Verklebung von Automotive Displays
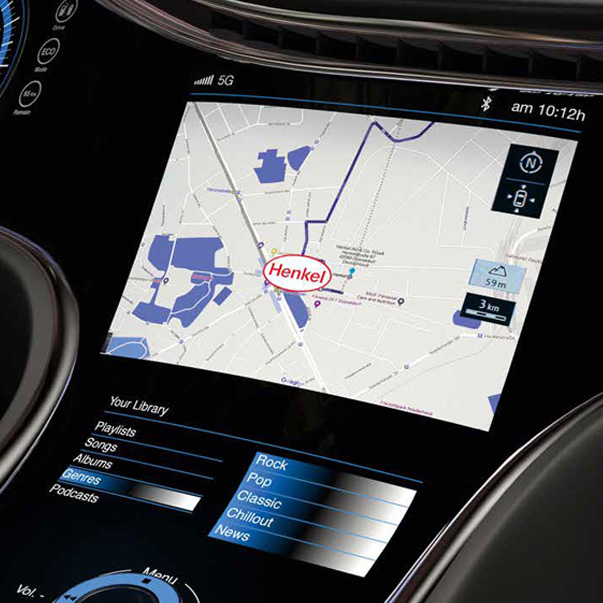
Die Digitalisierung und Vernetzung des Autos für eine moderne Mobilität mit zunehmend selbstfahrenden Fahrzeugen erfordern ein Auto mit mehrdimensionalen Infotainment- und Sicherheitsfunktionen sowie Schnittstellen, die einen individuelleren und interaktiven Ansatz für die Verkehrsteilnehmer bieten. Automotive Displays unterstützen die Sicherheit des Fahrers durch aktuelle Informationen über das Verkehrsgeschehen und die Funktionalität des Autos und schaffen eine komfortable Cockpit-Umgebung.
Die Automotive-Infotainment-Systeme bieten über ihre Displays Audio- oder Videounterhaltung für alle Insassen und die grafische Visualisierung der durch Fahrerassistenzsysteme (ADAS) zur Verfügung gestellten Informationen für den Fahrer, wie Einparkhilfe, Navigation, Verkehrsassistenz, Kontrollfunktionen und Internetkonnektivität. Über Touch-Displays sind alle Einstellmöglichkeiten im Auto bedienbar.
Freigeformte und gebogene Automotive Displays sind die Zukunft, um größere und attraktivere Displays für das Armaturenbrett zu ermöglichen. Gehäusedesigns werden weiterentwickelt, um den Platz im Innenraum besser zu nutzen und größere und reaktionsschnellere Bildschirme unterzubringen.
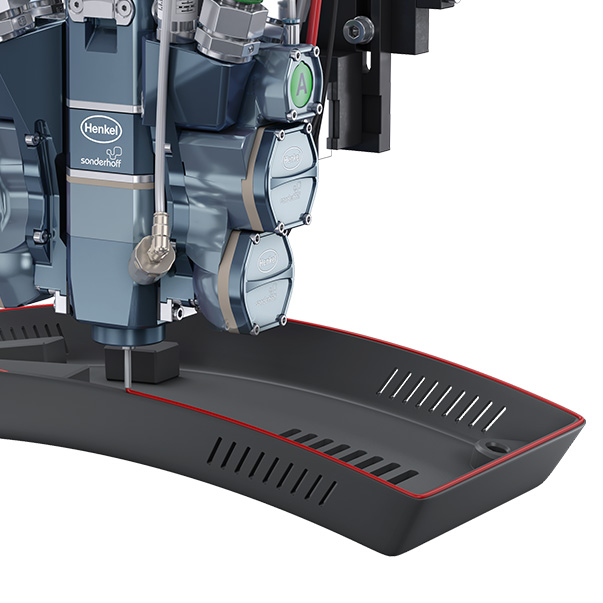
Mit unseren Lösungen für strukturelles Verkleben von Automotive Displays werden wir den Markttrends, wie die zunehmende Nachfrage nach Designflexibilität gerecht. Die hochpräzise Dosierung mit den vollautomatischen Misch- und Dosieranlagen von Henkel sorgen für eine hohe Konturgenauigkeit des Klebeauftrags.
Wie stellen Sie eine perfekte Displayverklebung sicher, wenn aus Kosten- und Designgründen die Verklebungsflächen des Displaygehäuses zunehmend schmaler werden?
Was machen Sie, um Bauteiltoleranzen beim Kleberauftrag auszugleichen und nach dem Fügen eine gleich breite Kleberraupe zu erzielen?
Mit Active Quantity Adjustment (AQA) haben wir für Sie die Lösung. Dieses Verfahren ermöglicht es, die Dosiermenge beim Kleberauftrag an die Teilekontur so anzupassen, dass unterschiedliche, herstellungsbedingte Unebenheiten der Verklebungsflächen durch eine genau vorausberechnete und entsprechend exakt dosierte Klebstoffaustragsmenge ausgeglichen werden. Vor der Dosierung misst dazu ein 3D-Linienscanner die Teilegeometrie, die dann mit der vorher definierten CAD-Referenz des Bauteils verglichen wird. Im Ergebnis entsteht nach dem Fügen eine in Höhe und Breite konstante Klebefuge.
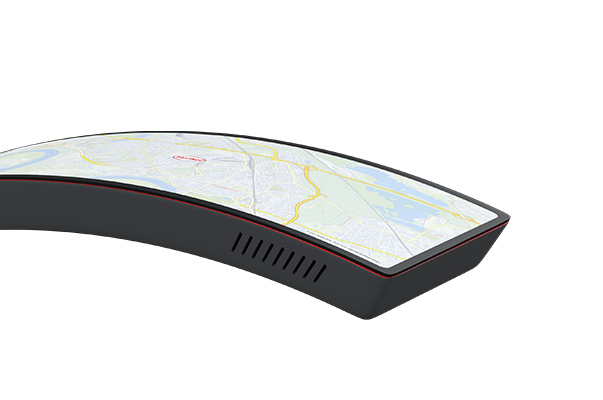
Der Trend zu größeren Displays in Fahrzeugen, bei gleichzeitiger Notwendigkeit für einen platzsparendem Einbau, hat allerdings zu schmalrandigen Displaylösungen geführt. Die Herausforderung besteht darin, bei schmalen Klebeflächen und somit dünnen Klebelinien dennoch eine starke Klebehaftung zu erreichen.
Und beim Zusammenfügen des Displays mit dem Gehäuse darf der Kleber nicht an den Rändern heraustreten. Den vollautomatischen Kleberauftrag und Toleranzausgleich übernehmen die Misch- und Dosieranlagen von Henkel.
Brandneue Animation des AQA (Active Quantity Adjustment)-Prozesses für die Displayverklebung mit LOCTITE MS 650 unter Verwendung einer Sonderhoff Dosiermaschine. Gezeigt werden die Prozessschritte vom Spritzgießen, der Bildverarbeitungsscanner, die Verklebung und das Fügen mit und ohne AQA-Prozess, um die Unterschiede und Vorteile zu verdeutlichen.
Animation der Systemlösung für Displayverklebung mit LOCTITE MS 650 unter Verwendung einer Sonderhoff-Dosiermaschine / AQA-Prozess
Exakte Verklebung auf schmalen Klebeflächen
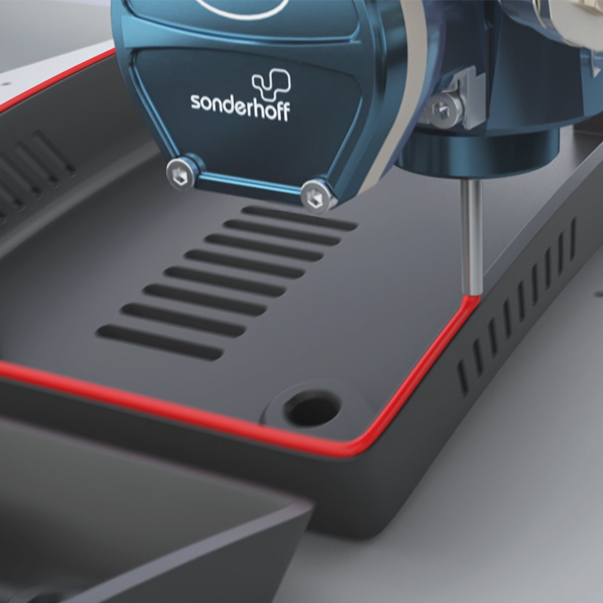
LOCTITE® MS 650 – Polymerklebstoff für elastische Strukturverklebungen mit hoher Anfangsfestigkeit
Frei geformte und geschwungene Designs von Automobildisplays dominieren den Innenraum moderner Autos und sind vollständig in die gesamte Innenraumgestaltung integriert. Das Design und die Herstellung von Automobildisplays erfordern eine Vielzahl von Materialien, die von der Sicherstellung der Festigkeit der Display-Gehäusestruktur bis hin zur Verklebung der Abschlussscheibe mit dem TFT / LCD-Display reichen.
Zur Verklebung des Automobildisplays mit dem Gehäuse wird LOCTITE® MS 650 – ein thixotroper, silan-modifizierter Polymerklebstoff – für elastische Strukturverklebungen mittlerer bis hoher Festigkeit eingesetzt. Hiermit können Multi-Substrat-Verklebungen wie Kunststoff auf Kunststoff, Kunststoff auf Glas und Glas auf Glas für frei geformte und gekrümmte Design-Displays realisiert werden.
LOCTITE® MS 650 ist als 1-Komponenten-Klebstoff für die Aushärtung bei Feuchtigkeit oder als 2-Komponenten-Klebstoff für die beschleunigte, ultraschnelle Aushärtung erhältlich.
Sie bieten eine hohe Grünfestigkeit und schnelle Hautbildung. Aufgrund sehr schnell härtender Eigenschaften erreicht der 2K Klebstoff bereits kurz nach dem Fügen der Bauteile eine hohe Anfangsfestigkeit bei Raumtemperatur.
Die für die Displayverklebung eingesetzten 2K-Klebstoffe auf MS-Polymerbasis werden unter Einsatz der Sonderhoff Misch- und Dosiermaschine in einem bestimmten Mischungsverhältnis dynamisch homogen vermischt und mit der Formed-In-Place- Technologie vollautomatisch und sehr präzise auf die Klebfläche des Displaygehäuses aufgetragen.
Referenzmaterial
LOCTITE MS 650 2C | |
Mischungsverhältnis, nach Gewicht | 10 : 1 |
Offene Zeit (DIN 50014 Normklima) | ca. 4-5 min. |
Stabilität der Handhabung | ca. 9-12 min. |
Klebefreizeit | ca. 2-10 min. |
Viskosität A-Komponente | ca. 180-330 pa.s |
Viskosität B-Komponente | ca. 150 pa.s |
Dichte | ca. 1,4 g/cm³ |
Shore-A-Härte | ca. 55 |
Gebrauchstemperatur | von -40 bis +90 °C (kurze Belichtung / bis zu 1h: 120 °C) |
Anwendungstemperatur | 15 bis 40 °C |
Aushärtung | Aushärtung bei Umgebungstemperatur (über 5 °C) oder Aushärtung bei erhöhten Temperaturen |
Technisches Datenblatt (Englisch) LOCTITE MS 650 2C
Sonderhoff Lösungen für Displayverklebungen unter der Lupe
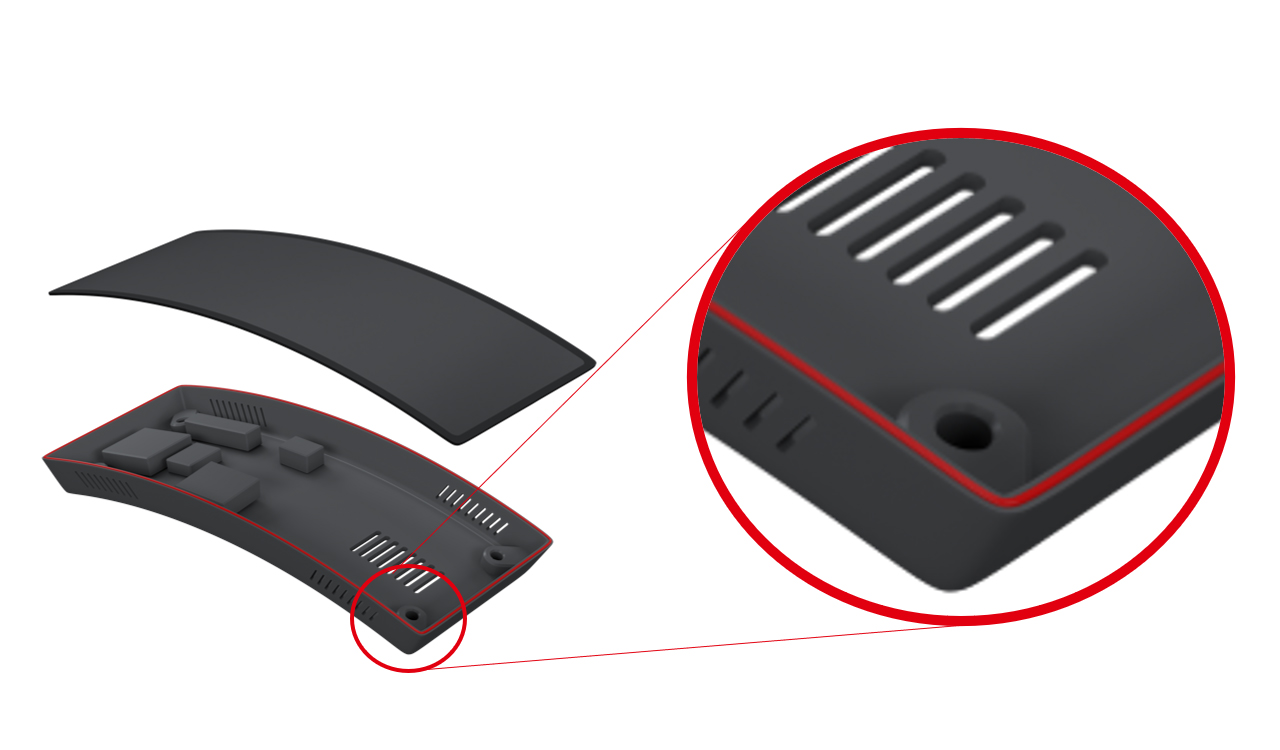
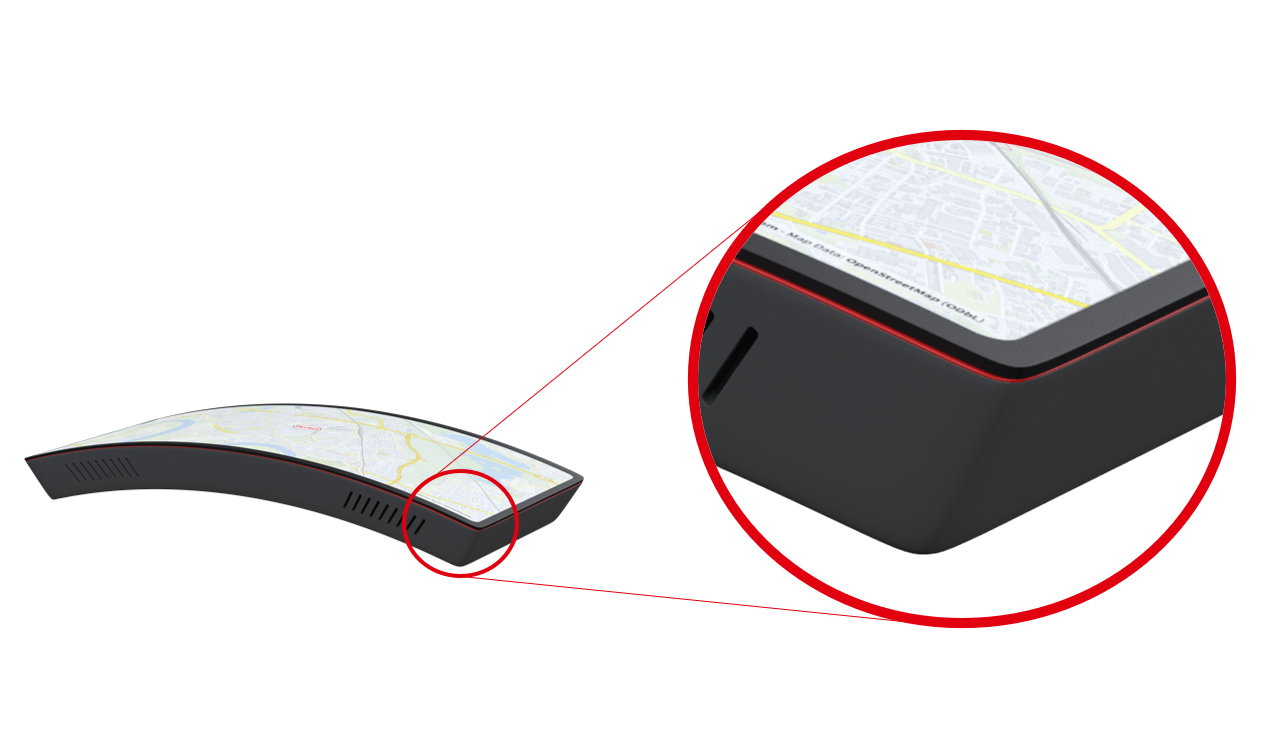
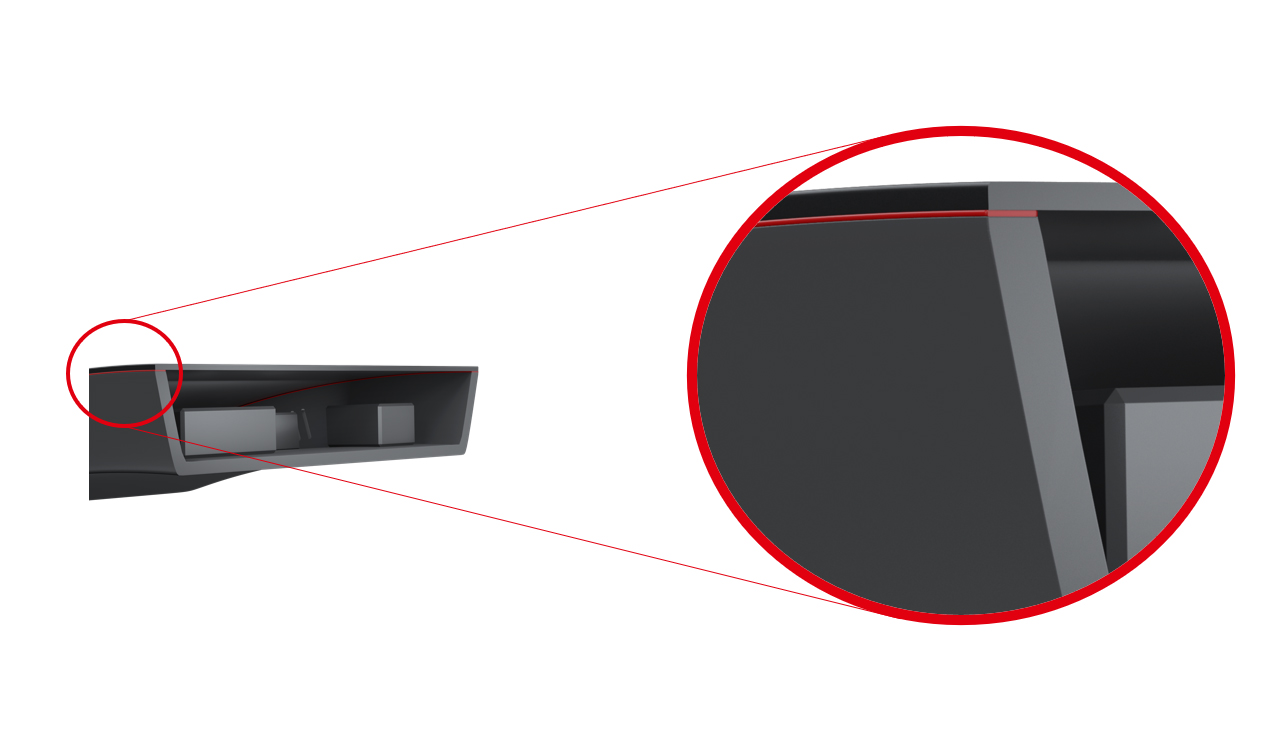
Flexibel anpassbare Dosiermenge zum Ausgleich von Bauteiltoleranzen
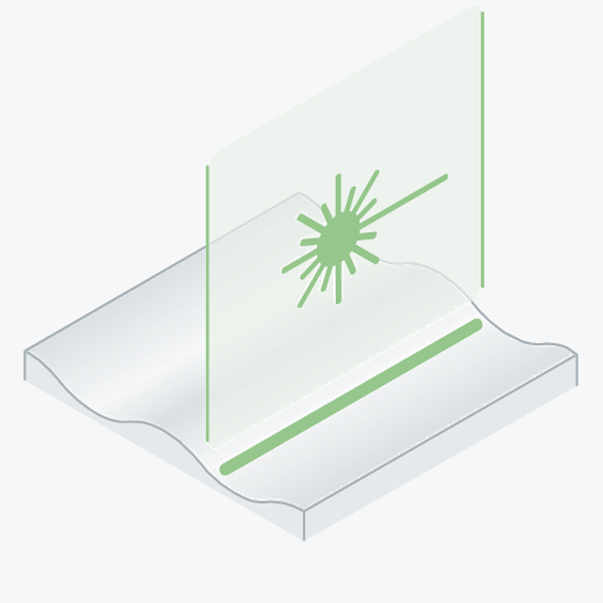
Mit dem von Henkel entwickelten Verfahren, Active Quantity Adjustment (AQA) ist es möglich, die Klebstoffaustragsmenge für die Verklebung von Displays mit dem Gehäuse so zu steuern, dass abhängig von dem jeweiligen Höhenprofil des Bauteils immer die richtige Mengendosierung sichergestellt ist.
Dieses Verfahren ermöglicht es, die Dosiermenge beim Kleberauftrag an die Teilekontur so anzupassen, dass unterschiedliche, herstellungsbedingte Unebenheiten der Verklebungsflächen durch eine genau vorausberechnete und entsprechend exakt dosierte Klebstoffaustragsmenge ausgeglichen werden.
Vor der Dosierung scannt dazu ein 3D-Linienscanner die Geometrie der Bauteile. Die gescannten Daten werden an die speicherprogrammierbare Steuerung (SPS) der Dosiermaschine übermittelt und mit der vorher definierten CAD-Referenz des Bauteils verglichen. Ermittelte Abweichungen werden genutzt, um das Dosierprogramm für den nächsten Kleberauftrag vorausberechnend anzupassen.
Bei der Spritzgussherstellung des Displaygehäuses können wellige Unebenheiten der Verklebungsflächen entstehen. Um dies aus- zugleichen, fährt der Roboter die leicht vertieften Auftragsflächen langsamer ab, damit dort mehr Klebstoff aufgetragen wird, und die leicht erhöhten Flächen fährt er schneller ab, so dass dort weniger Klebstoff dosiert wird.
Durch das AQA-Verfahren können Unterschiede der Maßtoleranzen des Bauteils kompensiert werden. Bei einem Soll-Klebespalt von 1 mm liegt die vorgegebene Toleranz für die Verpressung der Klebespur bei +/- 0,5 mm, wenn Display und Gehäuse gefügt werden.
Da aus Kosten- und Designgründen die Verklebungsränder des Displaygehäuses zunehmend schmaler gestaltet werden, stellt AQA bei Maßtoleranzen sicher, dass die Klebespur auf der Gehäusekontur nach dem Fügen mit dem Displayglas konstant bleibt.
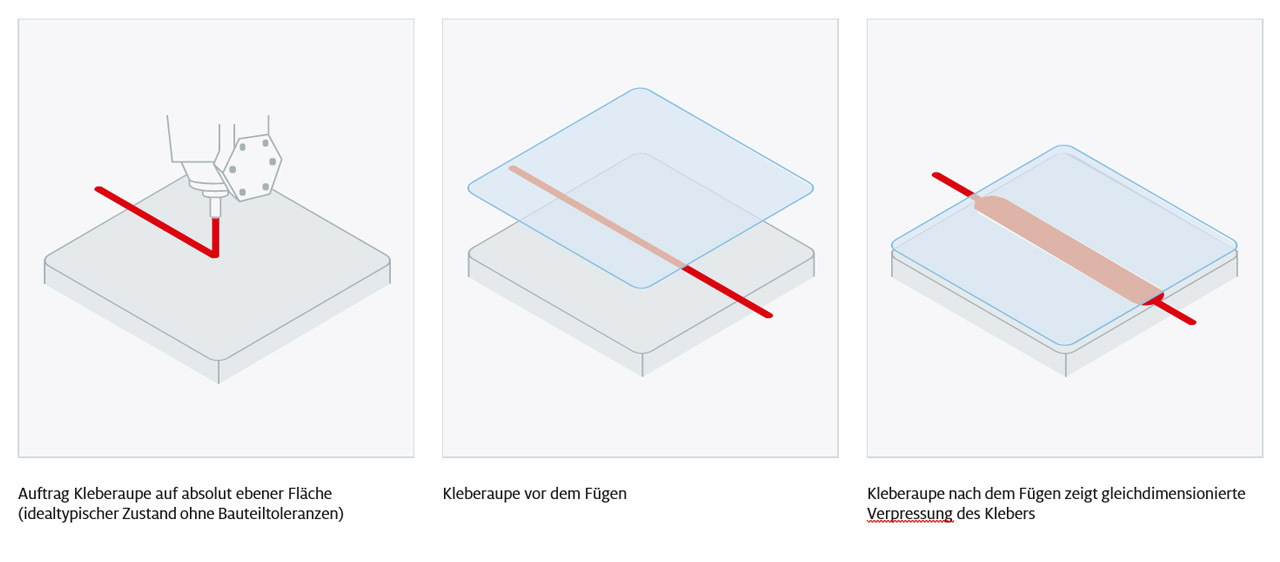
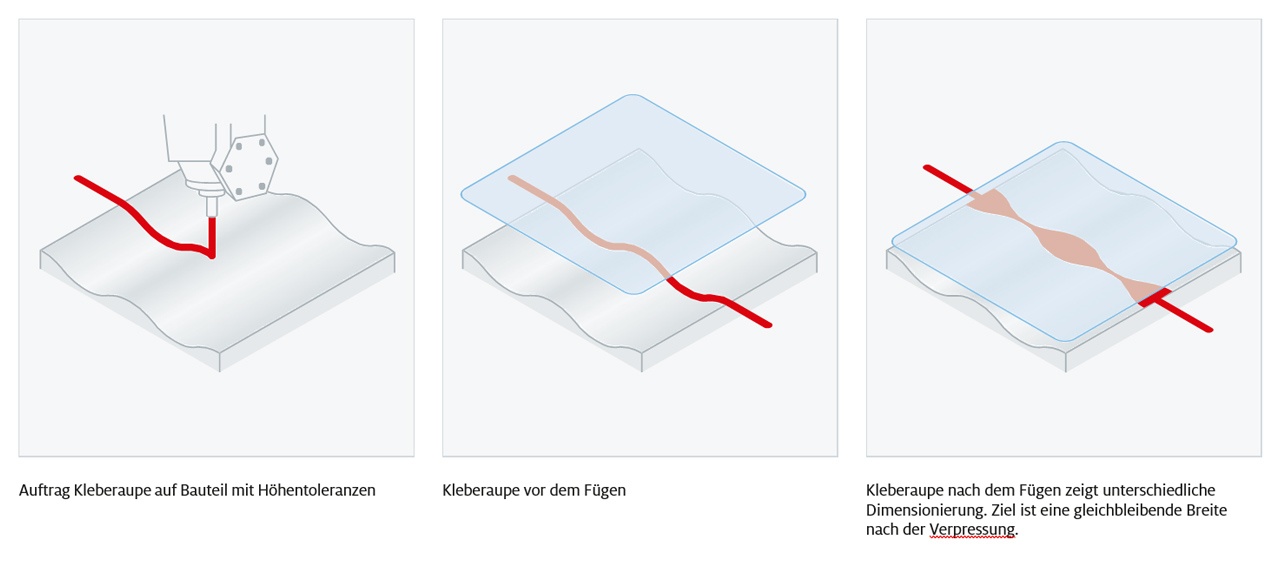
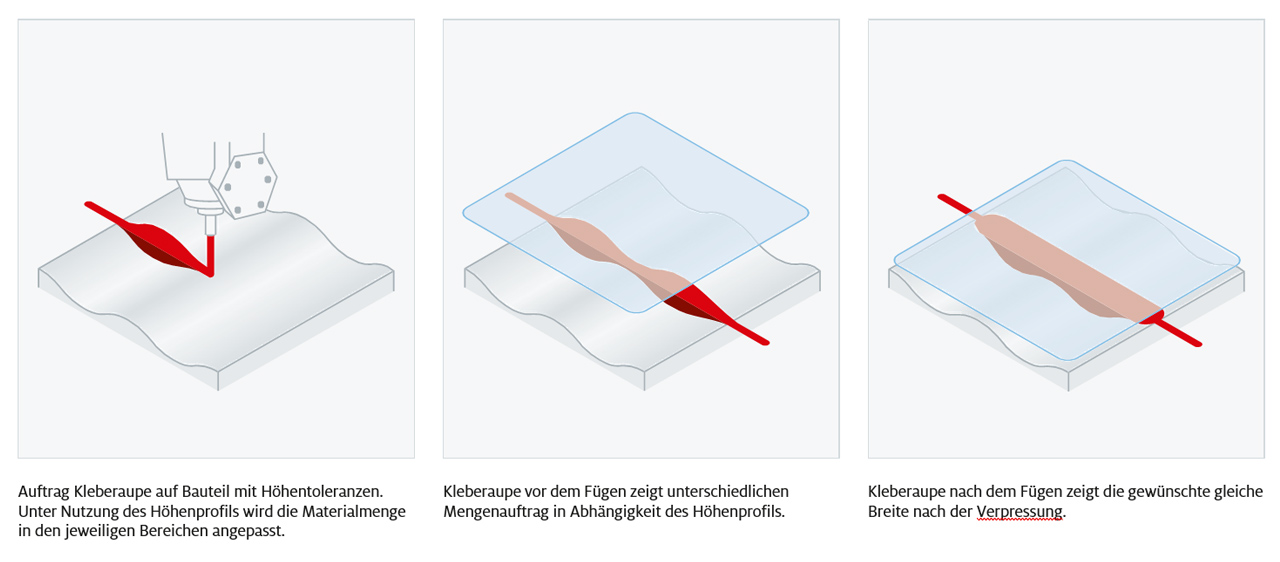
Misch- und Dosieranlagen mit 6-Achs-Roboter und Wechseltisch für die Verklebung von Displaygehäusen
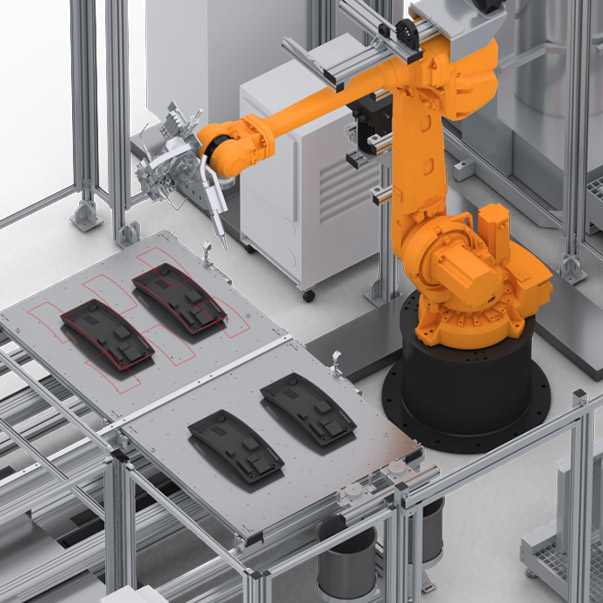
Flexibel und vollautomatisch – ganz nach Ihren Anforderungen
Der vollautomatische Klebstoffauftragsprozess für die Verklebung der Automotive Displays mit dem Gehäuse erfolgt bei der abgebildeten Referenzkonfiguration durch den Einsatz der Misch- und Dosiermaschine DM 502 mit einem 6-Achs-Roboter, der den Präzisionsmischkopf MK 825 PRO führt und dem Wechseltisch WT 1-LEVEL.
Die auf den zwei Aufnahmeplatten fixierten Displaygehäuse werden im Pendelbetrieb in den Arbeitsbereich des Roboters in einer Ebene positioniert. Damit wird ein kontinuierlicher Klebstoffauftragsprozess gewährleistet. Je nach verwendetem Kunststoff des Displaygehäuses kann es notwendig werden, zuvor Plasma auf die Kontur des Gehäuses aufzutragen, um eine verbesserte Klebwirkung zu erreichen. Dafür kann der Roboter optional mit einer Plasmadüse versehen werden.
Zur Überprüfung und Vermessung von Teiletoleranzen des Gehäuses wird in einem separaten Prozessschritt vor dem Dosierauftrag die Oberfläche des Gehäuses von einem 3D-Linienscanner gescannt. Die gemessenen Daten werden an die speicherprogrammierbare Steuerung (SPS) der Dosieranlage übermittelt und mit der vorher definierten CAD-Referenz des Bauteils verglichen. Die ermittelten Abweichungen werden genutzt, um das Dosierprogramm für den nächsten Kleberauftrag vorausberechnend anzupassen.
Der am Roboterarm montierte Mischkopf fährt über die Kontur des Displaygehäuses und trägt konturgenau eine schmale Kleberraupe auf. Dank dem AQA-Verfahren ist es möglich, die Klebstoffaustragsmenge passend zu den Maßabweichungen möglicher Bauteiltoleranzen automatisch anzupassen.
Bei der Spritzgussherstellung des Displaygehäuses können wellige Unebenheiten der Verklebungsflächen entstehen. Um dies auszugleichen, fährt der Roboter die leicht vertieften Auftragsflächen langsamer ab, damit dort mehr Klebstoff aufgetragen wird, und die leicht erhöhten Flächen fährt er schneller ab, so dass dort weniger Klebstoff dosiert wird.
Im Ergebnis entsteht ein die Höhentoleranzen ausgleichender Kleberraupenauftrag, der nach dem Fügen des Displayglases mit dem Gehäuse konstant bleibt.
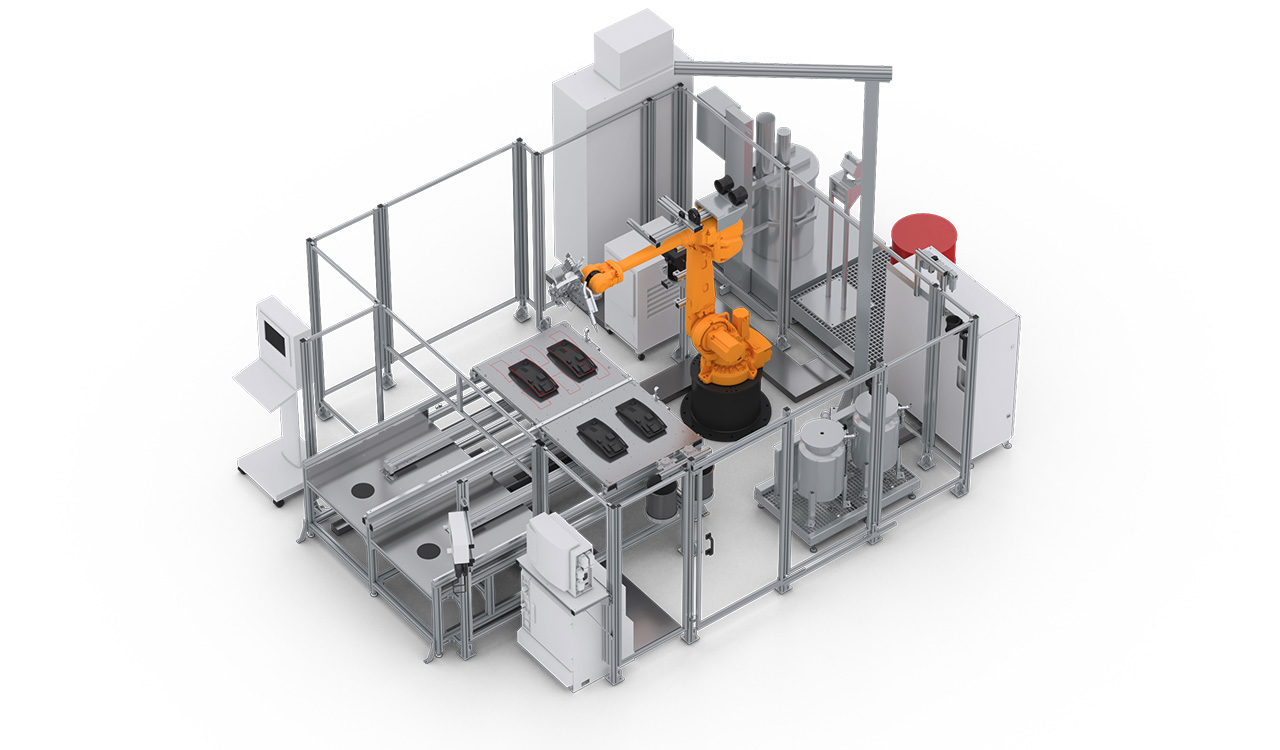
Supply Tap
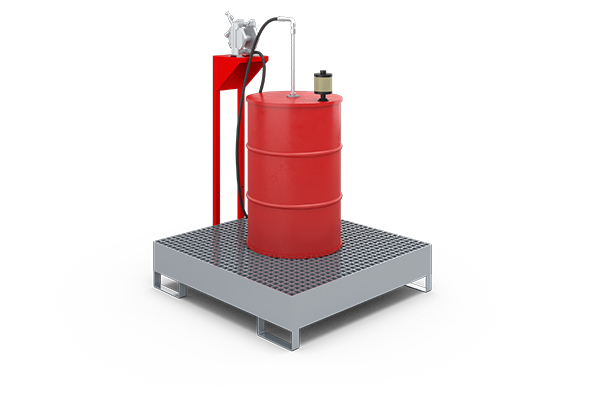
Optional: Automatische Fassnachfüllstation SUPPLY TAP für dünnflüssige Produkte, z. Isocyanate (B-Komponente)
Mehr Informationen zu unseren NachfüllstationenElevator
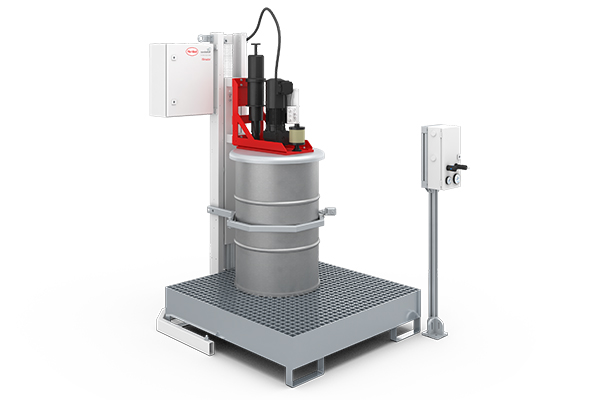
Optional: Automatische Fassbefüllstation ELEVATOR für die A-Komponente mit pneumatischem Lift und Rührwerk
Mehr Informationen zu unseren NachfüllstationenSchaltschrank
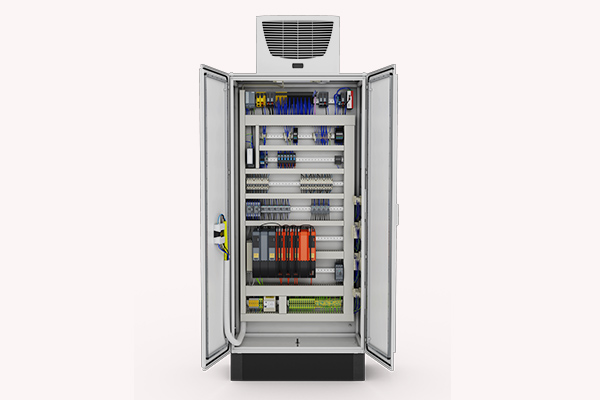
Im Schaltschrank sind Steuerelektronik, Sicherheitstechnik und Industrie-PC untergebracht.
Mehr Informationen zu unseren SchaltschränkenMischkopf 825 PRO
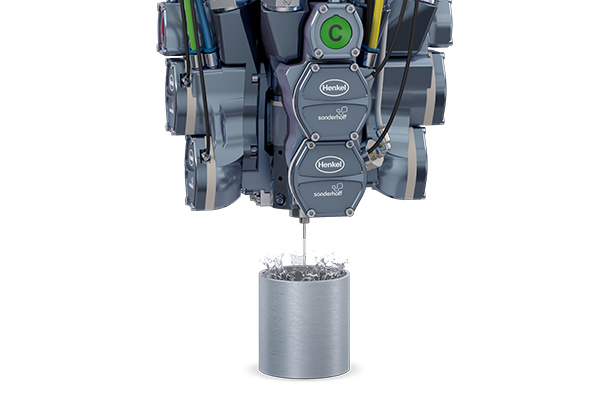
MK 800 PRO Präzisionsmischkopf mit Hochdruckwasserspülung oder alternativem Komponentenspülsystem
Mehr Informationen zu unseren MischköpfenWT 1-LEVEL Wechseltisch
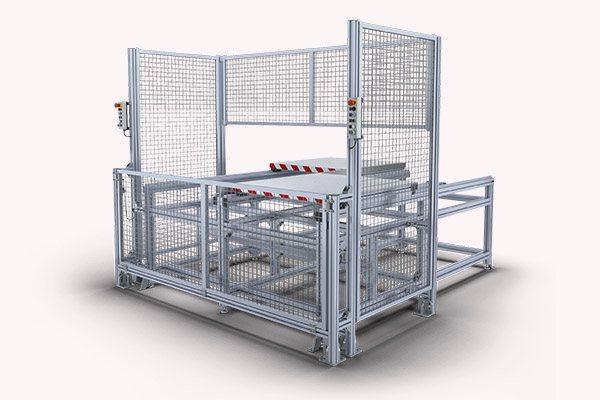
Zwei im Pendelbetrieb arbeitende Pick-up-Platten in einer Ebene
Mehr Informationen zu unseren WechseltischenCONTROL 2
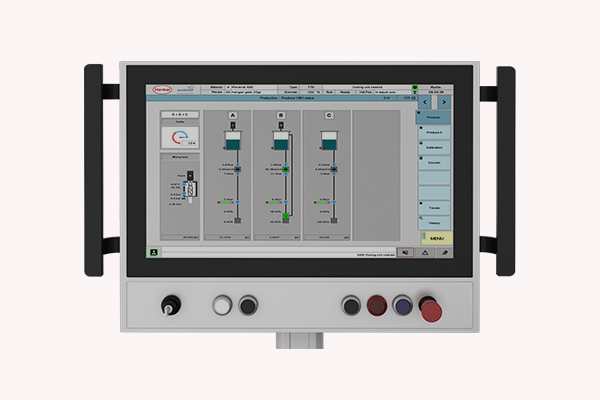
Optional erhältlich: Touchscreen-Bedienpanel CONTROL (21,5“) zur Bedienung des Dosiersystems
Mehr Informationen zu unseren BedienpanelsMobile Panel MP 2
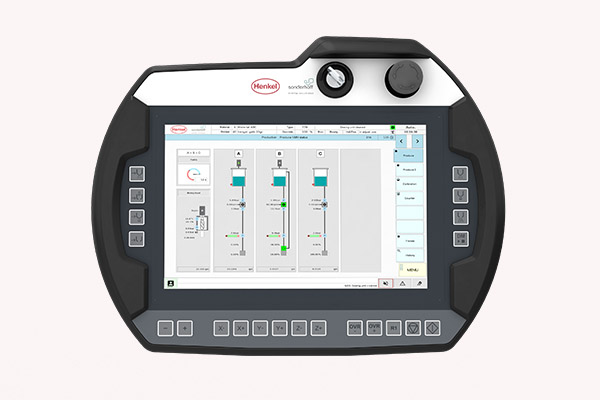
Das multifunktionale Mobile Panel MP 2 (10,1“ WXGA TFT) ermöglicht eine komfortable Bedienung des Dosiersystems.
Mehr Informationen zu unseren BedienpanelsMaterialdruckbehälter
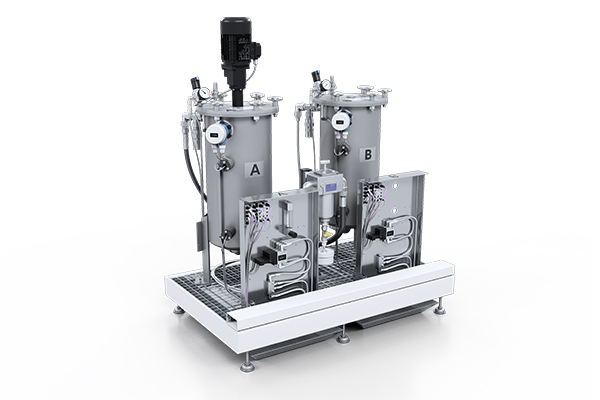
Materialdruckbehälter (24 l oder 44 l, einwandig oder doppelwandig) mit Mindestfüllstandssensoren, auf Gitterrostplattform mit verstellbaren Nivellierfüßen und Abtropfschale
Mehr Informationen zu unseren MaterialdruckbehälternDosiermaschine
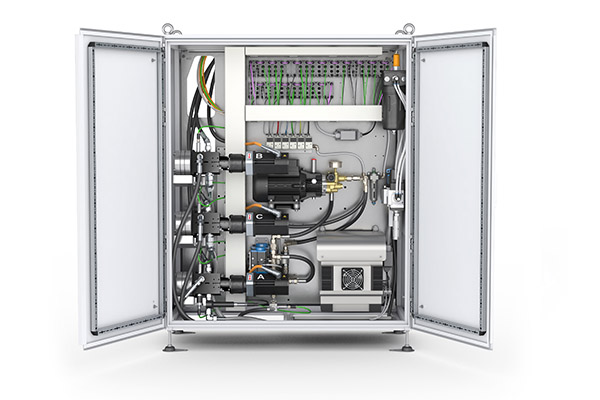
"Der Schrank der Dosiermaschine enthält die Komponenten der Dosierperipherie, z.B. die Dosierpumpen."
Mehr zu unseren Dosiermaschinen