FERMAPOR K31 FAST-CURE sealing foam systems
...for high-speed production
As the process specialists for Formed-in-Place Foam Gasket sealing technology, we know which foam seals are needed in the automotive, switch cabinet and packaging industries – the rapidly reacting FERMAPOR K31 FAST-CURE polyurethane foam systems.
Where swift further processing and early build times are the order of the day, FERMAPOR K31 FAST-CURE sealing foam systems come into play. Especially when efficient volume production of large orders is needed, and that with a high variability in the components, the fast tack-free times of fast-cure foams are decisive.
The advantages of fast-reacting FERMAPOR K31 FAST-CURE sealing foam systems are for you:
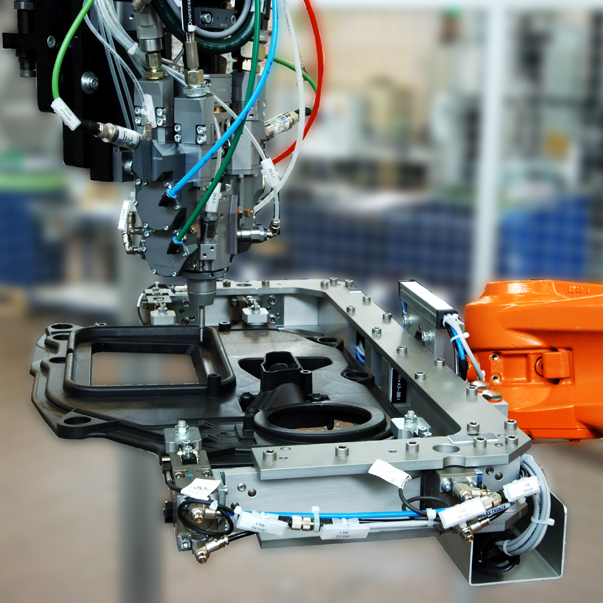
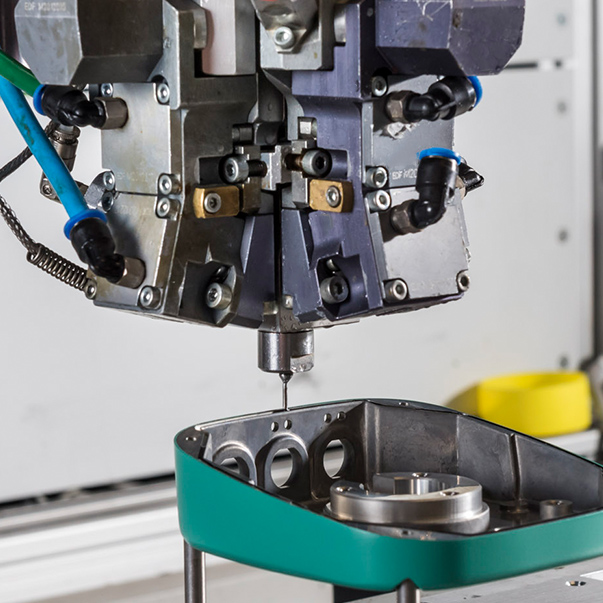
The reaction of the fast-cure material components displays a gradual start time of up to 30 seconds, so that even the short waiting times imposed by the injection moulding process can be accommodated.
Employment of the MOLD’N SEAL processing (inline production of injection moulding and foam sealing) with mixing head wait times of up to 30 seconds for part handling
Very short tack-free time for the fast-cure foam of approx. 120 seconds at room temperature after the dispensing of the part
Low investment: Extremely fast curing only needs short curing lines
Fast reprocessing and early assembly of the parts
Money and time savings through elimination of the need for intermediate storage and the logistical effort of entering and extracting parts from storage for further processing.
Cost saving through elimination of investment and energy costs spent on tempering ovens for the curing of foam seals.
Special fast-cure foam seals from Sonderhoff meet the house technical requirements of manufacturers within the automotive industry, from the Daimler DBL 5452-13 through the VW standard TL848 to Chrysler / Fiat standard MY 560.
Perfect part protection against damp, dust and other environmental influences
Low water absorption: depending on the part and the fast-cure system chosen, the whole system can attain protection classes up to IP69K.
Good adhesion to different material surfaces, on certain substrates after previous treatment.
Adjustable viscosity from fluid to paste-like, flexible as regards part geometry
Low bracing forces through different Shore hardnesses
Good recovery capacity: under test conditions (80 °C, 50 % compression, 22 h) the fast cure foam systems rebound by 96-98 %, essential for retaining high impermeability.
FIPFG sealing technology for the automated application of FERMAPOR K31 FAST-CURE sealing foams.
The FIPFG (Formed-In-Place-Foam-Gasket) sealing technology for the automated application of FERMAPOR K31 FAST-CURE sealing foams directly onto the part is the industry standard for rapid-cycle process production in such sectors as the automobile, switch cabinet and packaging industries.
Wherever fast reprocessing and early assembly of the components is the name of the game, FIPFG dispensing with fast-cure foam seals is essential for the efficient volume production of large consignments.
It is in such rapid production that care is taken to connect processes with one another, so that parts don’t have to wait for onward processing.
FERMAPOR K31 FAST-CURE sealing foam systems for SONDERHOFF MOLD’N SEAL from Henkel – inline production with two processes
The SONDERHOFF MOLD’N SEAL process for process integration from Henkel combines the processes of injection moulding and foam sealing of parts seamlessly in a single production cell. This saves investment, storage and personnel costs. For example, part handling is handled by one robot, as opposed to two previously.
The employment of FERMAPOR K31 FAST-CURE systems specially designed for the SONDERHOFF MOLD’N SEAL process allows a gradual reaction time for the material components in the mixing chamber of up to 30 seconds. This waiting time is used for part handling between the part removal from the injection moulding machine and the foaming of the part under the mixing head. FERMAPOR K31 FAST-CURE systems are customisable for many different injection moulding cycles.
The used Fast-Cure foam system is dispensed directly on the still-warm injection moulding, foams up there to form a seamless seal and, after a very short tack-free time of approx. 120 seconds, is ready for further processing.
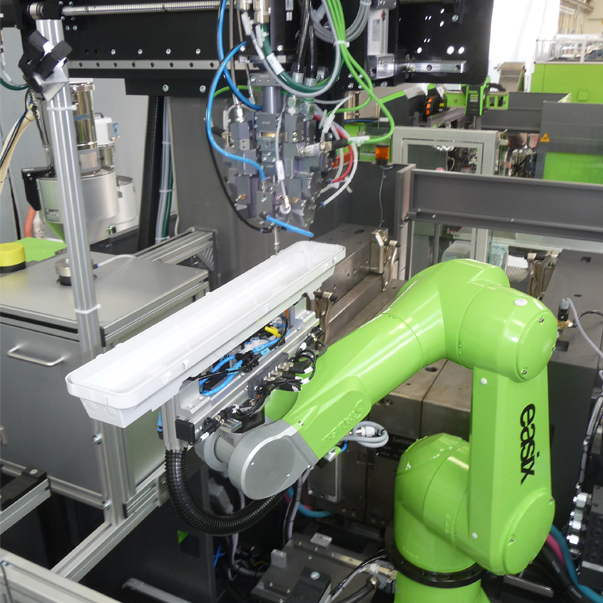