Automated sealing of camper and caravan windows
Sealing process of camper and caravan window frames
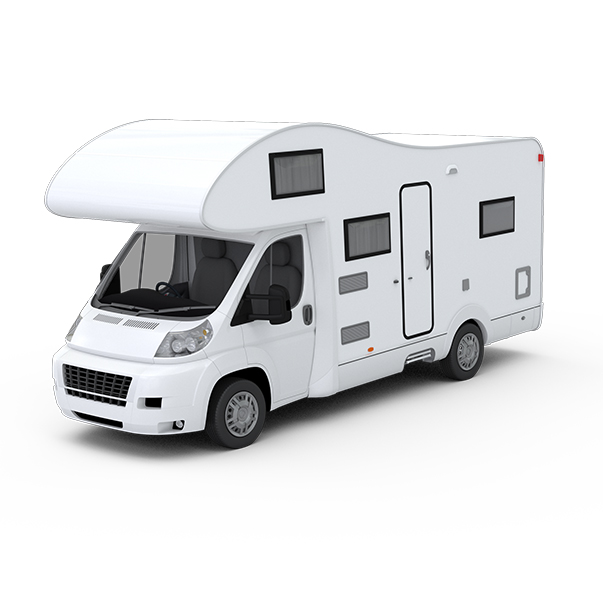
Caravans are comfortable and qualitively high equipped. This includes a sufficient number of windows in the caravan, which provide good ventilation. The window frames must be tight against weather impacts.
Sealing of camper and caravan window frames can be automated using FIPFG (Formed-In-Place-Foam-Gasket) technology. In this process, a fast-curing 2K polyurethane sealing foam is precisely applied by a Sonderhoff dosing machine in a robot-controlled and fully automatic process.
The highly viscous FERMAPOR K31-A-9308-5-VP 5 / K31-B-81 PUR foam gasket is tack-free after approx. 3.5 minutes and forms a seamless seal.
This allows relatively narrow and high gasket cross-sections. With a hardness of approx. 45 Shore 00, the foam seal has good compressibility.
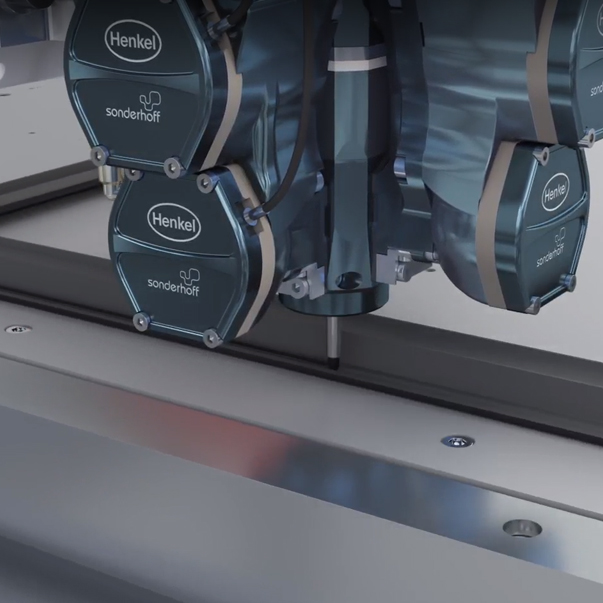
The closing forces when installing the windows are therefore low. In addition, the mixed-cell foam structure compensates for dimensional tolerances. The adhesion of the PUR foam to the frame, usually ASA, PUR or aluminum, is good and can be further improved, for example, by plasma pretreatment.
FIPFG technology allows great design freedom in window frame design. The sealing material can be applied on two- or three-dimensional surfaces or in grooves.
We can provide you with the perfectly coordinated system solution comprising material, machine and process for fully automatic material application.
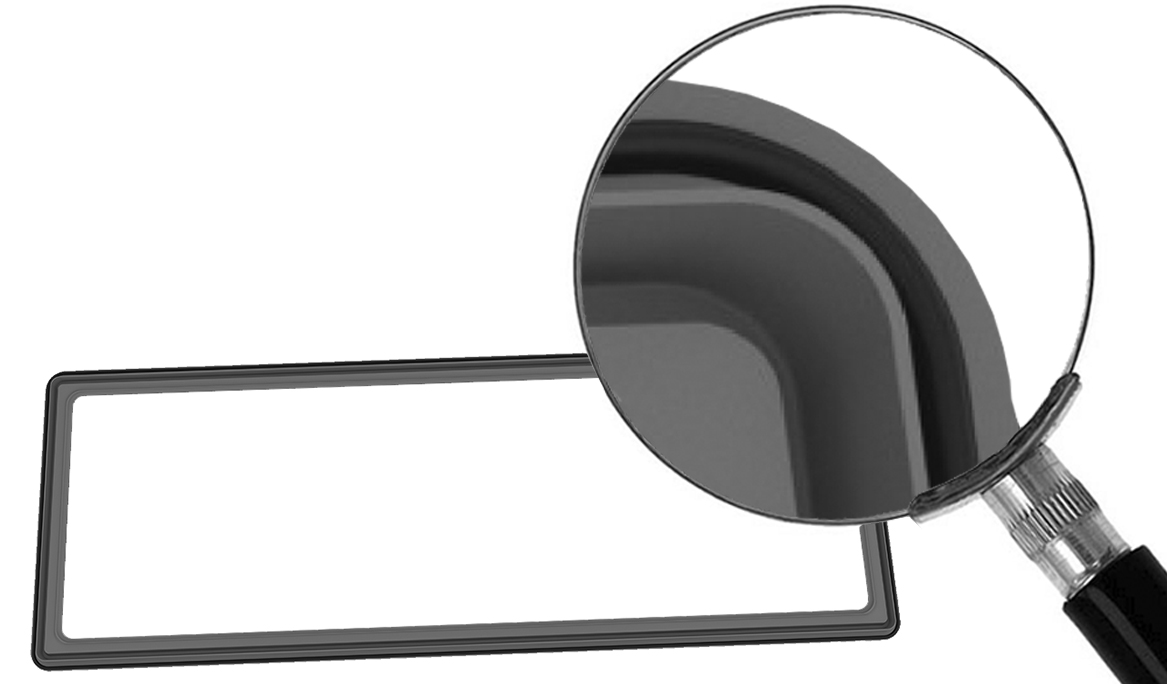
Sealing of camper and caravan window frames with polyurethane foam gasket FERMAPOR K31-A-9308-5-VP 5 / K31-B-81.
Reliable sealing with optimized material consumption
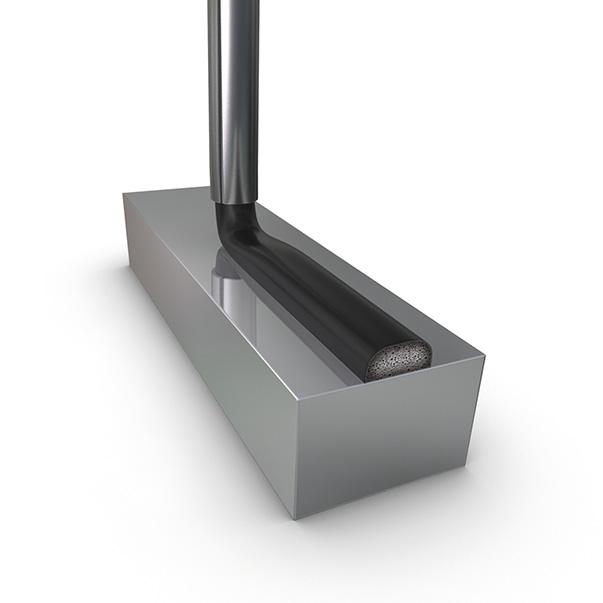
We develop individually for your specific requirements
Polyurethane sealing foams from the FERMAPOR K31 product family are used to seal the plastic window frames installed in caravans and campers. The foam material is applied with our mixing and dosing machines to the flat or slightly recessed application surface of the frames, where it remains stable.
The soft seal foamed in place solidifies due to a crosslinking reaction of the polyurethane foam components and is usually tack-free after a few minutes at room temperature. The variably adjustable degree of softness is advantageous for low compression forces when installing window frames in vehicles.
Due to the mixed-cell foam structure, the polyurethane seal can be compressed evenly and provides a consistently high level of tightness against moisture when installed.
In addition, thanks to the efficient and very precise FIPFG technology, significantly less material is used when sealing with polyurethane foam compared to the punched seals used in the past.
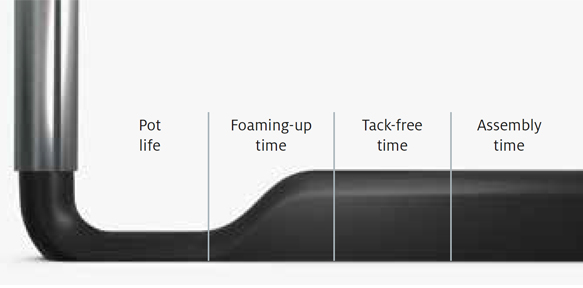
The different reaction phases of the sealing foam in the chronological sequence.
Reference material
FERMAPOR K31-A-9308-5-VP5 | ||
FERMAPOR K31-B-81 | ||
Mixing ratio | 4 : 1 | |
Pot life time | 24 sec | |
Tack-free time | 3.5 Min. | |
Viscosity of the A component | 130,000 mPas | |
Density of foam | 0.20 g/cm³ | |
Hardnee (Shore 00) | 45 | |
Heat resistance | from -40 to + 80 °C | |
Pretreatment | Plasma for e.g, PP and PE |
In addition to the reference products, we develop material systems according to your individual requirements. Influencing factors include pot life until start of foaming, curing time, and the viscosity, hardness and adhesion properties.
Repeated installation and removal of the window frame - with consistent sealing effect
The very good resetting ability of the foam seal allows repeated installation and removal of the window frames for maintenance purposes without the sealing effect weakening.
The polyurethane foam used adheres very well to the plastics commonly used for window frames. For adhesion to plastics such as PP or PE, it often requires pretreatment by plasma. We will be happy to integrate a plasma application unit into your automation system for this purpose.
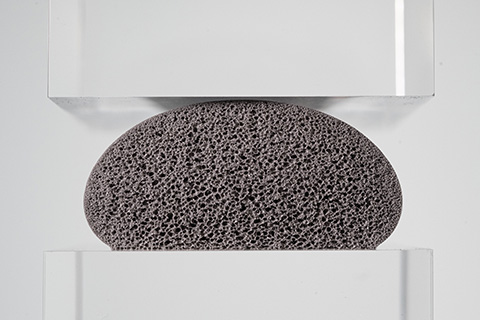
The unpressed polyurethane foam gasket before installation.
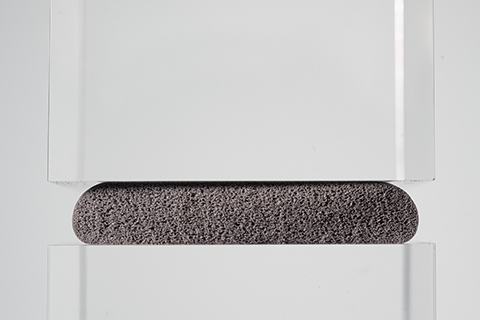
Compressing the foam gasket achieves the required degree of tightness achieves in the installed condition.
Flexible and fully automatic – according to your requirements
DM 502 mixing and dispensing system with 3-axis linear robot and shuttle table for part pick-up.
The alternative reference configuration shown here consists of our DM 502 mixing and dosing system with 3-axis linear robot and shuttle table for part pickup. The two shuttle tables, working in pendulum mode, enable the workpieces fixed there to be picked up and processed in one level. This means that very short cycle times and continuous operation can be guaranteed.
The placement and positioning of the window frames on the shuttle table plate is carried out either by a machine operator, who can also check the parts for quality, or by a pick & place robot. In this case, an optionally installed camera system could perform quality control of the parts. The optional plasma nozzle, CNC-controlled by the 3-axis linear robot and mounted on the Y-axis, applies plasma to the component contour for surface activation. This results in better adhesion of the foam gasket.
The polyurethane sealing material is dosed with the CNC-controlled MK 825 PRO precision mixing head and applied with high precision fully automatically to the flat or slightly recessed surface of the window frame contour. This FIPFG process ensures high dosing and repeat accuracy. After the dosing cycle, the coupling point of the foam gasket closes seamlessly and is almost invisible.
The material components of the polyurethane foam used are mixed dynamically and homogeneously in the mixing head of the DM 502. The resulting fine-cell foam structure is crucial for low water absorption levels. When installed, the uniform compression of the seamless foam gasket produces a consistently high level of tightness over the entire contour of the window frame.
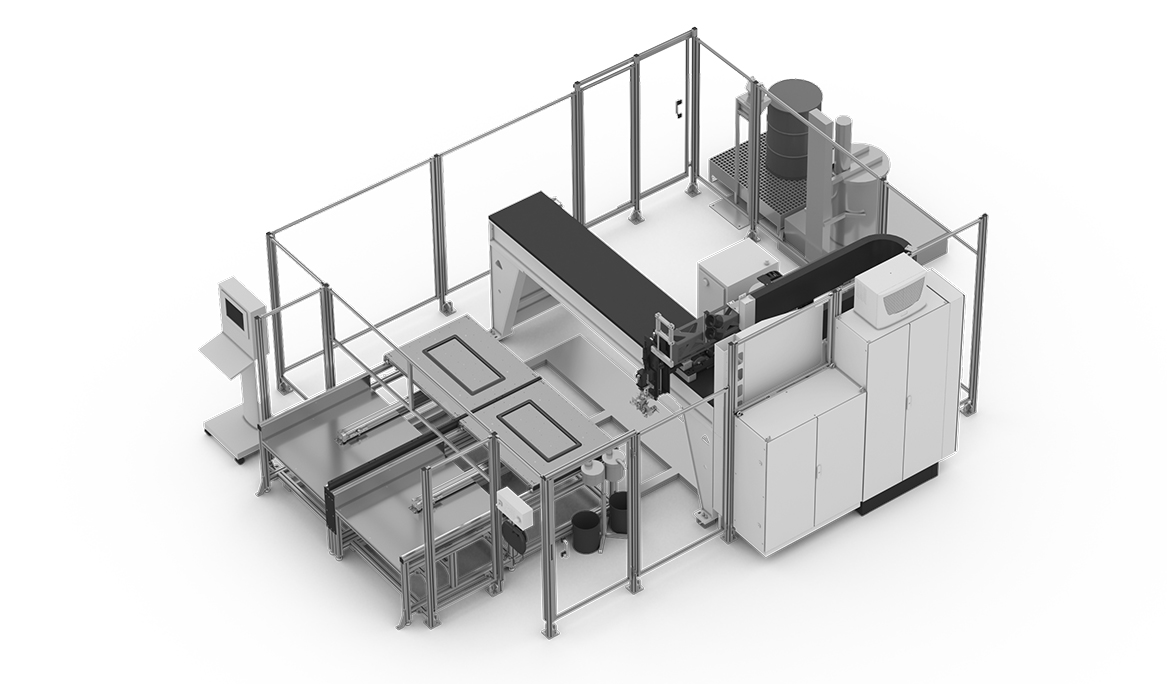
CONTROL 2
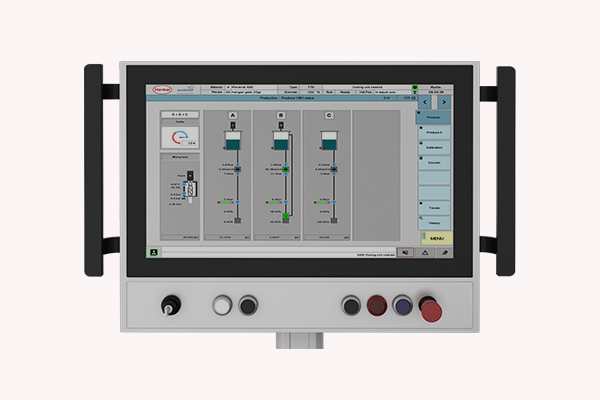
Optionally available: CONTROL touchscreen operating panel (21.5“) for operating the dosing system
More information to our operating panelsWT 1-LEVEL shuttle / sliding table
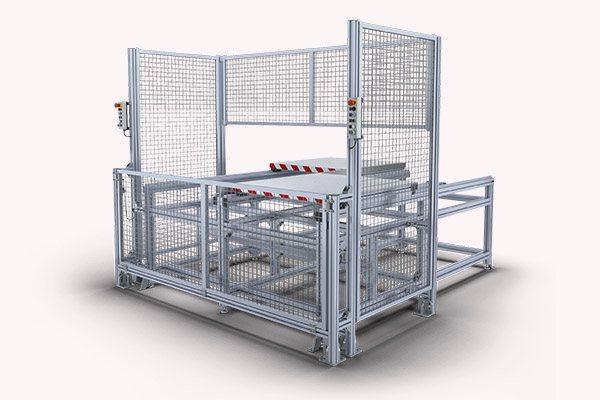
Two pick-up plates operating in pendulum mode in one plane
More information to our shuttle tablesMischkopf MK 800
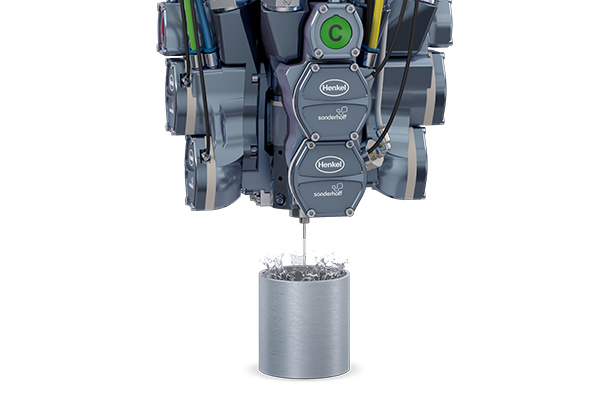
MK 800 PRO precision mixing head with high-pressure water rinsing or alternative component rinsing system
More information to our mixing headsDosing components and material containers
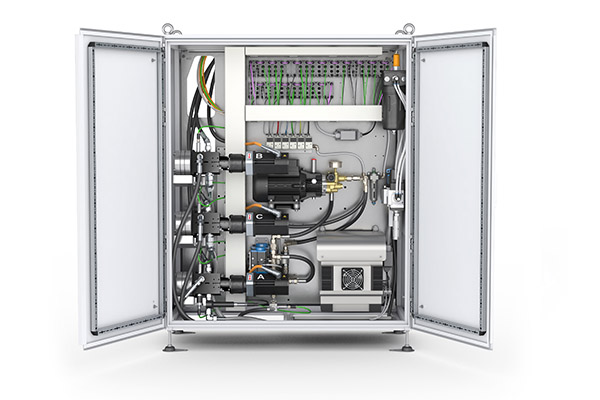
The dosing machine cabinet contains the components of the dosing periphery, e.g. the dosing pumps.
More information to our dosing machine cabinetsControl cabinet
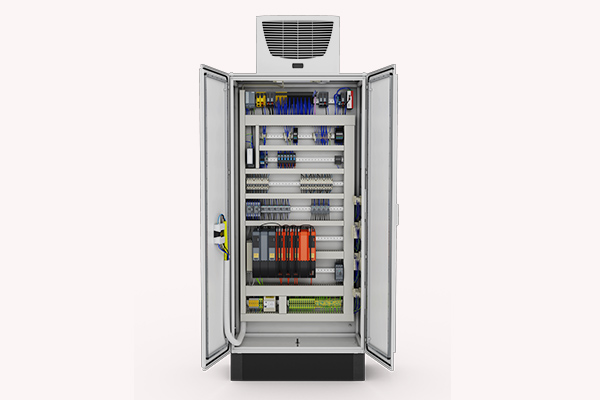
The control electronics, safety engineering and industrial PC are installed in the control cabinet.
More information to our control cabinetsElevator
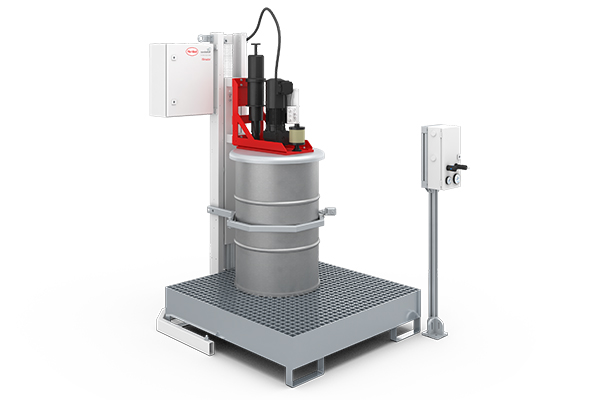
Optional: Automatic ELEVATOR drum refilling station for the A-component with pneumatic lift and agitator
More information to our refilling stationsSupply Tap
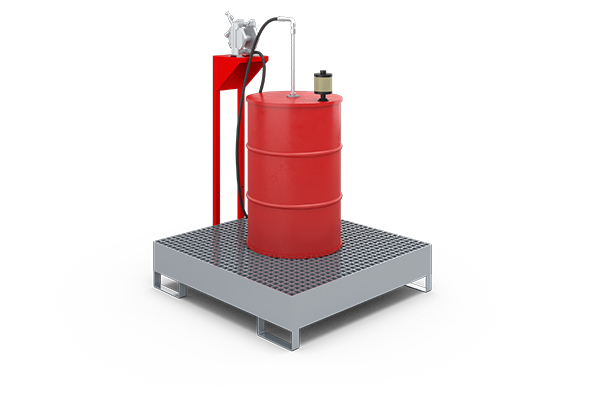
Optional: Automatic SUPPLY TAP drum refilling station for low-viscosity products, e.g. isocyanate (B-component)
More information to our refilling stations