Tailored sealing solutions for maximum product safety
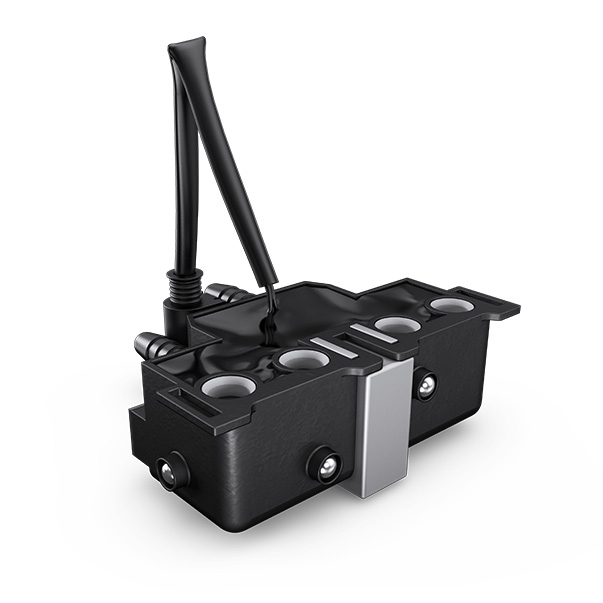
We carry out developments individually for your specific requirements
Electronic components such as windshield wiper electronics or the pins of a connector plug are potted with our polyurethane potting systems. The reference material presented for this purpose, FERMADUR-A-83D10-1-FR and B-N (B component), is a room-temperature curing 2-component polyurethane potting compound.
This material has a temperature resistance of -40 to +80 °C, is particularly mechanically stable and tear-resistant, and is resistant to shrinkage and stress. This increases dielectric strength and protection against moisture and corrosion. As a rule, polyurethane potting provides good adhesion to plastic surfaces.
The FERMADUR polyurethane potting compound is applied to the electronics and connector housings without bubbles using the FIP (Formed-In-Place) technology of our DM 502 mixing and dosing machine via the CNC-controlled mixing head, which features high dosing and repeat accuracy.
Tailored polyurethane potting systems for sealing of electronics or connectors
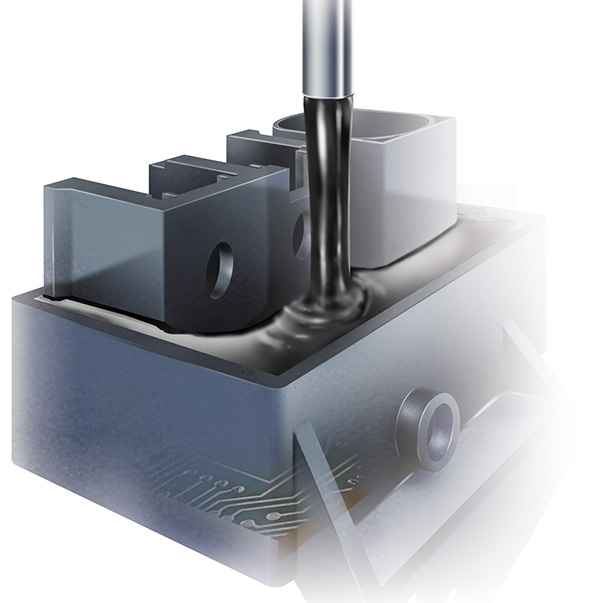
The excellent flow properties of FERMADUR ensure that the gaps between the connector pins in the connector housing are evenly and completely potted without the potting being drawn up on the pins. After dosing, a smooth, even surface is formed which does not show any signs of shrinkage.
This produces, at room temperature or by using an annealing oven for accelerated curing, a compact seal with the desired hardness.
Our potting systems and the fully automated application process for potting electronic housings and connector pins are perfectly matched with one another and adapted to your specific component requirements.
Reference material
FERMADUR A-83D10-1-FR | ||
FERMADUR B-N | ||
Mixing ratio | 3.8 : 1 | |
Pot life time | 5 min. | |
Tack-free time | 6 min. | |
Viscosity of the A component |
11,000 mPas | |
Density of foam | 1.50 g/cm³ | |
Hardness (Shore D) | 85 | |
Temperature resistance | from -40 to + 80 °C | |
Pretreatment | normally not necessary, otherwise primer (for metal) or plasma (for plastic) |
In addition to the reference products, we develop material systems according to your individual requirements. Influencing factors include pot life until start of foaming, curing time, and the viscosity, hardness and adhesion properties.
DM 502 mixing and dosing system with 3-axis linear robot and shuttle table for potting electronics or connectors
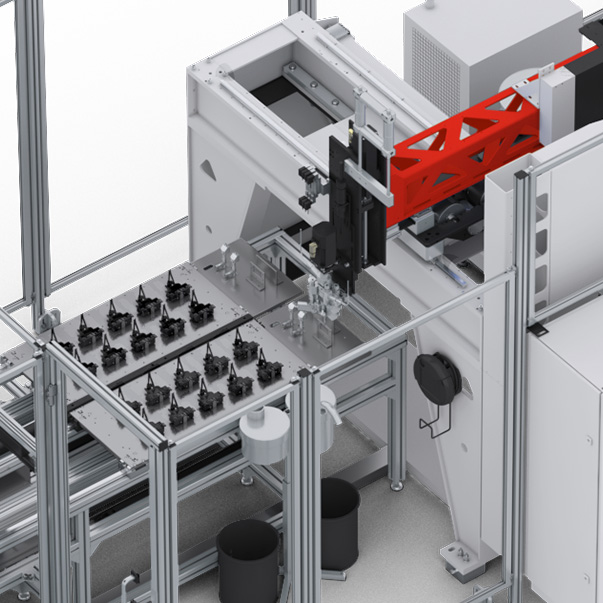
Flexible and fully automatic – fully in line with your requirements
The reference configuration shown here for potting electronic components or connector pins consists of the DM 502 mixing and dosing system with the LR-HE plus 3-axis linear robot and the WT 1-LEVEL shuttle table. Parts are picked up and machined with the two pick-up plates in continuous shuttle mode in one plane.
Parts are placed either by a machine operator, who can also check the parts for quality, or by a Pick & Place Robot. In the latter case, an optionally installed camera or sensor system could also carry out quality control.
The installed highly efficient LR-HE plus 3-axis linear robot ensures that the MK 800 PRO precision mixing head is guided over the component with repeatable accuracy. The FERMADUR potting material is applied fully automatically into the electronics housing or into the connectors with high dosing accuracy and dimensional accuracy. The dosing nozzle reaches as deep as possible into the component to ensure that it is filled from bottom to top without bubbles forming and thereby avoiding air pockets.
Our fail-safe mixing and dosing systems can be operated easily and intuitively without the need for extensive training.
Thanks to the automatic logging of dosing program data, all process data can be traced and evaluated by the machine operator via the CONTROL 2 operating panel while production is running.
In all solutions, our main focus is on extremely reliable plant engineering, minimized maintenance times and consistent dosing quality. As process experts, we support you with tailored advice for the automation of your manufacturing processes.
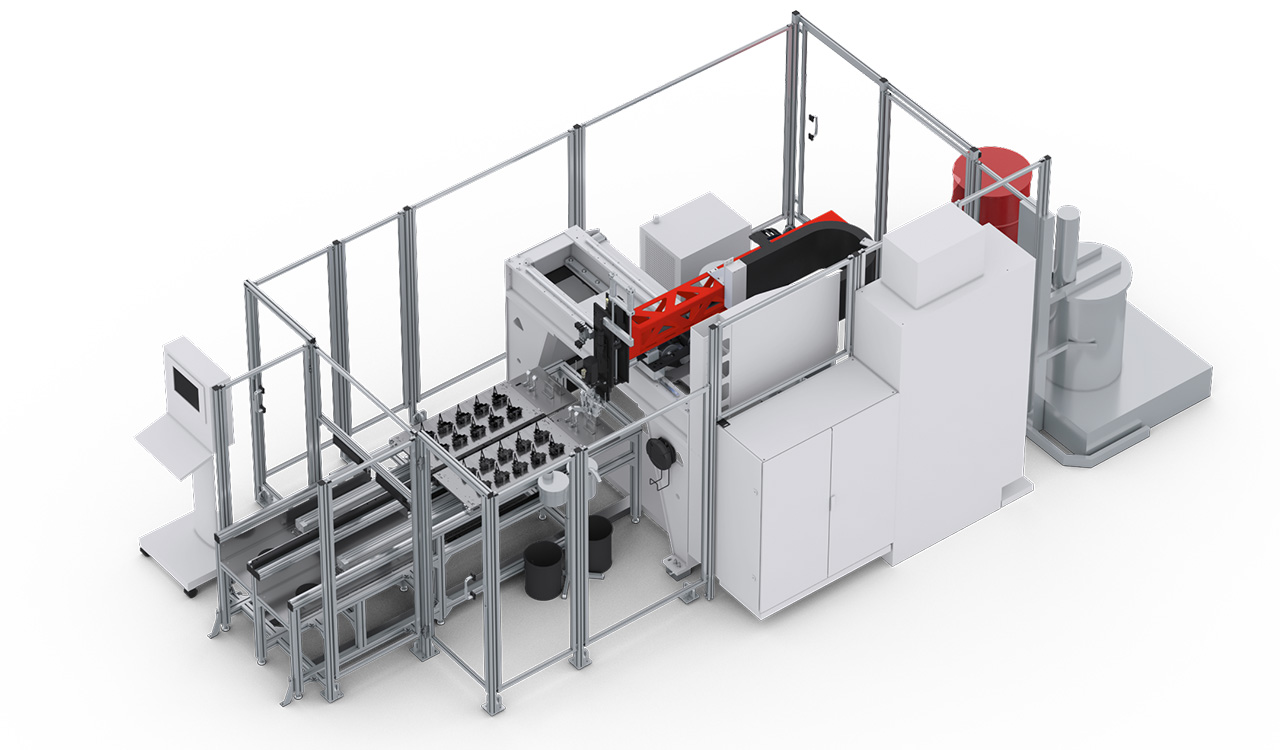
CONTROL 2
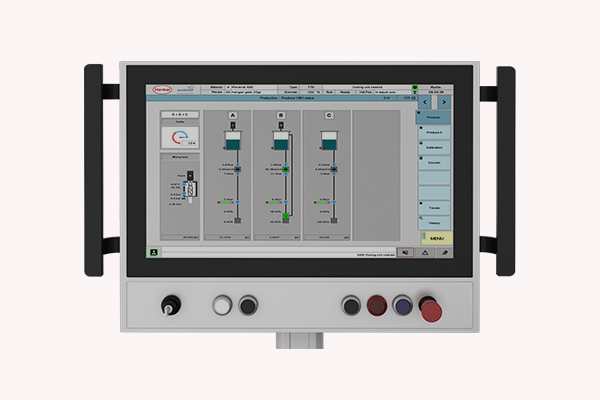
Optionally available: CONTROL touchscreen operating panel (21.5“) for operating the dosing system
More information to our operating panelsMP 2 Mobilpanel
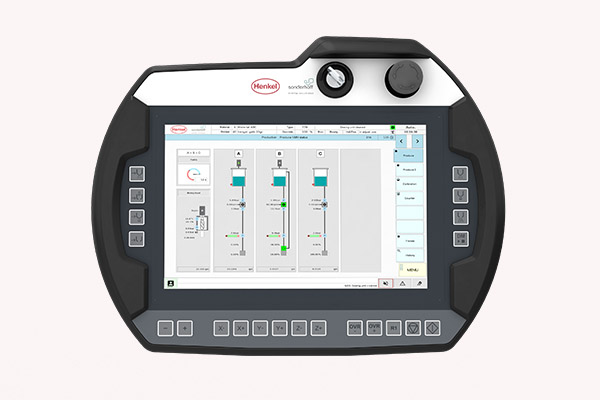
The multifunctional MP 2 mobile panel (10.1” WXGA TFT) enables convenient operation of the dosing system.
More information to our operating panelsWT 1-LEVEL Wechseltisch
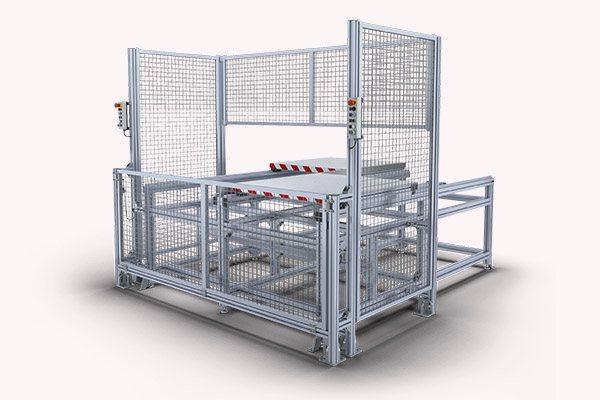
Two pick-up plates operating in pendulum mode in one plane
More information to our shuttle tablesMischkopf 825 PRO
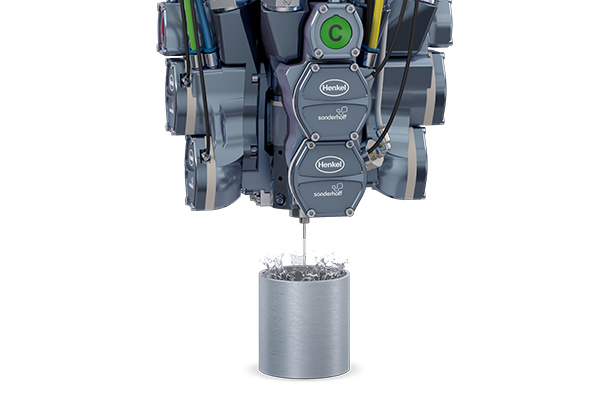
MK 800 PRO precision mixing head with high-pressure water rinsing or alternative component rinsing system
More information to our mixing headsDosiermaschinenschrank
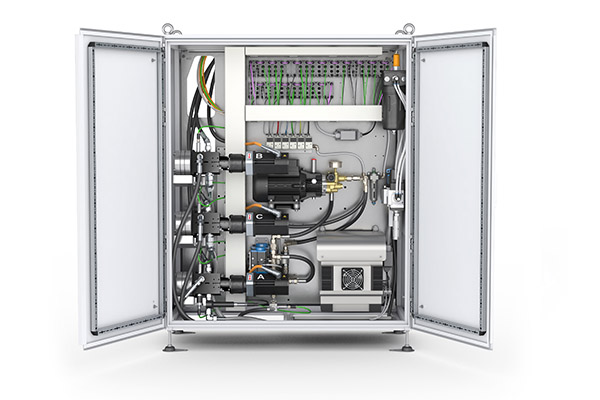
The dosing machine cabinet contains the components of the dosing periphery, e.g. the dosing pumps.
More information to our dosing machine cabinetsSchaltschrank
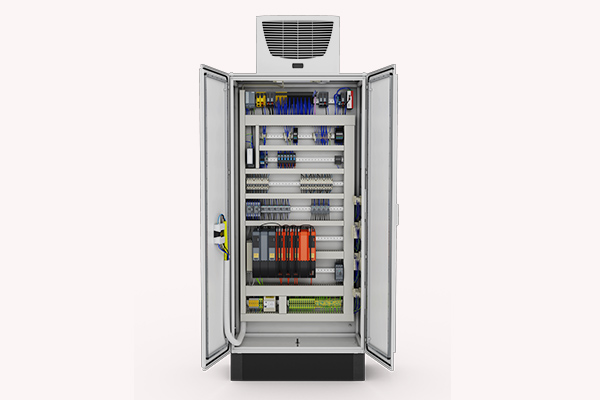
The control electronics, safety engineering and industrial PC are installed in the control cabinet.
More information to our control cabinetsSupply Tap
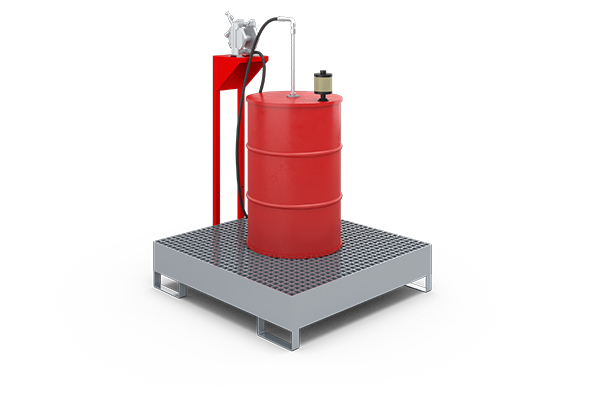
Optional: Automatic SUPPLY TAP drum refilling station for low-viscosity products, e.g. isocyanate (B-component) Automatische Fassnachfüllstation SUPPLY TAP für dünnflüssige Produkte, z. Isocyanate (B-Komponente)
More information to our refilling stationsElevator
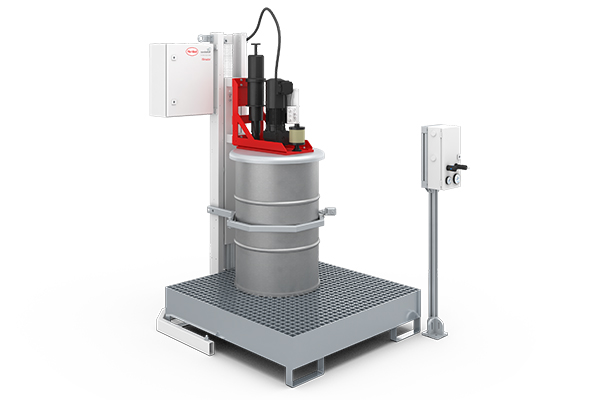
Optional: Automatic ELEVATOR drum refilling station for the A-component with pneumatic lift and agitator
More information to our refilling stations