FERMASIL
Silicone systems for extreme usage conditions
FERMASIL is the 2-component silicone system for the manufacturing of soft elastic silicone elastomers and silicone foam sealings for extreme usage conditions.
Using FIPFG dispensing technology (Formed-In-Place-Foam-Gasket), FERMASIL is applied directly to the part and cures there at room temperature.
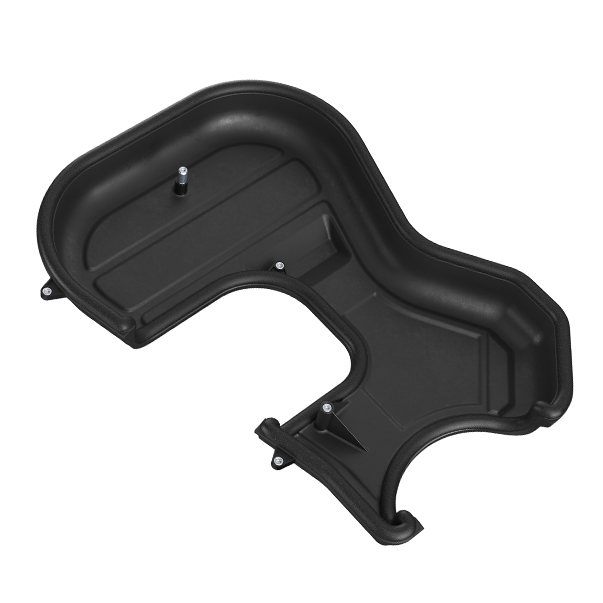
Chemical reaction and FERMASIL properties
The FERMASIL silicone foam seal systems consist of a silicone (A-component) and a cross-linking B-component, which are mixed with each other in a redetermined mixing ratio. After mixing the components, most systems react by their own at room temperature and generate a soft elastic silicone foam sealing or permanently elastic silicone elastomers.
FERMASIL is processed using low pressure mixing and dosing machines for two components. Suited for silicone sealants in dynamic or static mixing systems. Henkel recommends dynamic mixing systems for increased ease of material processing.
FERMASIL can be used at a constant temperature from -60 up to +180 °C and for a short time up to +350 °C, while maintaining its softness and flexibility at any time. Due to its closed cell structure, FERMASIL does not absorb water and is suitable for use in tropical or damp environments. It is also highly resistant to other chemicals (e. g. commercial cleaning agents, alcohols, diluted acids and lyes, brake fluids, and cooling agents).
Henkel can draw on the variety of more than 200 application-specific formulations of the FERMASIL product family.
Physical and chemical Properties* | ||
---|---|---|
Property | FERMASIL | |
Appearance | White, grey or black, other colors upon request (also transparent) | |
Hardness | Gel-like up to Shore A possible | |
Compression load deflection (25% compression) | From 20 to 150kPa (at 25 % compression) | |
Density | From 0.25 g/cm³ to 2 g/cm³ | |
Temperature resistance | From -60 °C to +180 °C (temporary up to +350 °C) | |
Tensile strength | Up to 4.5 MPa [N/cm²] | |
Elongation at break | Up to 600 % | |
Compression set (DVR) | Greater than 97 % (depending on test conditions) | |
Water absorption | < 1 % | |
Flame retardancy | Up to UL 94 V-2 possible | |
Viscosity of the A component: | from 1,000 mPa·s (liquid) to 250,000 mPa·s (highly pasty) | |
Optional features |
E.g. UL 50 conformity, UV resistant, ingress protection class up to IP69K and NEMA 4-6p (achievable with suitable component design), good chemical resistance |
Broad spectrum of characteristics of FERMASIL
Depending on customer requirements, FERMASIL systems can express many different characteristics. Different part applications are protected effectively in extreme surroundings. Numerous FERMASIL product family recipes are available for this.
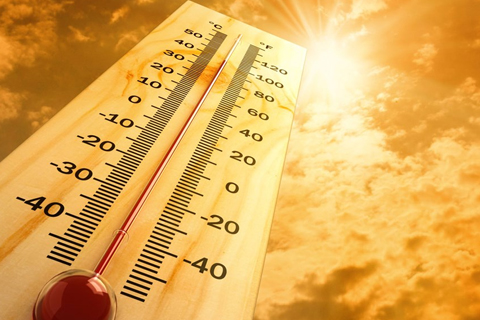
High temperatures
The different softness grades and flexibilities of FERMASIL silicone systems are maintained even at long-term temperatures of -60 to +180 °C, in special cases to 250 °C, and for short periods even to +350 °C.
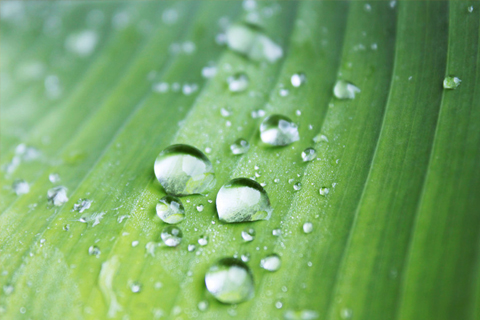
Very low water absorption (< 1 %)
Because of the closed-celled structure of silicone foams, they are tropicalised and wet room safe; infiltration protection to IP 69K and NEMA 4-6p are possible.
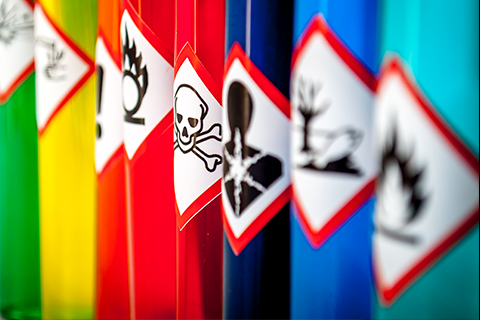
High chemical resistance
FERMASIL silicone systems are resistant to many chemicals (e. g. Common cleaning materials, alcohols, dilute acids and alkalis, brake fluids, oils and lubricants, coolants) and are low-fogging.
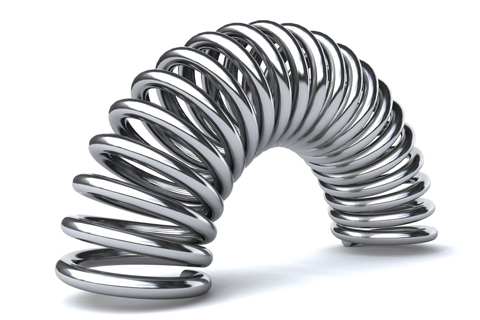
Flexibility
Ease of flow, reactivity and colour can be multifariously varied.
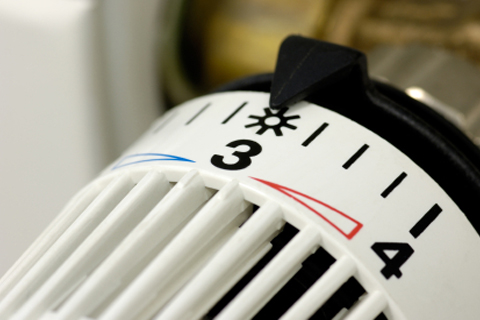
Curing at room temperature
FERMASIL silicone foams cure on the component at room temperature in a time range from approx. 20 minutes to around 12 hours, becoming a soft foam seal. The part can then be sent on to further processing.
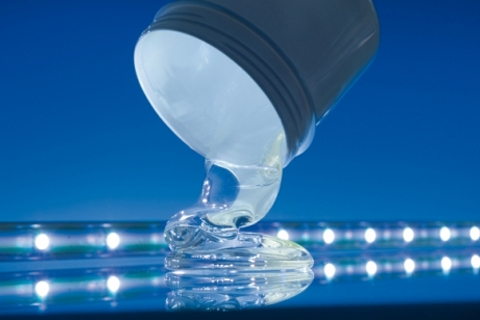
Crystal clear or translucent silicone potting
Temperature stable to 180 °C, very high tear resistance and flexural strength (example extension at break 600 %), UV-stable
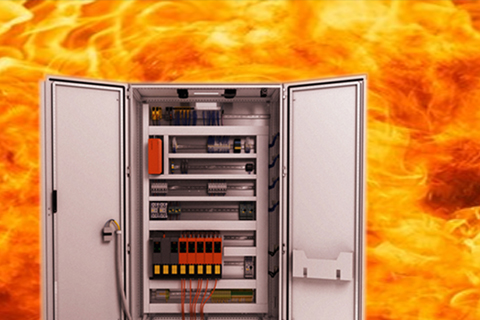
Flame protection in accordance with UL 94 V-2
FERMASIL silicone systems can be equipped with UL 94 V-2 flame protection; any flame after this is extinguished within 10 seconds, with max. 30 seconds afterglow.
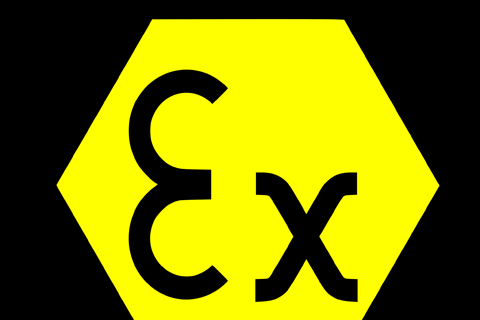
ATEX approval
For FERMASIL silicone foam seals, an ATEX approval for component applications in explosive environments e. g. mining, oil drilling is possible.
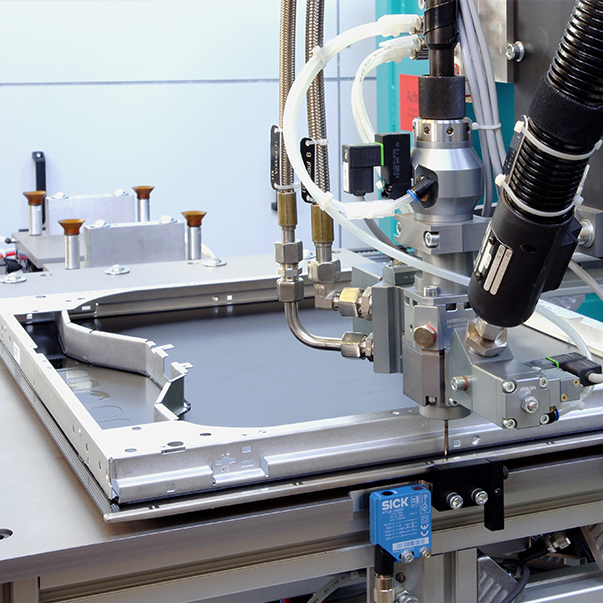
FERMASIL – the technology
FERMASIL sealing foams can be efficiently and accurately applied onto parts from the most varied industry sectors using the FIPFG (Formed-In-Place Foam Gasket) technology with the SONDERHOFF mixing and dosing machines. Depending on the viscosity, they are either freely applied as liquid material into a groove or highly viscous material on a 2D or 3D part surface.
Only the exact interaction of possible setting parameters of the mixing and dosing machine and the selected FERMASIL material system enables a reliable sealing against moisture, dust and other environmental influences together with the overall construction of the industrial component.
FERMASIL – the reaction process
The chemical reaction of FERMASIL sealing foams is initiated by mixing the A- and B-components. The applied compound foams up to a uniform gasket under room temperature conditions.
FERMASIL – The foaming process | |
---|---|
Pot life: | The time span from the mixing of the A- and B-components to the beginning of the foaming time (approx. 5 – 60 sec.). It is also referred to a processability time or service life. |
Foaming-up time: | The time span in which the FERMASIL foam system expands to form a sealing body (after approx. 1 – 20 min.). |
Tack-free time: | The time from which the sealant surface of FERMASIL foam systems can be touched without causing damage (after approx 2 - 60 minutes) |
Assembly time: |
The chemical reaction has progressed so far that the FERMASIL foam systems can bear loads or the foamed components can be assembled (after approx. 30 minutes - 12 hours) |
THE FERMASIL RANGE SELECTION
The FERMASIL offers effective component protection for the most diverse requirements for sealing, gluing and potting. In the table you will find a selection of different silicone systems for various industries, from lighting to control cabinet and automotive construction, to electronics, packaging and white goods.
Designation | Application* | Viscosity mPas |
Hardness Shore |
Density g/cm3 |
Other properties | |
---|---|---|---|---|---|---|
1809-1 |
Automotive Distance sensors |
8,400 | 77 Shore 00 |
0.67 | Slightly foamed, liquid silicone system, particularly suitable for ultrasonic sensors, good ratio between resonance and absorption behavior | |
93-VP1 |
Automotive Drive belt cover |
145,000 | 64 Shore 00 | 0.35 | Highly viscous, stable, medium hardness, curing possible without heat treatment | |
2525-1 |
Automotive Underbody cover |
28,000 | 30 Shore 00 | 0.28 | Extremely soft, semi-thixotropic, good processability | |
3510-1-G |
Automotive Maintenance cover Ad-Blue |
45,000 | 45 Shore 00 | 0.23 | Soft, semi-thixotropic, good price-performance ratio | |
6080-1 |
Automotive Cover |
138,000 | 57 Shore 00 | 0.31 | Thixotropic, medium hardness, UL50e listed | |
91-VP2 |
Lighting Luminaires, E-boxes, packaging, switch cabinets |
21,000 | 57 Shore 00 |
0.30 | Liquid, good flow, curing possible without heat treatment, for lighting with ATEX approval | |
4570-1-DG |
Lighting Lighting with ATEX approval |
55,000 | 40 Shore 00 | 0.34 | Soft, semi-thixotropic, good price-performance ratio | |
4010-LV |
Electronics Potting of electronics, battery packs, sensors, PC boards |
5,700 | 37 Shore A | 0.97 | Very good dielectric properties, good flow rating, good low-temperature flexibility, good chemical resistance, transparent | |
5507-LV |
Packaging Food boxes, packaging covers in contact with food |
14,000 | 44 Shore A | 1.16 | Fast curing, good mechanical properties, good chemical resistance | |
47-14 | Enclosures | 92,000 | 60 Shore 00 |
0.33 | Thixotropic, stable, standard material with medium hardness, UL50e listed | |
93-1-VP3-GREY |
Enclosures Switch cabinets with ATEX approval |
110,000 | 62 Shore 00 |
0.36 | UL50e listed, thixotropic, stable, curing possible without heat treatment | |
3590-2-DG | Enclosures | 80,000 | 35 Shore 00 | 0.30 | Soft, thixotropic, fast curing | |
38C3-1 | Enclosures | 165,000 | 40 Shore 00 | 0.34 | Soft, thixotropic, stable |
Good reasons for using FERMASIL
- ... can be used at a constant temperature up to +180 °C, for special types up to +250 °C
and temporary up to +350 °C. - … keeps the greatest possible flexibility even down to -60 °C.
- … is closed-cell and therefore nearly do not absorb water.
- … is highly resistant to many chemicals.
- … is hydrolysis stable and therefore suitable for use in tropical or damp environments.
- … is tack-free in 2– 60 minutes, depending on the thermal conditions. A furnace can significantly
shorten the reaction time, but it is not always necessary. - … is processed using a mixing and dosing machine for two components and can be adapted flexibly
and quickly to other parts for sealing application at any time. - … develops a cross-linked structure which is extremely resistant to environmental effects
such as humidity, dust and temperature. - … has an exceptional long-term behavior and almost 100% resetting ability, even after many years
of continual use. - … is in some cases also suitable for direct contact with food.