Mit der zunehmenden technischen Weiterentwicklung des Automobils werden Applikationen wie das Aufbringen von Dichtungen, Klebstoffen und Vergussmaterialien auf verschiedene Bauteile immer relevanter. Schaumdichtungen und Verguss werden beispielsweise zum Schutz der Automobilelektronik vor Korrosion durch Feuchtigkeit eingesetzt. Klebstoffe sind für den Leichtbau und die Elektromobilität unverzichtbar.
Anforderungen der Automobilindustrie
In den heute produzierten Automobilen sind Dichtungs-, Verguss- und Klebeanwendungen auf Basis Polyurethan oder Silikon an sehr vielen Stellen zu finden wie z.B. für Bauteile im Motor- und Innenraum, für die Beleuchtung, Karosserie und Elektronik. Sie dienen dort als Staub-, Chemikalien und Feuchtigkeitsschutz sowie zur Vibrationsdämpfung.
Die Anforderungen an die verschiedenen Materialsysteme sind dabei sehr unterschiedlich. Häufig sind diese in einer eigenen Norm, z.B. der DBL 5450/5452 oder der TL 848/577-A, festgehalten. Das Resistenzverhalten der Dichtung gegenüber den verschiedenen Medien ist immer abhängig von Kontaktdauer, Temperatur und der Konzentration des Mediums. Sowohl Polyurethan- als auch Silikondichtungen erreichen in Kombination mit der jeweiligen Gesamtkonstruktion hohe IP-Schutzklassen. Die IP (International Protection)-Schutzartprüfungen geben Aufschluss darüber, wie geschützt elektrische Geräte und Produkte vor verschiedenen Umwelteinflüssen sind. Im Bereich der Medienresistenz und bei hoher Temperatur zeigt allerdings Silikon ein besseres Verhalten. Teilweise kann eine Schädigung der Dichtung auch durch eine konstruktive Änderung des Bauteils verhindert werden. Einfache Einlagerungstests des Dichtungsmaterials im jeweiligen Kontaktmedium lassen daher nur bedingte Rückschlüsse zu, das Dichtverhalten muss immer an der Gesamtkonstruktion getestet und bewertet werden.
Für Anwendungen im Temperaturbereich von -40 °C bis +80 °C eignen sich Polyurethandichtungen zur Abdichtung gegen Staub und Feuchtigkeit. In Bereichen mit einer dauerhaft höheren Temperaturbelastung bis + 250 °C oder für die Abdichtung gegen aggressivere Medien kommen Silikonsysteme zum Einsatz. Hohe Temperaturresistenzen werden im Allgemeinen bei Anwendungen im Motorbereich gefordert. Hier muss jedoch auch kritisch hinterfragt werden, ob die Dichtung tatsächlich dauerhaft einer erhöhten Temperatur ausgesetzt ist, da der Einsatz von Silikondichtungen mit deutlich höheren Kosten verbunden ist.
Bei Henkel wird eine gleichbleibend hohe Qualität der Abdichtung, Verklebung und Versiegelung von Bauteilen bereits durch die richtige Auswahl der Rohstoffe für die Formulierung der Materialsysteme festgelegt. Aber auch die Sicherheit und Genauigkeit sowie ein hoher Bedienkomfort der Misch- und Dosieranlagen sind für einen präzisen und störungsfreien Applikationsprozess der Materialien auf die Bauteile sehr wichtig. Ebenso dafür verantwortlich ist das genaue Zusammenspiel unterschiedlicher Einstellungsparameter und Zusatzfunktionen der Dosiermaschine. Die SONDERHOFF Dosieranlagen ermöglichen zudem eine flexible Anpassung an unterschiedliche Fertigungssituationen in der Automobilindustrie, zu nennen sind hier wechselnde Losgrößen, steigende Variantenvielfalt und Komplexität der Bauteile.
Hohe Prozesssicherheit mit der FIPFG-Dichtungstechnologie
Aufgrund der hohen Automatisierung in der Automobilproduktion muss auch der Materialauftrag stark automatisiert erfolgen. Als Standard haben sich in den letzten Jahrzehnten vor allem geschäumte Dichtungen aus Polyurethan, aber auch Silikon durchgesetzt. Diese Dichtungen werden mit Hilfe von modernen Misch- und Dosieranlagen vollkommen automatisiert mit der FIPFG-(Formed-In-Place-Foam-Gasket)Technologie direkt auf das abzudichtende Bauteil aufgetragen. Der Polyurethanschaum härtet danach unter Raumtemperatur zu einer elastischen Weichschaumdichtung aus. Zwei- und dreidimensionale Teile werden damit genauso gut konturgenau dosiert wie Bauteile mit und ohne Nut. Mit der FIPFG-Technologie werden, bei gleichzeitiger Kostenersparnis aufgrund der Automation, meist wesentlich bessere Dichtungsergebnisse erzielt als mit herkömmlichen, von Hand eingelegten Dichtungen.
Alle für die Qualitätssicherheit relevanten Maschinen-, Material- und Prozessdaten werden bei den SONDERHOFF Misch- und Dosieranlagen automatisch protokolliert und sind damit jederzeit abrufbar. Die FIPFG-Technologie zusammen mit der Nachvollziehbarkeit der vorangegangenen Verarbeitungsabläufe der Anlage stellt eine reproduzierbare Fertigungsqualität der beschäumten Bauteile sicher. Die im Autobau geforderte Nullfehler-Toleranz wird damit ermöglicht. Die hohe Prozesssicherheit wiederum ermöglicht schnellere Produktionsgeschwindigkeiten und damit eine höhere Produktivität in der Automobilindustrie.
Low-Emission Schaumdichtungen für saubere Luft im Auto
In zunehmendem Maße wird für die im Autoinnenraum verbauten Kunststoffe zum Schutz der Fahrzeuginsassen die Einhaltung von Emissionswerten, also die geringstmögliche Abgabe von Stoffen an die Umwelt, gefordert. Die Bauteile aus Kunststoff dürfen auch bei sehr hohen Temperaturen im Auto keine die Gesundheit gefährdenden Schadstoffe ausstoßen. Die geforderten Grenzwerte sind allerdings je nach Herstellernorm unterschiedlich. Im Allgemeinen können sie jedoch als sehr anspruchsvoll bezeichnet werden. Schließlich geht es darum, die Insassen des Fahrzeuges vor schädlichen Stoffen zu schützen.
Die Minimierung von Emissionen wird über die Auswahl der Materialrohstoffe erreicht. Im Falle von Dichtungsschäumen bedeutet dies, dass leicht flüchtige Bestandteile, wie Treibmittel, Öle oder Weichmacher, nicht eingesetzt werden dürfen. Die SONDERHOFF FERMAPOR K31 LOW-EMISSION Polyurethanschäume erfüllen die strengen Grenzwertanforderungen aller wichtigen Automobilhersteller. So erfüllen sie zum Beispiel die Zielwerte der herstellereigenen Spezifikation DBL 5452-13 von Daimler. Hier liegen die Zielwerte für die VOC-Emission bei 100 µg und für das Foggingverhalten bei 250 µg pro Gramm Polyurethan. Damit lässt sich eine hohe VOC-Belastung der Luft im Fahrzeuginnenraum deutlich reduzieren. Irritationen von Augen, Nase, Rachen, der Haut oder allergische Wirkungen werden so vermieden. VOC bezeichnet leicht-füchtige organische Verbindungen („volatile organic compounds“), die nicht immer fest in die Molekülstruktur von Kunststoffen oder Klebern eingebunden sind.
Die Low-Emission Schäume dichten zum Beispiel Filtergehäuse für die Frischluftansaugung im Fahrerraum ab. Sie sorgen für einen Leckage freien Sitz des Filters am Luftansaugkanal in den Klimaanlagen von Autos, so dass keine ungefilterte Luft am Filter vorbei in den Innenraum gelangt.
Durch zu viel VOC in der Luft entsteht oft auch Fogging (Vernebelung). VOC-Teilchen in der Luft bewegen sich dabei aus warmen in kältere Zonen und scheiden sich dort ab. Beim Auto kann das zu einem Beschlagen der Windschutzscheibe oder der Innenseite der Scheinwerfer führen. Im Extremfall könnte dadurch die Verkehrssicherheit der Autofahrer beeinträchtigt werden. Die besonders bei den Autoherstellern und deren Zulieferern nachgefragten Low-Emission Dichtungsprodukte leisten so einen entscheidenden Beitrag, den Fogging-Effekt und VOC-Belastungen der Luft im Autoinneren zu reduzieren.
Fast-Cure Schaumdichtungen für die hoch getaktete Prozessfertigung
Beim Auftrag einer Dichtung auf ein Bauteil ist die Taktzeit, mit der die Bauteile der Misch- und Dosieranlage zugeführt und mit der sie anschließend weiterverarbeitet werden, von sehr großer Bedeutung. Moderne Misch- und Dosieranlagen arbeiten daher schon immer sehr schnell und dabei hochpräzise. Bauteile mit einer gerade aufgetragenen Schaumdichtung benötigen im Allgemeinen jedoch eine gewisse Zeit bis sie weiter verarbeitet werden können. Grund hierfür ist die Vernetzungsreaktion der Materialkomponenten Polyol und Härter. Sie muss erst abgeschlossen sein, bevor die Dichtungsoberfläche klebfrei und ein Teilehandling möglich ist. Der Einbau der Teile kann erst erfolgen, wenn die Dichtung vollständig ausreagiert ist. In der Regel liegen die Aushärtezeiten der Schaumdichtung bei 25 bis 120 Minuten.
Im Automobilbau mit einer hoch getakteten Prozessfertigung ist jedoch ein rasches Teilehandling schon nach wenigen Minuten nötig. Hierfür kann die Klebfreizeit durch Einsatz sog. Fast-Cure-Systeme auf Polyurethanbasis deutlich reduziert werden. Die Oberfläche der SONDERHOFF FERMAPOR K31 FAST-CURE Schaumdichtung ist bei Raumtemperatur je nach Formulierung der Rezeptur schon nach ca. 120 bis 180 Sekunden klebfrei. Die beschäumten Bauteile können so in nachfolgenden Fertigungsprozessen zügig weiterverarbeitet und damit früher eingebaut werden. Das spart Energiekosten, mögliche Kosten für eine Zwischenlagerung von Bauteilen, Investitionen in Temperöfen oder Transferbänder für lange Aushärtestrecken. Die schnellere Weiterverarbeitung und somit frühere Endmontage der Bauteile führen so zu einer erheblichen Zeiteinsparung im gesamten Herstellungsprozess, zu sinkenden Stückkosten und einer effizienteren Fertigung.
Spezielle SONDERHOFF FERMAPOR K31 FAST-CURE Schaumdichtungen erfüllen zudem die technischen Anforderungen der herstellereigenen Normen der Automobilindustrie, von der Daimler DBL 5452-13 über die VW-Norm TL848 bis zur Chrysler/Fiat Norm MY 560. Die schnell reagierenden Fast-Cure Schäume haben generell eine gute Haftung, auf bestimmten Substraten jedoch nur nach vorheriger Vorbehandlung, z.B. durch Primer oder Plasmaaktivierung als Haftvermittler. Die Viskosität der Fast-Cure Schäume kann von flüssig bis pastös flexibel an die jeweilige Bauteilgeometrie angepasst werden. Dank unterschiedlicher Shore-Härten lassen sich Fast-Cure Schäume einfach verbauen.
Typische Anwendungen in der Automobilindustrie
Geschäumte Dichtungen auf Basis von Polyurethan oder Silikon kommen in Fahrzeugen u. a. im Innen- und Motorraum vor, sowie für Teile der Karosserie, Beleuchtung und Auto-Elektronik. Typische Anwendungen für Schaumdichtungen sind beispielsweise Türmodule, welche seit Jahren standardmäßig mit direkt aufgetragenen FIPFG-Dichtungen versehen werden. Die Türmodule nehmen Lautsprecher und elektrische Fensterheber auf, deren Elektronik vor Feuchtigkeit und Staub geschützt werden muss. Weitere Standard-Anwendungen sind die Abdichtung von Kunststoffgehäusen z. B. für Elektronikbauteile oder „dritte Bremsleuchten“, für die häufig rotfarbige Dichtungen gewünscht sind. Polyurethan- und Silikondichtungen können aber auch in anderen Farben eingestellt werden. Ein Beispiel für eine Dichtungsanwendung mit erhöhten Anforderungen ist die Zahnriemenabdeckung. Sie befindet sich im Motorraum und wird wegen der dortigen Temperaturbelastung mit einer Silikondichtung versehen.
Polyurethanklebstoffe für den Autoleichtbau
Dank neuer Werkstoffe und Materialkombinationen sind die Konstruktionsmöglichkeiten im Autoleichtbau vielseitiger geworden. Ein- und Anbauteile im Auto aus thermoplastischen oder duroplastischen Kunststoffen (teilweise faserverstärkt) oder auch Kunststoffbauteile mit metallischen Komponenten werden zunehmend mit 2-Komponenten Polyurethanklebstoffen verklebt. Im Fahrzeugbau ist das eine Vielzahl von Bauteilen, so zum Beispiel GFK-Sandwichaufbauten, KTL beschichtete Metallrahmen für Schiebedächer aus Glas, Teile aus PMMA oder PC mit Kratzfestbeschichtungen, Dachblenden, Zierleisten und Spoiler sowie ABS- oder PP-basierte Heckklappen.
Der Automobilindustrie steht hierfür das umfangreiche Klebstoffportfolio von Henkel zur Verfügung. Zum Beispiel 2-Komponenten Polyurethan-Klebstoffe, sie ermöglichen optimale Kleberesultate für Bauteile aus unterschiedlichen Materialien. Sie erfüllen zudem die hohen Anforderungen an Mechanik und Klimabeständigkeit. Der perfekte Verklebungsprozess erfordert ein präzises Mischen und Dosieren der Kleberkomponenten. Die SONDERHOFF Misch- und Dosieranlagen sorgen dafür, mit der Einhaltung eines genau definierten Mischungsverhältnisses, einer prozessdurchgängigen Dosiergenauigkeit und einer systematischen Prozessüberwachung.
Fazit für die Automobilindustrie
Die Formed-In-Place- (FIP-) Technologie für das vollautomatisierte Auftragen flüssig bis pastöser 2-Komponenten Materialsysteme aus Polyurethan oder Silikon direkt auf die Bauteile hat sich im hochautomatisierten Fahrzeugbau als Fertigungsstandard etabliert. Die dafür eingesetzten SONDERHOFF Misch- und Dosieranlagen lassen sich sehr gut in bestehende Fertigungsstraßen und -konzepte integrieren.
Mit der FIP Dichtungstechnologie werden in hoher Stückzahl sehr unterschiedliche Bauteilgeometrien mit Weichschaumdichtungen, Klebstoffen oder Vergussmassen in reproduzierbarer Qualität präzise dosiert. Die eingesetzten Rohmaterialien werden fast zu 100 % ausgenutzt und es fallen so keine Stanz- oder Verschnittverluste an.
Die Anwendungsmöglichkeiten für geschäumte Dichtungen sind dabei besonders vielfältig und können hervorragend auf die Erfordernisse der Automobilindustrie eingestellt werden. Hierbei geht es neben Emissionsverhalten, Temperatur- und Medienresistenz um das gute Rückstellverhalten einer Schaumdichtung, insbesondere geeignet für das wiederholte Öffnen und Schließen für Wartungszwecke, und die flexible Härteeinstellung und weitere mechanische Eigenschaften wie Zugfestigkeit und Bruchdehnung. Die Forderungen der verschiedenen Automobilnormen müssen dabei ebenso beachtet werden wie die Anforderungen, die sich aus der konkreten Applikation ergeben.
Vielfältige Lösungen für die Automobilindustrie
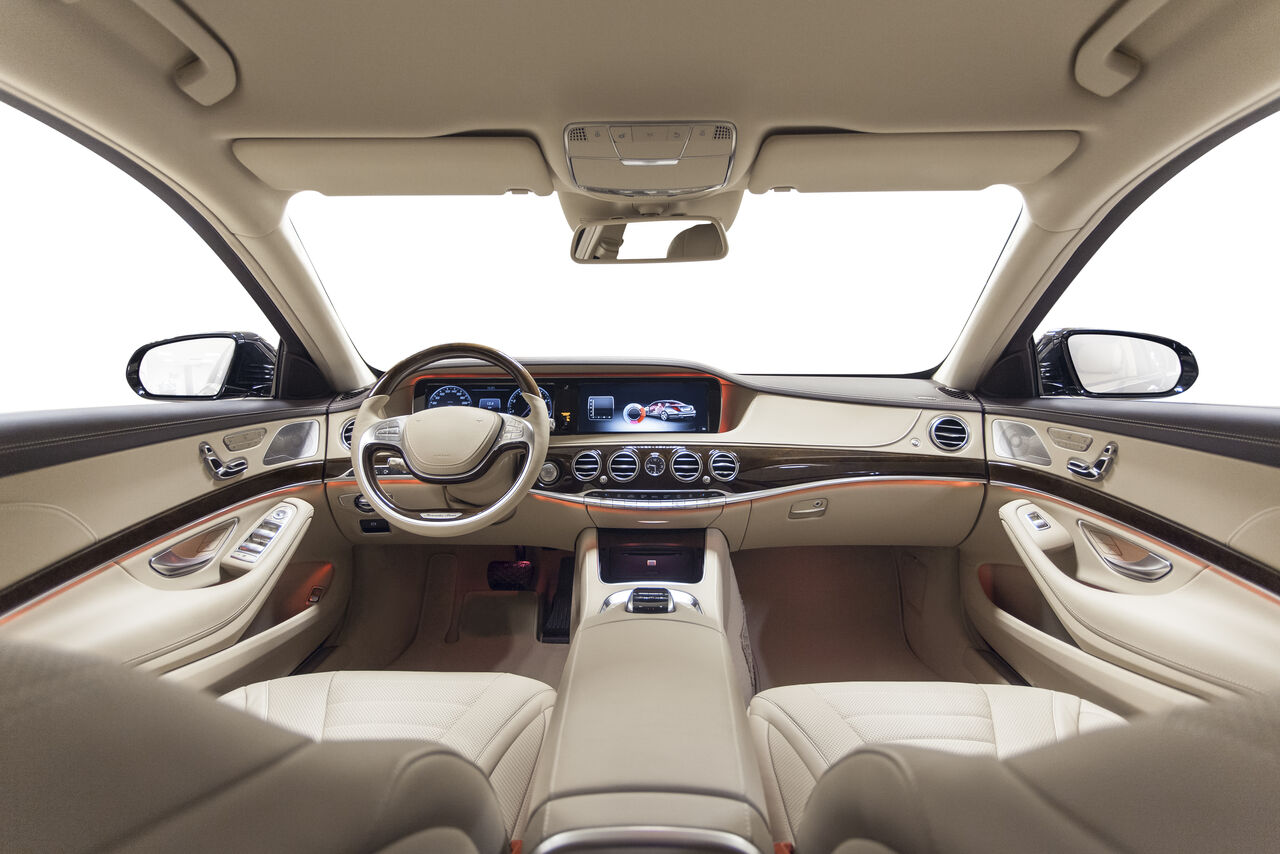
Die Automobilindustrie ist mit jährlich >80 Mio. produzierten Fahrzeugen weltweit einer der größten und wichtigsten Industriezweige. Derart immense Produktionszahlen, die zu einem weltweiten Automobilbestand von > 1 Mrd. Fahrzeugen geführt haben, können nur durch einen hohen Grad an Automatisierung erreicht werden. Henkel bietet der Automobilindustrie mit SONDERHOFF SYSTEM SOLUTIONS den Vorteil, Material, Maschine und Lohnfertigung (Subcontracting) aus einer Hand zu beziehen. Der Kunde wählt das für ihn passende Materialsystem auf Basis von Polyurethan oder Silikon zum Abdichten, Kleben oder Vergießen seiner Bauteile. Dazu erhält er die SONDERHOFF Misch- und Dosieranlage für den vollautomatischen Auftrag dieser 2-Komponenten Materialien. Und dem Kunden steht auch das umfangreiche Klebstoff-Portfolio von Henkel zur Verfügung. Die für das Abdichten, Kleben und Vergießen von Bauteilen eingesetzte Formed-In-Place-(Foam-Gasket) Technologie hat sich vor allem im Automobilbau als effiziente, präzise und wirtschaftliche Fertigungsmethode durchgesetzt, insbesondere bei großen Stückzahlen und komplexen Bauteilgeometrien.