective machine components or a parts’ overhaul at our location in Dornbirn. We also advise you on your perspective spare parts.
For this purpose, we prepare a risk analysis for the existing mixing and dosing machines in your current production, so that you have an overview of the availability of spare parts and the resulting downtimes of the machines. This can result in schedulable recommendations for the maintenance and servicing of your machine parts, which you can then deliver to Dornbirn.
The risk analysis is not only of interest for your perspective production planning, but often generates forward-looking ideas and inquiries for a modification of the machine based on your planning for new component series to be produced.
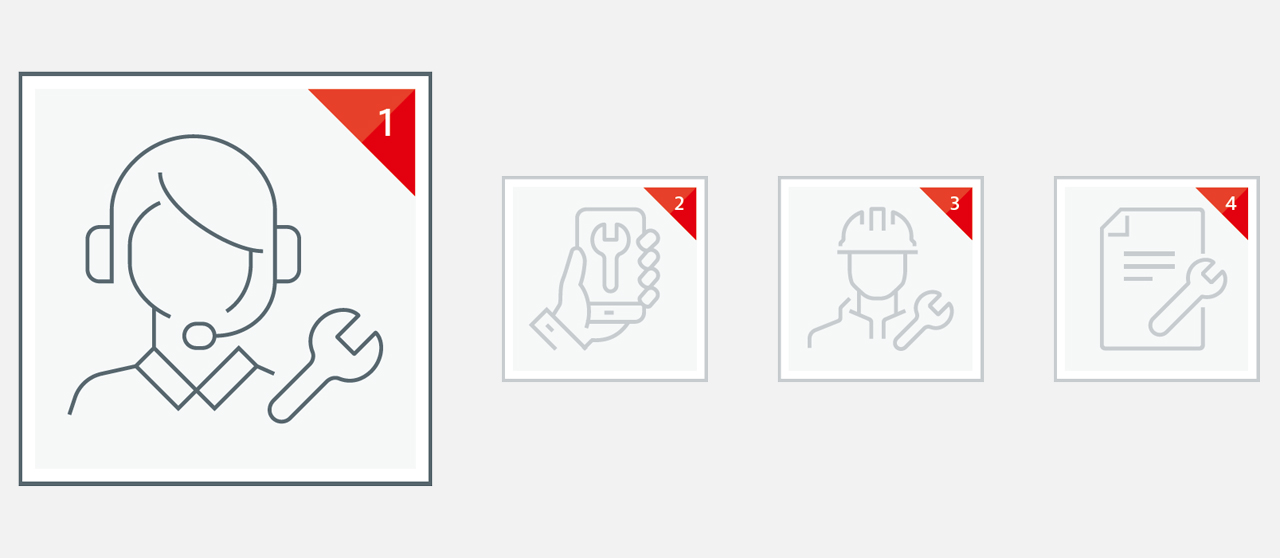
Proactive service is the best protection against machine failures
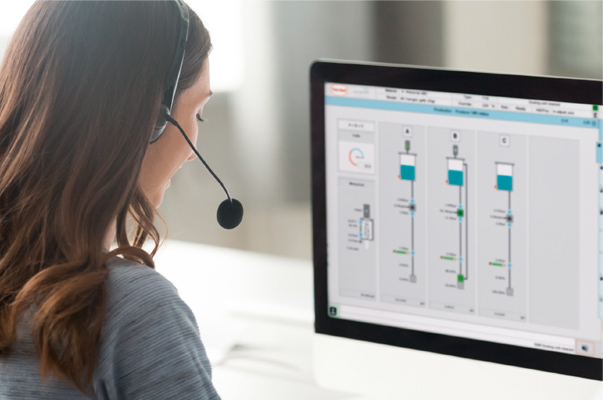
YOUR ADVANTAGES AT A GLANCE
- Proactive protection against machine failures
- Troubleshooting and programming of the dosing machine control system
- Order acceptance overhaul / repair of defective machine components at the Dornbirn site
- Advice on spare parts requirements planning
- Risk analysis for existing mixing and dosing machines in your ongoing production
Option 2:
ONLINE-SERVICE
Pictures say more than a thousand words and are an enormous advantage when we use the new Remote Support via VPN to contact you and advise you on joint troubleshooting and fault elimination.
As soon as our service department is connected to your machine via VPN, it has the possibility to display a mirror image of the machine control (read out, analyze and correct errors and data) and thus have exactly the same information as the machine operator. Together, the task can be discussed, coordinated and corrected.
With this technical possibility, there are of course also extended possibilities for online training of your employees and preventive online machine check.
Regular online machine checks based on the logged machine data enable us to draw conclusions about the wear of machine components or worn seals. In this way, preventive measures are initiated for ongoing production in order to keep downtimes as short as possible.
The VPN connection is the prerequisite for both the preventive service forecast and the emergency, so that we can react very quickly together with you in the event of faults, and that production downtimes do not occur in the first place.
Regular online training courses increase the expertise of your employees. What’s more, they can be held at flexible times, saving time and money on planning and travel expenses for employees. After completion of the training participants receive a training certificate including proof of performance.
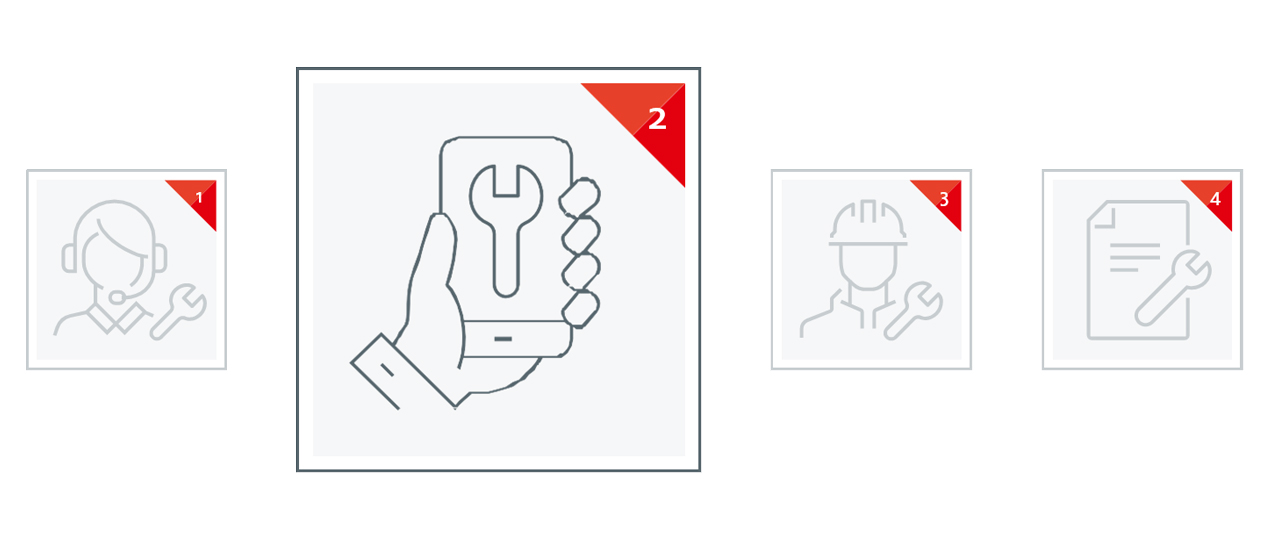
When distance no longer plays a role for interactive consulting
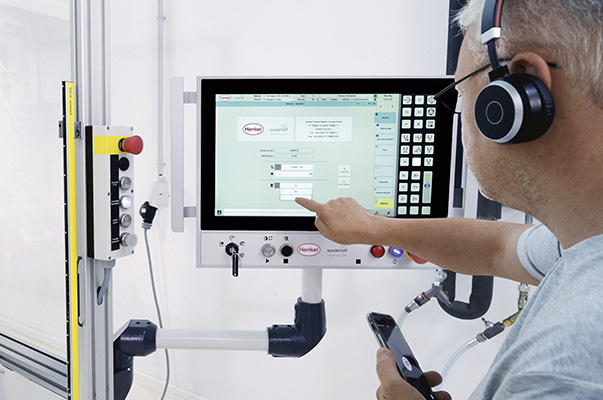
YOUR ADVANTAGES AT A GLANCE
- Remote Support via VPN
- Online Machine Checks
- Online Employee Training
Option 3:
ON-SITE-SERVICE
We know that complex manufacturing processes require automated machine-material solutions and individual machine layouts. Especially in the start-up phase for new component series up to the production of customer-ready products, reliable production processes are very important.
For this reason, we offer you intensive support with our on-site service, in particular for conscientious machine installation, employee training and machine commissioning, as well as for the support or execution of all maintenance work.
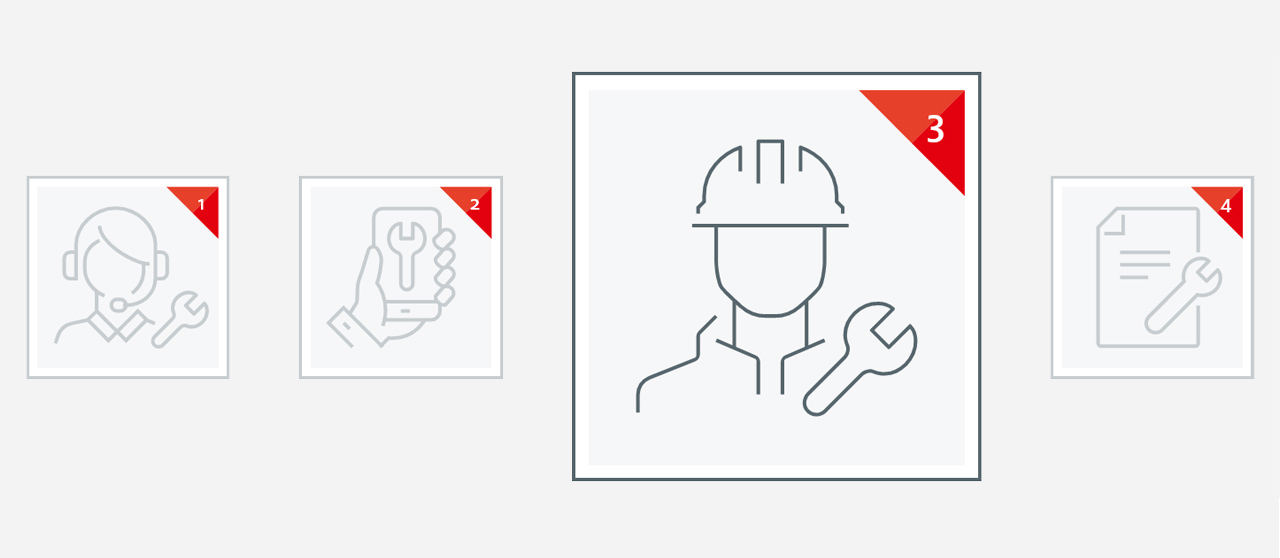
We are also happy to come to you!
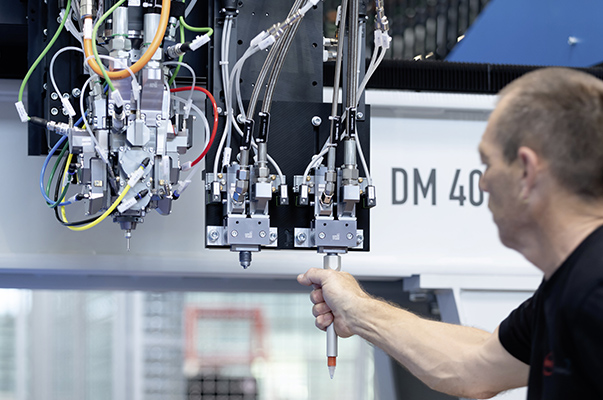
YOUR ADVANTAGES AT A GLANCE
- Machine commissioning (after relocation or shutdown)
- More complex dosing program creation incl. support for cycle time / process flow optimization
- On-site training, with final test if desired
- Machine inspection at cost or with service contract
(at agreed interval times, incl. assessment of machine condition) - Repair of machines at cost or with service contract
- Dismantling and reassembly of machines within the plant premises or in case of change of production site (special on-demand agreement)
Option 4:
FULL-SERVICE
With the Full-Service offer, we combine our online and on-site service measures for you.
You thus receive a contractually agreed all-round carefree package with the highest possible flexibility at foreseeable costs. This saves you time and money, minimizes your ordering processes, and makes it easier for you to plan your budget expenditures.
In addition, we offer you attractive price advantages for spare parts during the term of the contract.
We carry out all the measures specified in the inspection plan on your premises and offer preventive repair work as well as spare parts stocking. In addition, we coordinate and monitor all necessary inspection and service measures as well as the appointments for you. All of this and more can be agreed with you in a Full-Service contract.
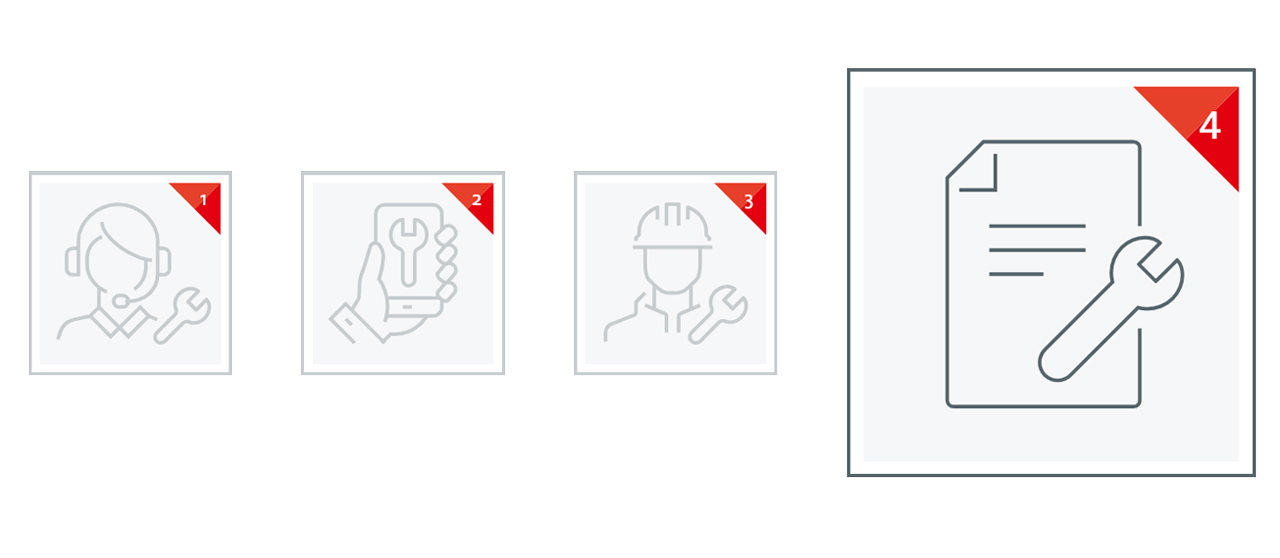
With Full-Service measures for a mutual future
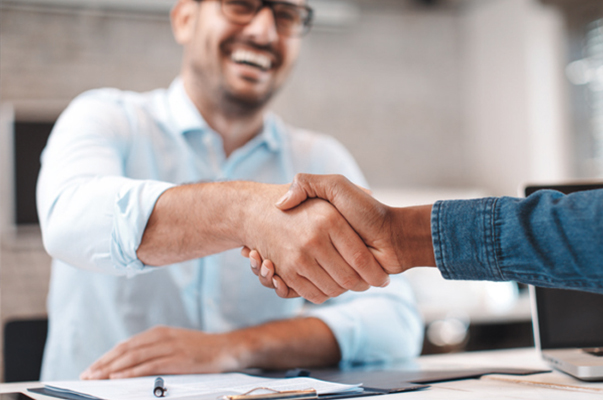
YOUR ADVANTAGES AT A GLANCE
- Ability to plan your inspection and maintenance budget, clear overview of costs and services
- Minimized administrative effort due to contractually fixed service intervals according to inspection schedule
- Minimized / significantly fewer ordering processes
- Appointment coordination and monitoring of all necessary inspection and service measures
- Hot-line telephone / online
- Offers for preventive, necessary repair work
- Recommendations for spare parts stocking
- Price advantages for spare parts during the term of the full service contract
Overview of our service options
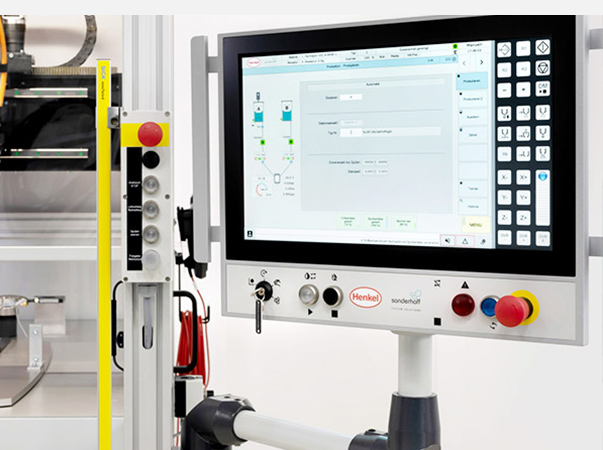
|
TELEPHONE
|
ONLINE
|
ON-SITE SERVICE |
FULL
|
Proactive protection against machine failures |
• |
|
|
• |
Troubleshooting and programming |
• |
|
|
• |
Order acceptance overhaul / repair of defective |
• |
|
|
• |
Advice on spare parts requirements planning |
• |
|
|
• |
Risk analysis for the existing mixing and dosing machines |
• |
|
|
• |
Remote Support via VPN |
|
• |
|
• |
Online-Machine-Checks |
|
• |
|
• |
Employee Online Training |
|
• |
|
• |
Dosing program generation* |
|
|
• |
• |
Support for cycle / |
|
|
• |
• |
Employee training on site |
|
|
• |
• |
Machine inspection |
|
|
• |
• |
Machine repair* |
|
|
• |
• |
Machine dismantling and reassembly / |
|
|
• |
• |
Price advantages for spare parts |
|
|
|
• |
Your contact to our experts: service-engineering@henkel.com or the hotline +43 5572 398810 7211 |
Customer-specific solutions – worldwide and for many industries
The Henkel specialists for the Sonderhoff portfolio are available to you worldwide
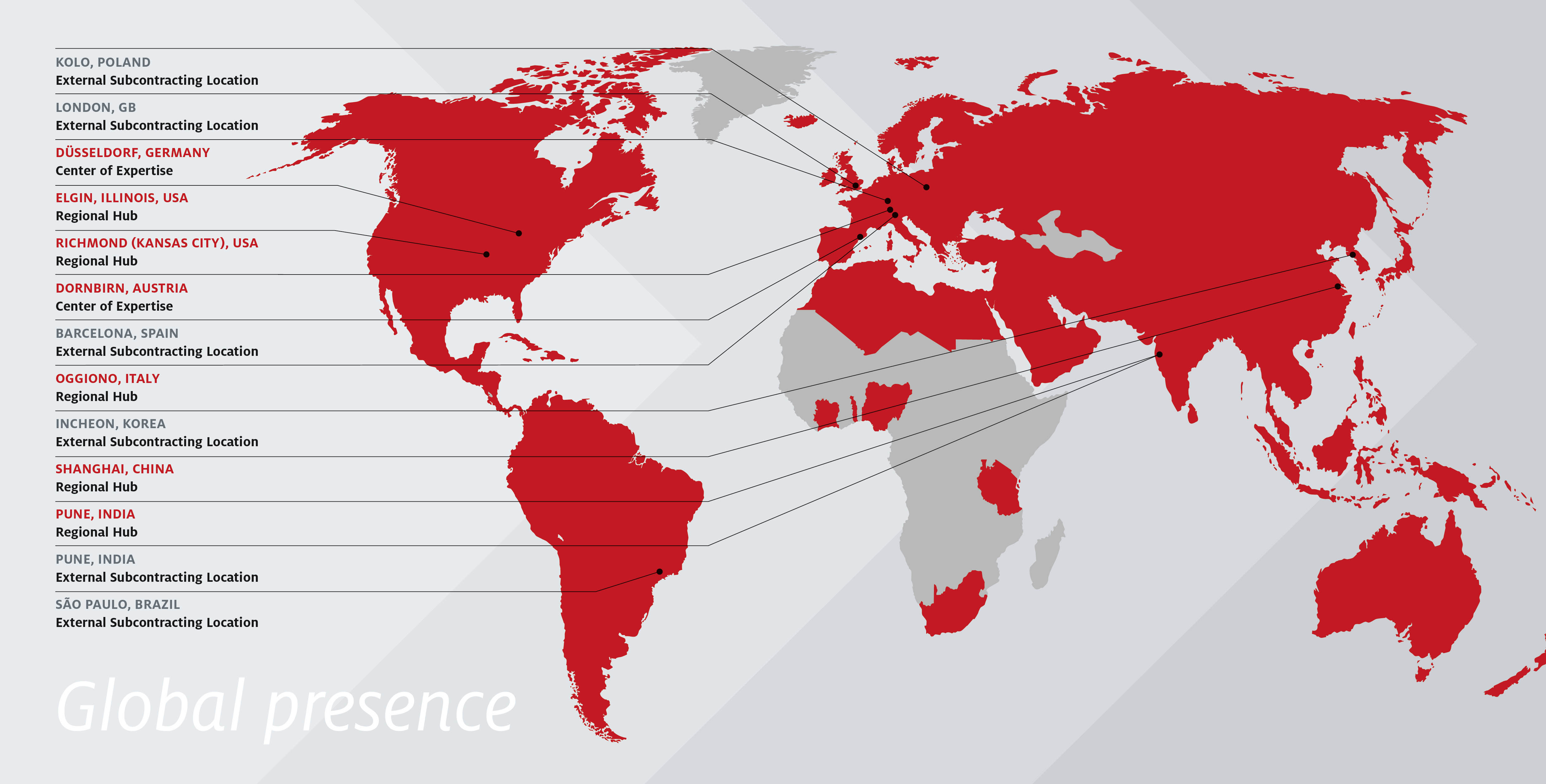
Every year, more than 300 million seals are manufactured in more than 50 countries using products from the Sonderhoff portfolio. At our “Centers of Expertise” and “Regional Hubs”, our specialists offer application engineering advice on the selection of a suitable material system and sampling of your components as well as project management for dosing systems and automation. We can offer training on how to use the FIPFG technology. We will also support you with the selection of spare parts and a regular service offering. Furthermore, we will be pleased to take over parts of your production for you – from small to large series – at our subcontracting locations.
Sales staff at all other Henkel locations worldwide will also be happy to answer any questions and provide you with further information on our sealing, bonding, and potting solutions. We look forward to hearing from you.