Customized solutions for sealing of panel filter frames
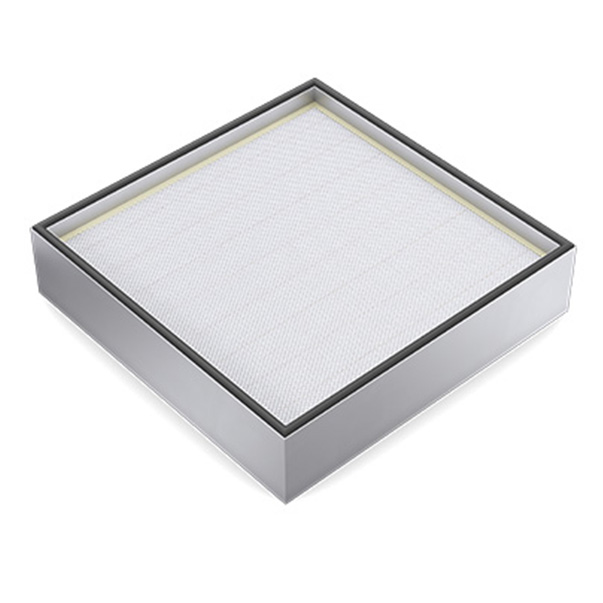
Differently soft polyurethane sealing foams for low closing forces and compensation of component tolerances
The reference materials presented here have been used by leading manufacturers of panel air filters for many years, and are tried and tested. The 2-component polyurethane sealing foams of the FERMAPOR K31 product family are available for this purpose in different viscosities, ranging from liquid for the frame groove to thixotropic for flat or three-dimensional application surfaces.
The thixotropic sealing foams are available in a soft and also slightly harder versions.
Alternatively, we can also customize our material systems to meet your component requirements and specifications. Influencing factors include pot life until start of foaming, curing time, and the viscosity, hardness and adhesion properties.
Thanks to the mixed cell foam structure, closing forces of the foam gasket are low during installation of the panel filters.
Animation of sealing and bonding of panel filter frames with Sonderhoff DM 502 and conveyor belt for feeding parts
Bespoke solutions to seal panel filter frames
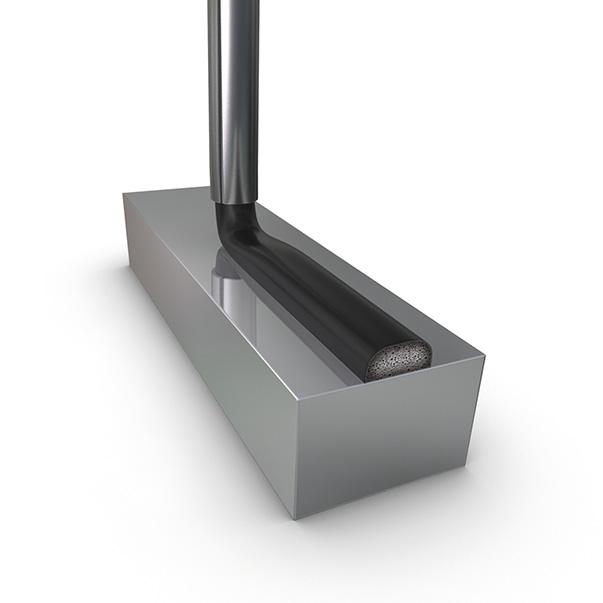
When installing the air filter in the air-conditioning system, for example, the tongue-and-groove design ensures that the filter frame with foam gasket is firmly connected to the counterpart on the filter seat.
The foam gasket compensates for component tolerances during sealing and thus prevents air drawn in from outside from flowing past the filter unfiltered due to possible leakage.
Repeated installation and removal of air filters with remaining sealing effect of foam gasket
The excellent shape recovery characteristics of the FERMAPOR K31 polyurethane foam gasket allow repeated installation and removal of the air filters of air conditioning systems for maintenance purposes without reduction or even loss of the sealing effect (tested according to DIN EN ISO 1856).
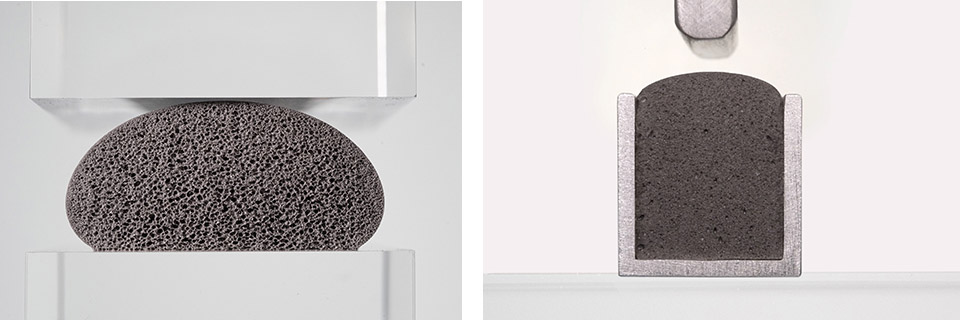
Cross-section of a polyurethane foam bead – unpressed (without groove)
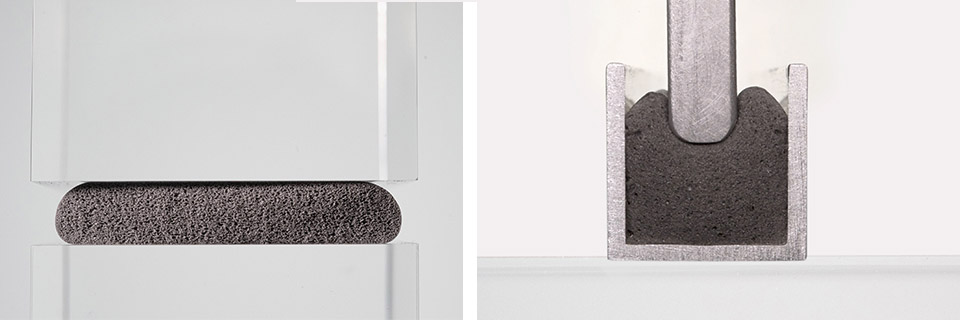
Cross-section of a polyurethane foam bead in the groove with 50 % compression
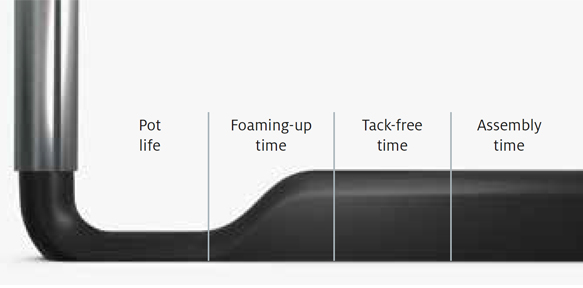
The different reaction phases of the sealing foam in the chronological sequence
Reference material
thixotropic (soft version) |
thixotropic (harder version) |
liquid / soft for frame groove |
||
FERMAPOR K31 | A-9025-2-VP2 | A-6045-2-B-MX | A-9675-5-VP | |
FERMAPOR K31 | B-4 | B-4 | B-4 | |
Mixing ratio | 4.5 : 1 | 4.0 : 1 | 4.5 : 1 | |
Pot life time | 33 sec. | 28 sec. | 40 sec. | |
Tack-free time | 5 min. | 3 min. | 7 min. | |
Viscosity of the A component |
44,000 mPas | 56,000 mPas | 1,500 mPas | |
Density of foam | 0.20 g/cm³ | 0.28 g/cm³ | 0.23 g/cm³ | |
Hardness (Shore 00) | 35 | 55 | 43 | |
Temperature resistance | from -40 to + 80 °C | from -40 to + 80 °C | from -40 to + 80 °C |
In addition to the reference products, we develop material systems according to your individual requirements. Influencing factors include pot life until start of foaming, curing time, and the viscosity, hardness and adhesion properties.
Mixing and dosing system DM 502 with 3-axis linear robot for the sealing of panel filter frames using seal foam or gel seals
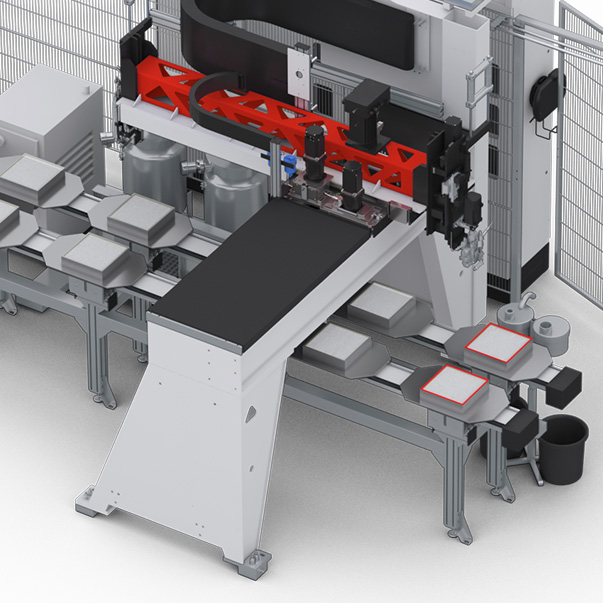
Flexible and fully automatic – fully in line with your requirements
In the reference configuration of the DM 502 mixing and dosing system shown here, the filter frames are fed to the dosing station on a transfer belt passing under the 3-axis linear robot.
The LR-HD 3-axis linear robot handles the contour-accurate CNC-controlled movement of the precision mixing head above the component.
Alternatively, the DM 502 can also be used as a sliding table system with the LR-HD linear robot and the WT 1-LEVEL shuttle table.
The MK 800 PRO precision mixing head of the DM 502 applies the polyurethane sealing foam to the frame contour fully automatically using the FIPFG process with high dosing and repeat accuracy.
For frame grooves, the liquid version FERMAPOR K31-A-9675-5-VP is used; for filter frames without a groove, the thixotropic sealing foams FERMAPOR K31-A-9025-2-VP2 (soft version) or FERMAPOR K31-A-6045-2-B-MX (somewhat harder version) are used.
For a comprehensive filter product portfolio, the DM 503 dosing system can alternatively be used, which is designed for three components. This dosing system can produce panel filters with a single seal on a flat surface, as well as panel filters with a groove design and using two different sealing systems.
The applied material foams, expanding to several times its original volume, and forms an elastic soft foam gasket with the desired foam hardness at room temperature. After the dosing cycle, the coupling point of the foam gasket closes seamlessly and is almost invisible. It achieves consistently tight sealing through uniform compression over the entire contour of the panel filter frame.
The decisive factors for the low water absorption of the foam gasket in its installed state are the fine-cell foam structure and the degree of compression.
The fail-safe DM 502 mixing and dosing machine can be operated easily and intuitively without much training. The dosing and process data are recorded, and can thus be tracked and evaluated by the machine operator via the CONTROL 2 operating panel.
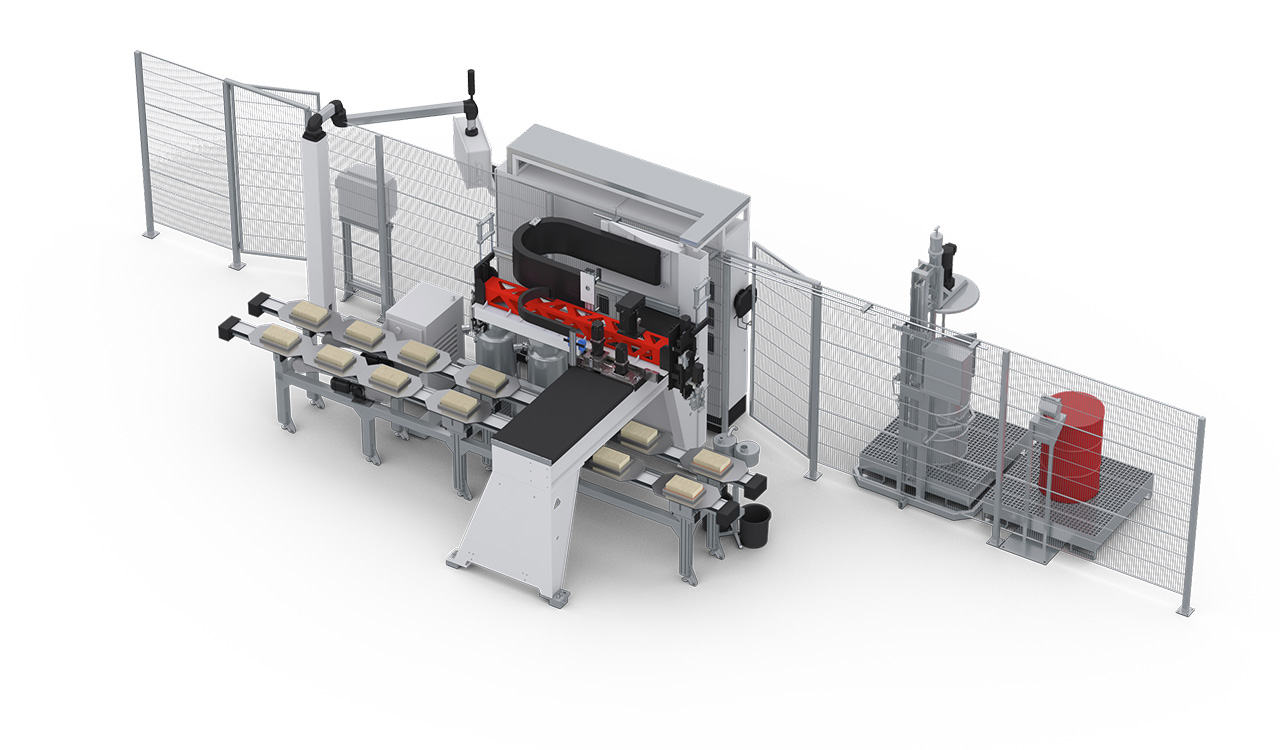
Elevator
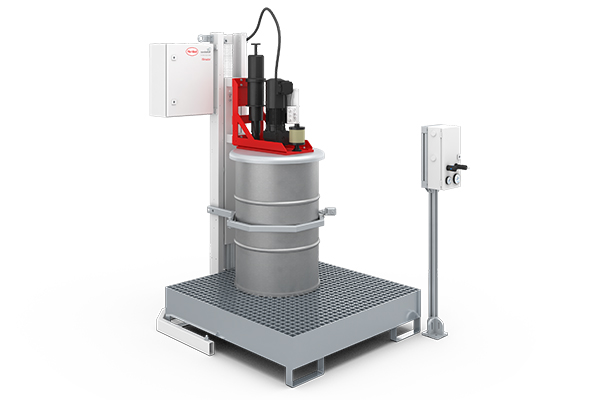
Optional: Automatic ELEVATOR drum refilling station for the A-component with pneumatic lift and agitator
Mehr Informationen zu unseren NachfüllstationenSupply Tap
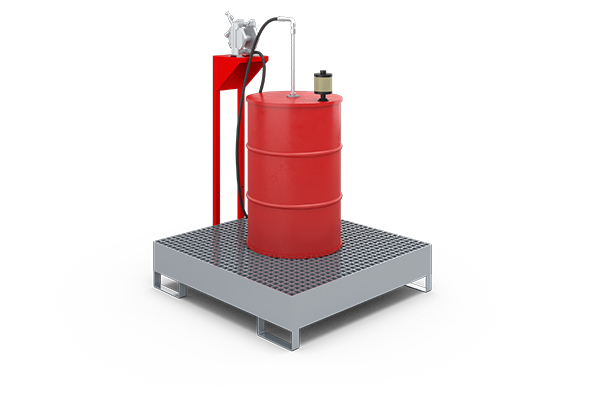
Optional: Automatic SUPPLY TAP drum refilling station for low-viscosity products, e.g. isocyanate (B-component)
Mehr Informationen zu unseren NachfüllstationenMixing head 825 PRO
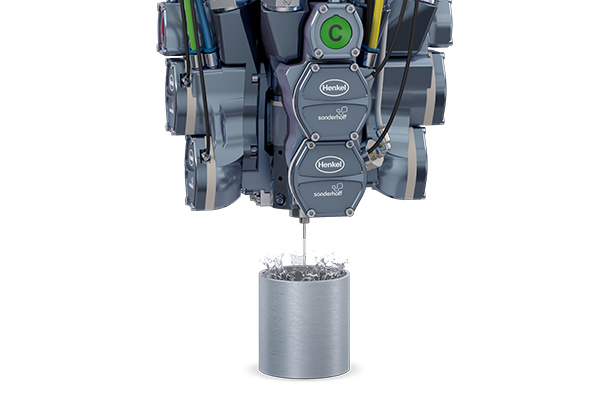
MK 800 PRO precision mixing head with high-pressure water rinsing or alternative component rinsing system
More information to our mixing headsControl cabinet
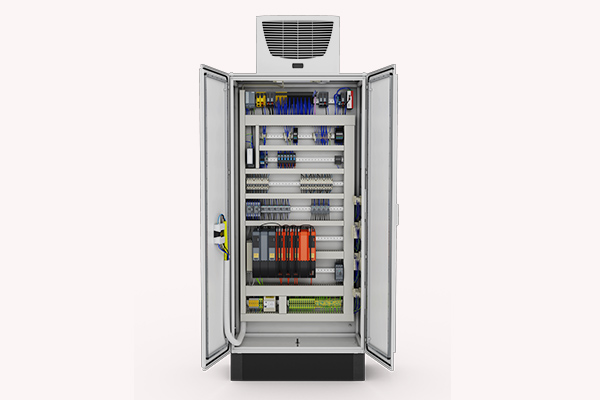
The control electronics, safety engineering and industrial PC are installed in the control cabinet.
More information to our control cabinetsDosiermaschinenschrank
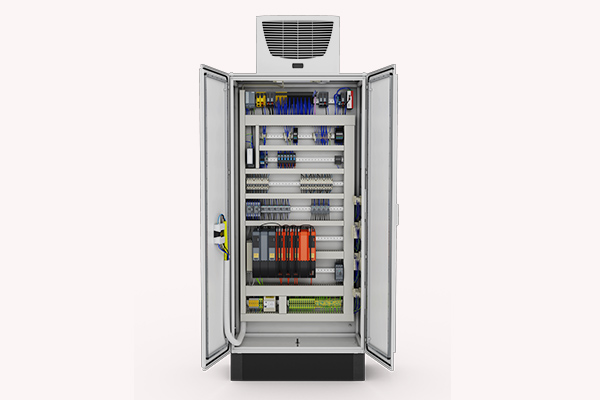
The dosing machine cabinet contains the components of the dosing periphery, e.g. the dosing pumps.
More information to our dosing machine cabinetsCONTROL 2
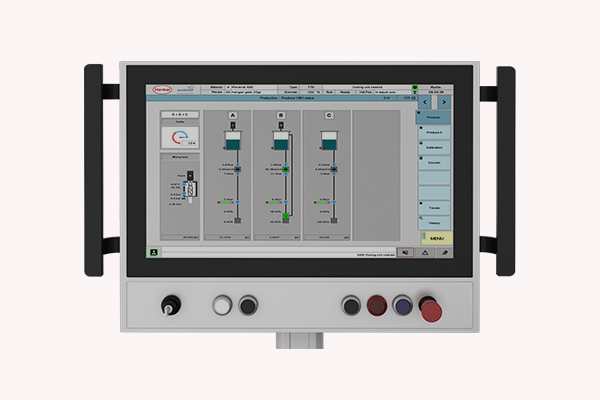
Optionally available: CONTROL touchscreen operating panel (21.5“) for operating the dosing system
More information to our operating panelsMP 2 Mobile panel
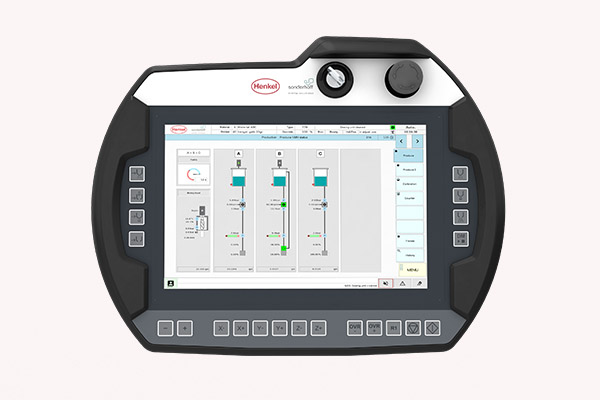
The multifunctional MP 2 mobile panel (10.1” WXGA TFT) enables convenient operation of the dosing system.
More information to our operating panels