Dosing Machine Cabinet
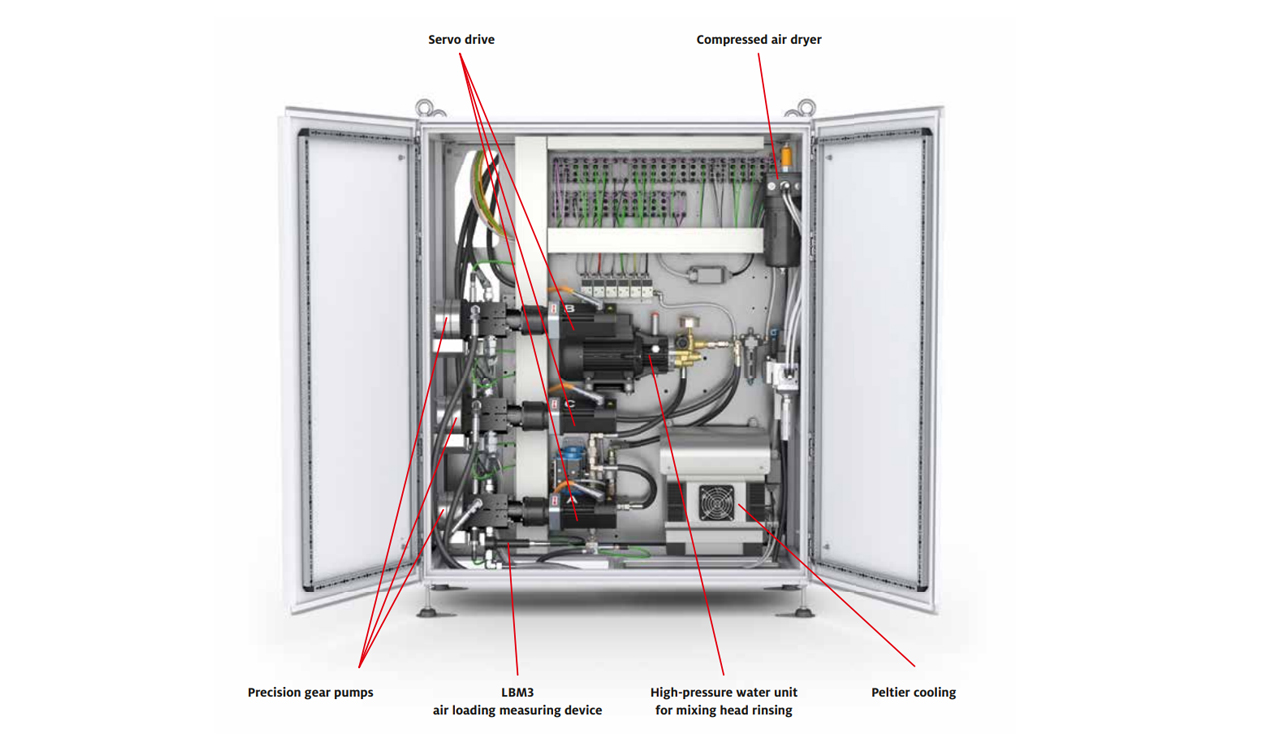
GENERAL
The dosing machine cabinet is a compact, self-contained unit that contains all components important for the dosing process:
- precision gear pumps with servo drive for dosing the material components,
- high-pressure water unit for the mixing head rinsing,
- Peltier cooling unit for tempering the mixing head and the recirculation hoses,
- LBM 3 air load measuring and control device,
- compressed air dryer
The precision gear pumps are installed in the dosing machine cabinet in a user-friendly manner by a new mounting system. They ensure precise dosing of the material components on their way through the recirculation lines to the mixing head, where they are dynamically mixed in a defined mixing ratio.
The cabinet with lockable hinged doors and a side service door is designed for user-friendly maintenance. Only 2 screws need to be loosened to replace the pumps including the drive train. The side service door provides direct access for removal of the pump heads.
The high-pressure water unit for the mixing head rinsing uses tap water, which is usually discharged into the regular wastewater system after use. This saves disposal costs that would be incurred with conventional solvent-based cleaning (after case-by-case review with local wastewater authorities).
The Peltier cooling unit provides cooling of the mixing head and, if necessary, also of the recirculation hoses and can thus positively influence the reactivity behavior of the 2K material systems.
The LBM 3 air loading measuring device checks the air loading of the A-component to form the desired cell structure of the polyurethane or silicone foam seal.
- Chassis: modular hybrid structure, painted in RAL 7035
- Pressure control for adjusting the recirculation pressure
- Pressure monitoring of the components, optional digital component pressure display for air loading control
- Mixing ratio: from 100 : 1 to 1 : 100, continuously adjustable
- Application rate: from 0.05 to 100.0 g/s, other application rates on request
- Viscosity processing range: from 50 to 2,000,000 mPas, other viscosities on request
- Material supply monitoring for component pumps
- Rinsing and filling shot container
DRIVE TECHNOLOGY
Speed-controlled servo gearmotor with speed display and adjustment on the display
Pumps | Mixing head | |
Driving power | 0.94 kW | 0.94 (alternatively 1.13) kW |
Driving speeds | 1 – 250 rpm | 1 – 4,500 (alternatively 1 – 6,000) rpm |
PRECISION GEAR PUMPS (OPTIONALLY)
- For FIPFG sealing foam, size: 0.05 / 0.10 / 0.30 / 0.40 / 0.75 / 3.0 / 12.0 ccm/rev.
- For potting / adhesive applications, size: 0.05 / 0.10 / 0.30 / 0.60 / 1.20 / 3.0 / 6.0 / 10.0 ccm/rev.
- Special pumps on request
HOSE PACKAGE
- Length according to customer requirement with all electrical and pneumatic connections
- A component: Fabric-reinforced polyester high-pressure hose
- B component: Steel-reinforced Teflon high-pressure hose
PNEUMATICS
- Pneumatic system with filter pressure reducer, maintenance unit with pressure monitoring and valve cluster for controlling the pneumatic consumers
CONNECTED LOADS
- Compressed air connection value: approx. 150 l/min at 6 –7 bar
- Water connection value: approx. 13 l/min at least 4 bar
DIMENSIONS
- Dosing machine cabinet: B x H x D 1,210 x 1,400 x 510 mm, alternatively also with a height of 2,000 mm (without frame, feet or carrying eyes), approx. 300 kg
Precision gear pumps
Precision gear pumps
In order to remove the pump, only 2 screws need to be loosened
.
Precision gear pumps
Precision gear pumps
In order to remove the pump including the drive train, only 2 screws
need to be loosened.
.