Tailored sealing solutions for maximum product safety
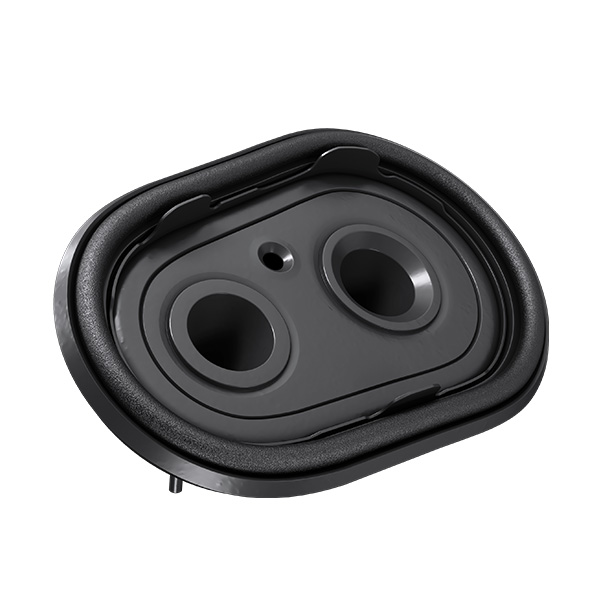
We develop custom sealing foams for sealing cable grommets according to your requirements
Loose parts in the wiring of vehicles are not permitted, as they can cause operational malfunctions and damage. This is because the cables in cars are exposed to a wide range of influences such as vibration and also environmental influences. Therefore, they must be particularly solid and well protected.
The wiring from the engine compartment through the firewall of the engine compartment partition into the interior, e. g. to the control devices, is made via plastic cable grommets with vulcanized cable passages.
The contour of the underside of the cable grommet is sealed to the installation side of the engine partition with sealing foam. Possible component tolerances are fully compensated.
Sealing of cable grommets
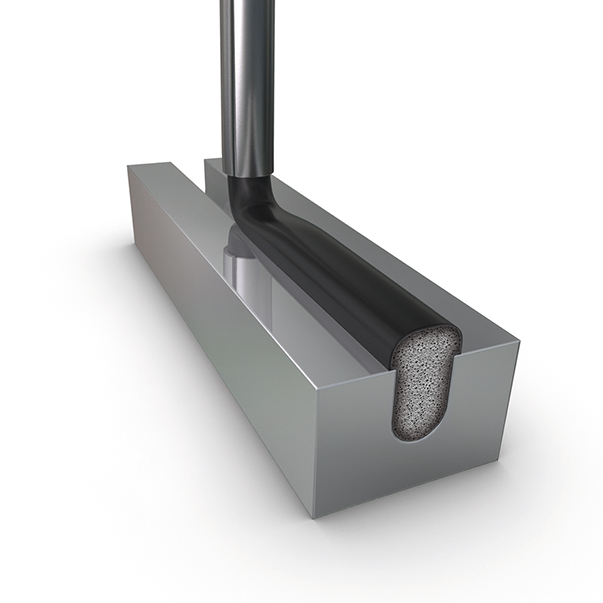
The reference material presented for this purpose, FERMAPOR K31-A-9308-5-VP5 and B-81 (B component), is a room-temperature curing 2-component polyurethane foam. It is temperature-resistant from -40 to +80 °C and is applied to the component contour very precisely, reliably and efficiently using the FIPFG (Formed-In-Place-Foam-Gasket) technology of our fully automated dosing machines.
In addition, we can also customize the polyurethane sealing foams to meet your specific component requirements. Influencing factors include pot life until start of foaming, curing time, and the viscosity, hardness and adhesion properties. Thanks to a mixed-cell foam structure, the closing forces when installing the foam gasket are low.
Due to its very good shape recovery characteristics, the mixed-cell polyurethane foam gasket can be compressed easily even after many years (tested according to DIN EN ISO 1856). It is possible to remove and reinstall the sealed component several times while maintaining the sealing effect of the foam gasket.
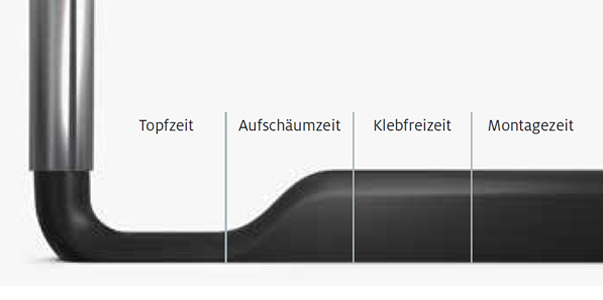
The different reaction phases of the sealing foam in the chronological sequence
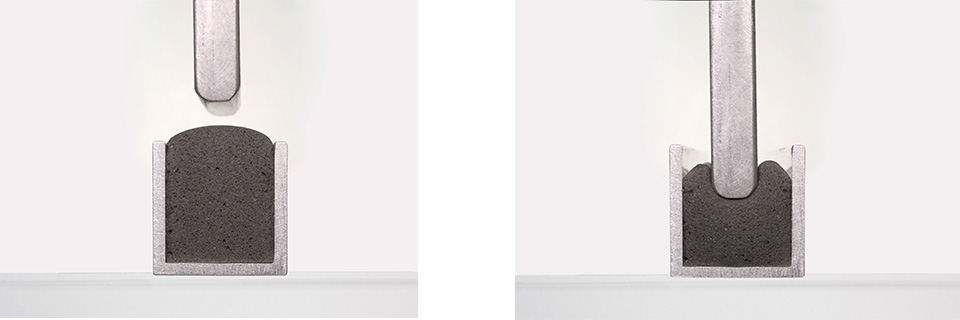
Cross-section polyurethane foam bead ind groove unpressed and approx. 50 % compressed
Reference material
FERMAPOR K31-A-9308-5-VP5 | ||
FERMAPOR K31-B-81 | ||
Mixing ratio | 4 : 1 | |
Pot life time | 24 sec. | |
Tack-free time | 3.5 min. | |
Viscosity of the A component | 130,000 mPas | |
Density of foam | 0.20 g/cm³ | |
Hardness (Shore 00) | 45 | |
Temperature resistance | from -40 to + 80 °C | |
Pretreatment | if necessary plasma for e.g. PP and PE |
In addition to the reference products, we develop material systems according to your individual requirements. Influencing factors include pot life until start of foaming, curing time, and the viscosity, hardness and adhesion properties.
DM 502 mixing and dosing system with 6-axis robot for seal foaming of cable grommets
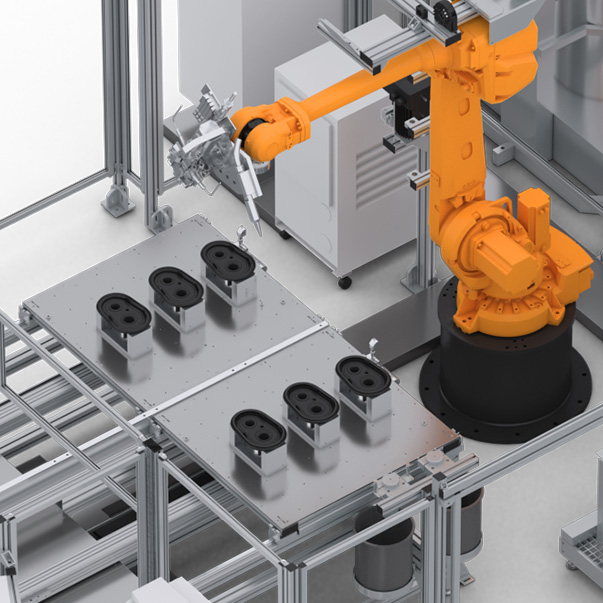
Flexible and fully automatic – fully in line with your requirements
The reference configuration shown here for seal foaming the contour on the underside of cable grommets consists of the DM 502 mixing and dosing system and a 6-axis robot that precisely guides the MK 825 PRO precision mixing head over the component for dosing of the sealing foam.
Parts are picked up and machined with the WT 1-LEVEL shuttle table in continuous shuttle mode of the two pick-up plates in one plane.
Parts are placed either by a machine operator, who can also check the parts for quality, or by a Pick & Place Robot. In the latter case, an optionally installed camera or sensor system could also perform quality control.
The FERMAPOR K31 polyurethane sealing foam is accurately and fully automatically applied to the groove contour on the underside of the cable grommet via the nozzle of the MK 825 PRO precision mixing head which is mounted on the robot arm.
After the dosing cycle, the coupling point of the foam gasket closes seamlessly and as a result is almost invisible.
When the cable grommet is installed, e. g. to the engine compartment wall, the uniform compression of the foam gasket achieves a high degree of tightness over the entire groove contour.
Even with short cycle times and high unit numbers, the material application process using the FIPFG method is carried out with high dosing precision and repeat accuracy. As a result, you achieve foam gaskets of uniformly high quality. This allows you to quickly process the sealed cable grommets right through to final assembly. This saves time and money.
In addition, our fail-safe mixing and dosing system can be operated easily and intuitively without the need for extensive training.
Thanks to the automatic logging of dosing program data, all process data can be traced and evaluated by the machine operator via the CONTROL 2 operating panel while production is running.
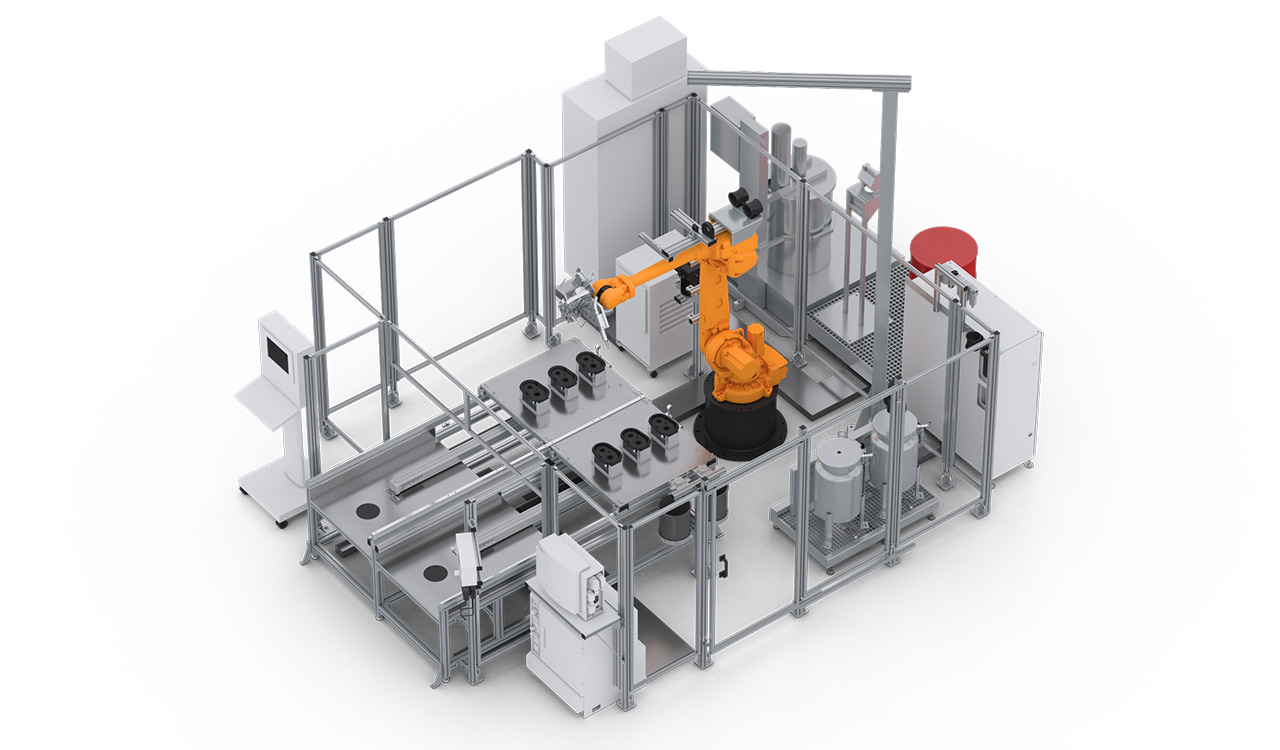
CONTROL 2
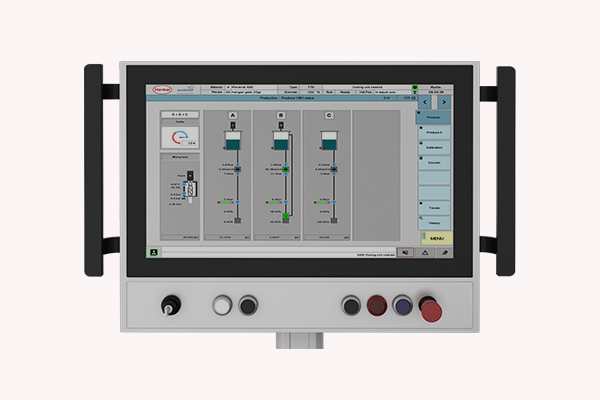
Optionally available: CONTROL touchscreen operating panel (21.5“) for operating the dosing system
More information to our operating panelsWT 1-LEVEL shuttle / sliding table
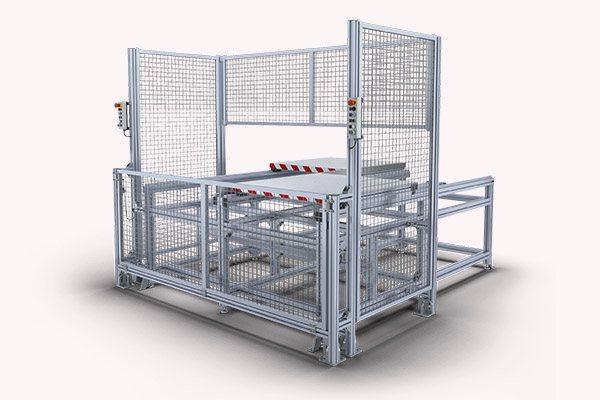
Two pick-up plates operating in pendulum mode in one plane
More information to our shuttle tablesMixing head 825 PRO
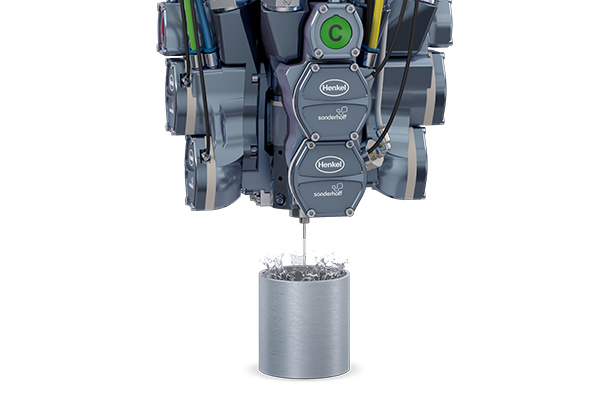
MK 800 PRO precision mixing head with high-pressure water rinsing or alternative component rinsing system
More information to our mixing headsControl cabinet
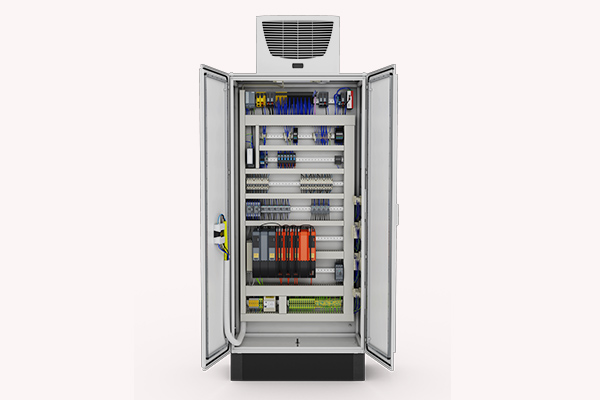
The control electronics, safety engineering and industrial PC are installed in the control cabinet.
More information to our control cabinetsDosing machine cabinet
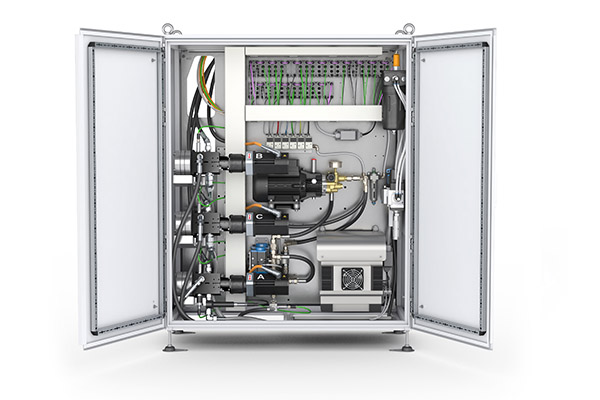
The dosing machine cabinet contains the components of the dosing periphery, e.g. the dosing pumps.
More information to our dosing machine cabinetsElevator
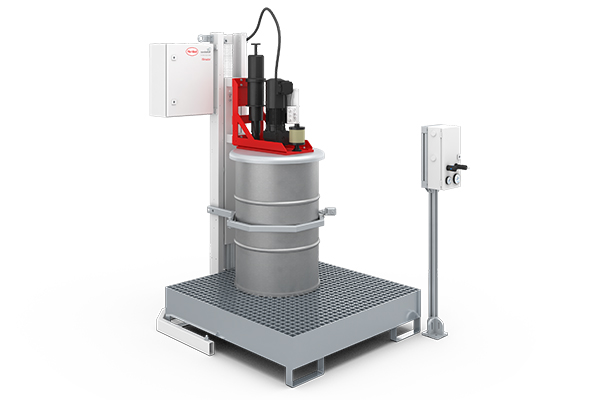
Optional: Automatic ELEVATOR drum refilling station for the A-component with pneumatic lift and agitator
More information to our refilling stationsSupply Tap
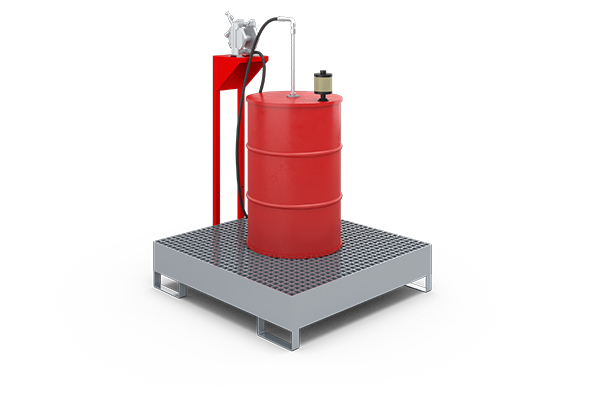
Optional: Automatic SUPPLY TAP drum refilling station for low-viscosity products, e.g. isocyanate (B-component)
More information to our refilling stationsMaterial pressure tanks
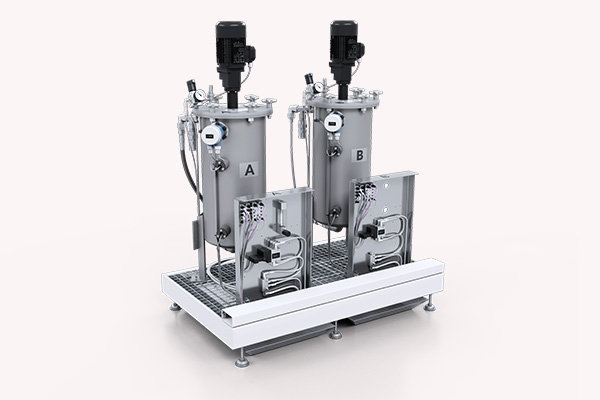
Material pressure tanks (24 l or 44 l, single-walled or double-walled) with minimum level sensors, on a grating platform with adjustable leveling feet and drip tray
More information to our material Pressure Tanks