Material systems for sealing plate heat exchangers
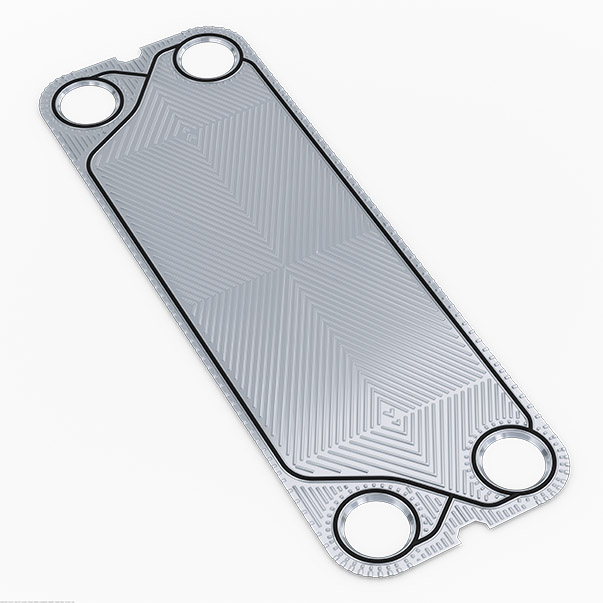
2-component silicone elastomers with high temperature resistance are used for the seamless sealing of plate heat exchangers, and are applied fully automatically by the robot-controlled mixing head of the DM 502 mixing and dosing system from Henkel.
The silicone elastomers usually adhere well to the stainless steel surfaces of the heat exchanger plates. The adhesion can be further improved by pretreatment with primers, plasma or flame treatment.
2-component silicone elastomers for your specific requirements
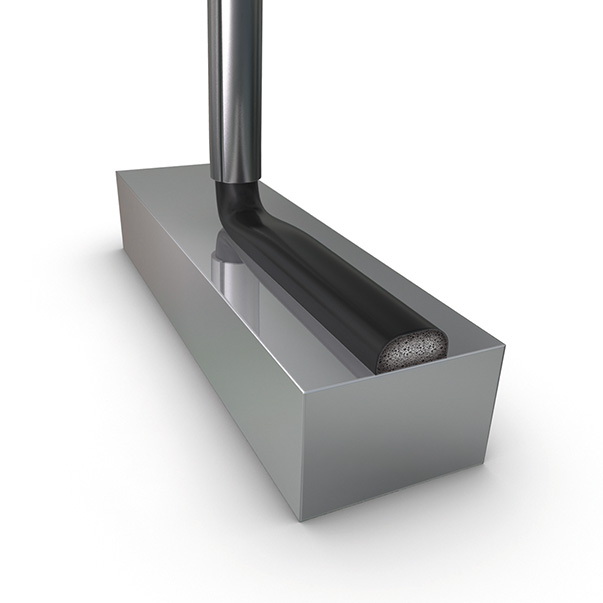
When the viscosity is appropriate, the 2-component silicone elastomers employed generally flow well on the surfaces of the heat exchanger plates.
Our high-precision dosing systems permit the material bead to have a constant height-to-width ratio and seamless completion of the contour despite multiple coupling points. This allows the individual plates of the heat exchanger to be mounted flat on top of each other very easily.
DM 502 mixing and dosing system with 3-axis linear robot for the sealing of plate heat exchangers
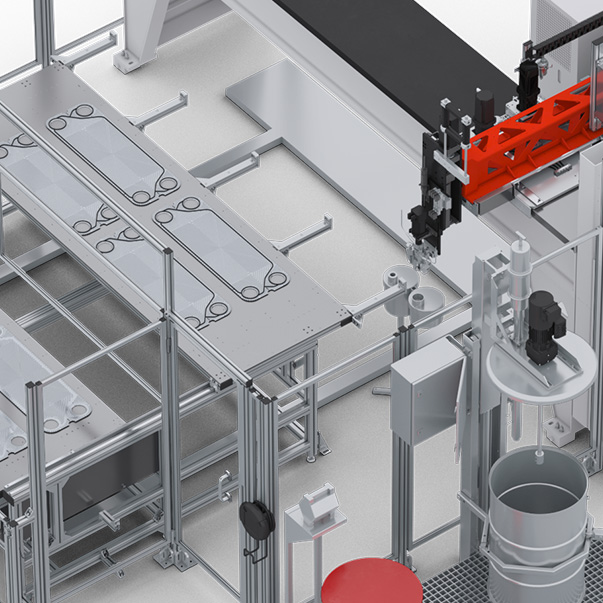
Flexible and fully automatic –
according to your requirements
The reference configuration shown here for sealing plate heat exchangers consists of the DM 502 mixing and dosing system with a 3-axis linear robot and the WT 2-LEVEL shuttle table. The parts are processed in continuous shuttle mode on the pick-up plates, which are positioned above one another on two planes.
Alternatively, we can offer the WT 1-LEVEL shuttle table with two pick-up plates in one plane.
The highly dynamic LR-HD 3-axis linear robot used or, alternatively, the highly efficient LR-HE plus ensures that the MK 825 PRO precision mixing head is repeatedly guided accurately over the component.
The silicone elastomer used is applied here with high dosing accuracy in accordance with the pre-programmed dosing contour to the surface of the heat exchanger plates fully automatically.
Precise dosing of the silicone elastomer, which is applied as a liquid, is crucial for the evenness of the coupling points, which are seamless at several points along the contour. This makes them virtually invisible and they achieve a uniform height-to-width ratio with very low tolerances along the entire course of the silicone elastomer. This is important because when assembled the individual plates of the heat exchanger must lie absolutely flat on top of each other layerby layer before they are pressed together.
The refilling stations ensure material-specific preparation of the material systems used - without contamination with the products to be filled. The optional equipment with an automatic lifting device offers more operating convenience and greater occupational and system safety. In addition, agitators stir the materials and therefore ensure the consistency is homogeneous before they are put into service.
The refilling stations of the modular DM 502 system periphery ensure that material is supplied continuously to the material pressure tanks for fully automatic production processes. Capacitive sensors on the material pressure tanks monitor the filling level and control refilling. This means that the production process is not interrupted in the event of a material change.
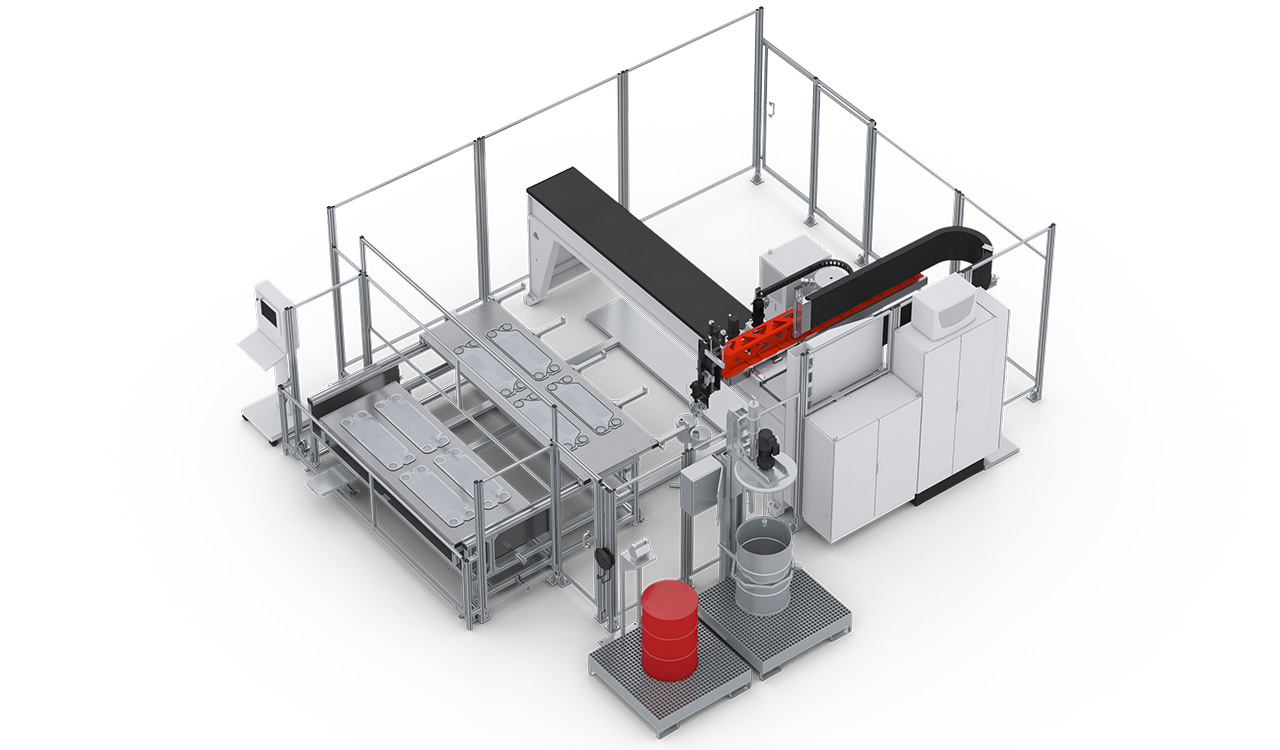
CONTROL 2
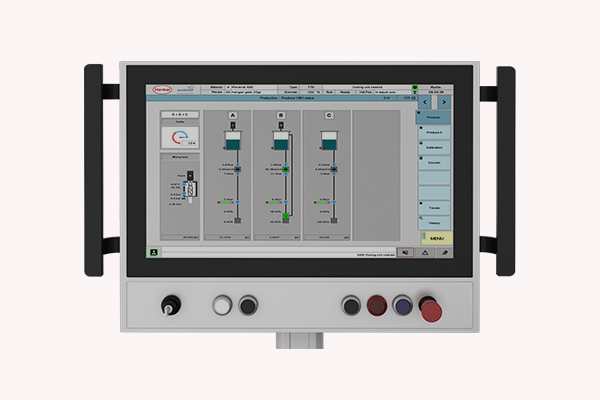
Optionally available: CONTROL touchscreen operating panel (21.5“) for operating the dosing system
More information to our operating panelsWT 1-LEVEL shuttle / sliding table
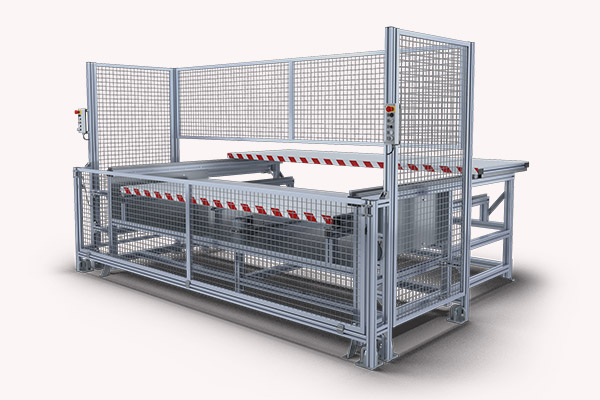
Two pick-up plates operating in pendulum mode in one plane
More information to our shuttle tablesMixing head 825 PRO
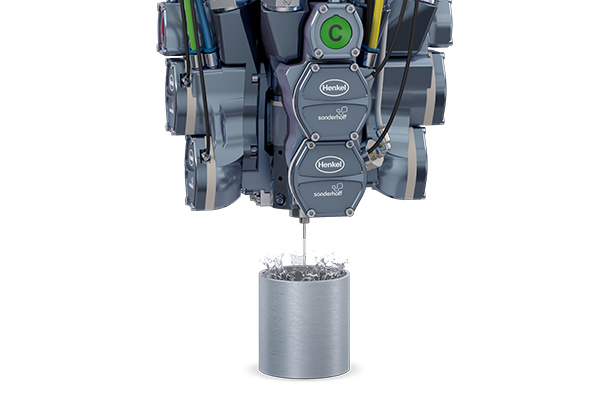
MK 800 PRO precision mixing head with high-pressure water rinsing or alternative component rinsing system
More information to our mixing headsDosing machine cabinet
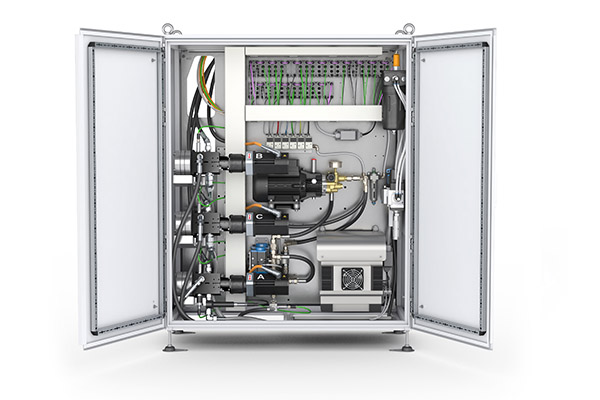
The dosing machine cabinet contains the components of the dosing periphery, e.g. the dosing pumps.
More information to our dosing machine cabinetsControl cabinet
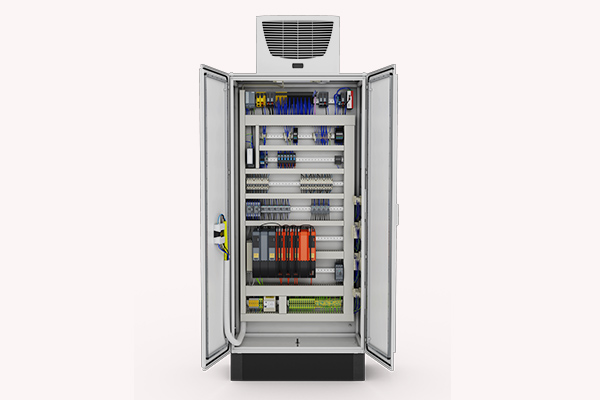
The control electronics, safety engineering and industrial PC are installed in the control cabinet.
More information to our control cabinetsSupply Tap
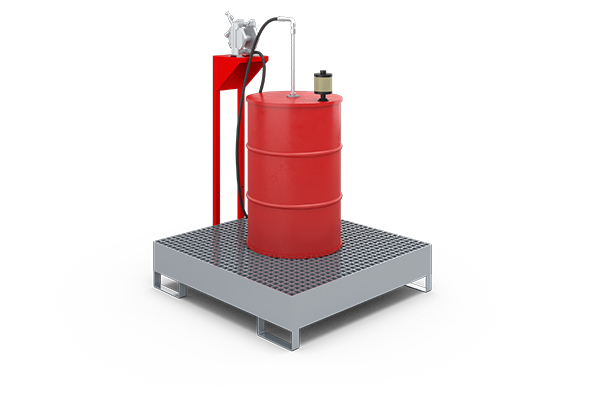
Optional: Automatic SUPPLY TAP drum refilling station for low-viscosity products, e.g. isocyanate (B-component)
More information to our refilling stationsElevator
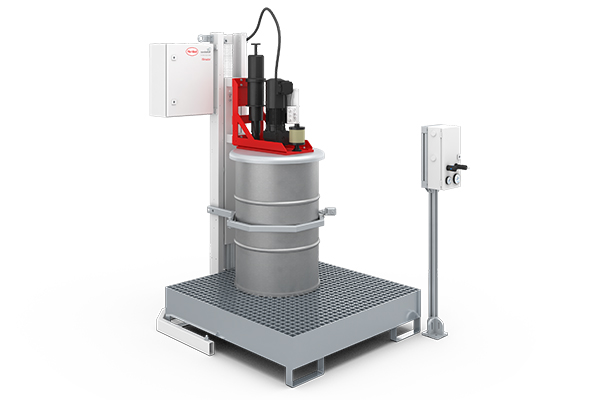
Optional: Automatic ELEVATOR drum refilling station for the A-component with pneumatic lift and agitator
More information to our refilling stations