Automated 2-component potting
The industry standard in many sectors
Through the automated application process electronics or electronic parts are potted or encapsulated using 2-component cast resins. The potting hardens at room temperature and supports the integrity of the final parts. Potting material is also used for circuit boards which are covered with a potting layer, or component surfaces covered with a transparent protective coating.
The main advantage is that potting can be achieved through fully or partly automated processing and dispensing. The part application is carried out in an economical and reliable fashion with a fully automatic SONDERHOFF mixing and dosing machine.
The chemical basis of the 2-component cast resin systems used for this are polyurethane (PUR), polyurethane-epoxy mixes or silicone. The chemical and mechanical properties of these plastics can be varied over a broad spectrum. The potting is therefore suited to a wide range of applications.
Once the potting has cured, it protects electrical and electronic parts from damp, dust, dirt, temperature, shock and accidental contact.
Furthermore, potting can be used for copy protection, and it improves electrical insulation and can be formulated flame-retardant.
The chemistry makes it possible
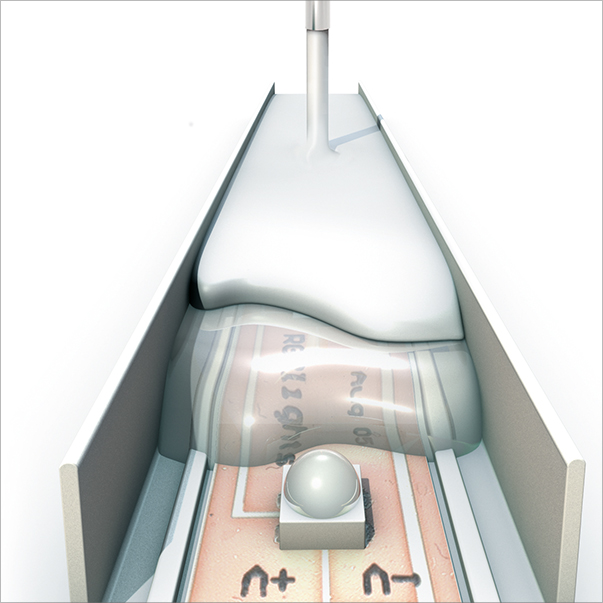
The resin component is made up of polyols. Together with fillers and diverse additives they make up the A-component of a potting recipe. Varying molecular weights (chain lengths) in the resin polyols determine how hard or soft the potting is going to be.
The hardener component (B-component) of a PUR cast resin product consists of 4,4-methylene diphenyl diisocyanate (MDI) with varying NCO content.
The hardening of the PUR resin components to become a potting is based on a chemical reaction between both components, A and B, the alcohol group of the resin with the isocyanate group of the hardener.
Cast resin is an artificial resin in liquid form that is shaped into a final product. The cast resins harden through a chemical cross-linking reaction at room temperature and become an irreversible element of the finished artefact. In contrast, thermoplastic potting compounds melt under heat application and stiffen after cooling
Polyurethane casting resins are 2-component potting systems and consist of a resin and a hardener component. A mixing and dosing system mixes the two components in a pre-determined ratio. After the application on the part, a cross-linked upper surface forms in a few minutes. The complete curing time varies depending on the potting recipe and material properties.

Silicone potting for demanding applications
Silicone-based casting resins are 2-component potting systems and also consist of a resin and a hardener component. They, like polyurethane potting, are processed with a DM 502 mixing and dosing system from Henkel and are mixed together at a pre-determined ratio.
The mechanical properties of silicones, e. g. very high tear-resistance and flexural strength, are superior to those of polyurethane. Silicone potting is additionally very weather and ageing-resistant and survives temperatures up to +180 °C, for a short time even up to +350 °C.
Transparent silicone potting is UV-stable and has great chemical resistance. Thanks to excellent dielectrical properties, silicone potting is often used to protect electrical and electronic components, battery packs, sensors and circuit boards. Silicone potting can be given flame protection up to UL-94 V-0. As part of the completed construction of the part, they can reach protection classes to IP 69K and NEMA 4 to 6p.
The potting process
In the potting process, in contrast to foam sealing, air nucleation is left out, as potting is about the production of a compact elastomer without foam structure. The air present in the potting compound (A-component) is completely evacuated by thin film degasification in the material pressure tank of the potting dispenser system.
The two components, potting polyol and hardener, recirculate in separate pipelines from the material pressure tank of each component to the mixing head for dispensing on the part and back into the pressure tank. Gear pumps ensure a constant flow rate. Line valves open the flow of material to the mixing head and interrupt it after a time specified in the dispensing programme. In the mixing chamber of the mixing head an agitator mixes the two components at a pre-determined ratio. With electronically regulated rotational speed, the dynamic, homogeneous mixing of the components can be exactly controlled.
Only then does the dispensing and automatic material application begin. After a curing of a few minutes, a bubble-free potting is formed.
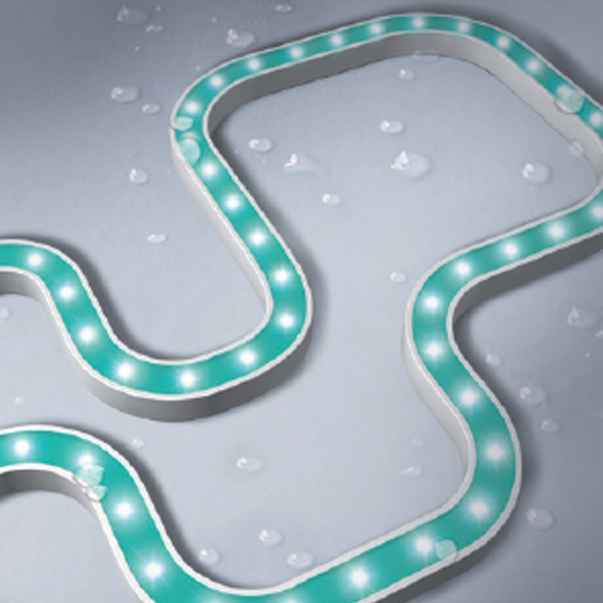
Automatic potting with the 2-component technology
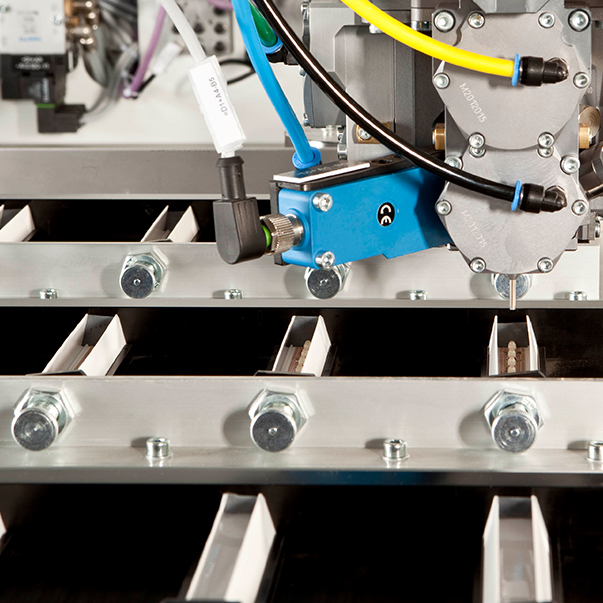
The mixing and dosing systems of the DM 50x series achieve extremely reliable material processing to create hard to gel-like potting with 2-component technology. They process medium to large batches very efficiently and economically in serial productions.
Employing 2-component technology, standard within the industry, the mixing head of the dosing system applies the potting compound in the exact quantity required for the part. This high volume accuracy facilitates the reproduction of identical potting volume to fill cavities of equal size.
The varying viscosity of the potting products ensures uniform potting distribution even in the most convoluted cavities of complex components. Bubble-free potting is essential for all-over adhesion to the part surface without any disturbance through air inclusions.
Dynamic mixing, as opposed to static mixing, has the advantage of making the mixing duration and homogenising intensity of the potting components adjustable at any time. Specially developed agitator designs allow gentle mixing after a few turns.
In contrast to volumetric dispensing, which relies on the determination of a constant output volume, SONDERHOFF potting systems are dosing gravimetrically. The potting is dosed by weight, weighing the exact quantity to be dispensed. By weighing and comparing the dispensed quantity with the set value in the machine programme, deviations are adjusted and the applied quantity kept constant.
A vital reason for the employment of 2-component potting is the ease of automation of the material application on to the industrial parts.

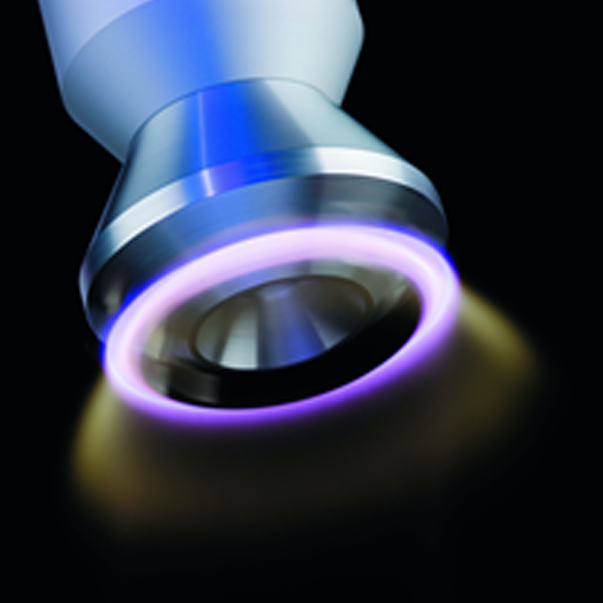
Atmospheric plasma treatment
Successful potting is dependent not only on the potting material and potting system, but also on the upper surface of the part being potted. For example, a dividing layer of fats or dust prevents ideal adhesion between potting material and the upper surface of plastic parts.
Via a plasma nozzle on the mixing head, atmospheric plasma treatment can take place on the part surface directly prior to the potting application. The part is purged of minuscule accretions of organic material down to the narrowest crevice. At the same time, the surface tension is increased, so that the potting can flow into every cavity of the part surface. Through strong chemical bonds an ideal adhesion between potting mass and surface is achieved.
Numerous potting uses
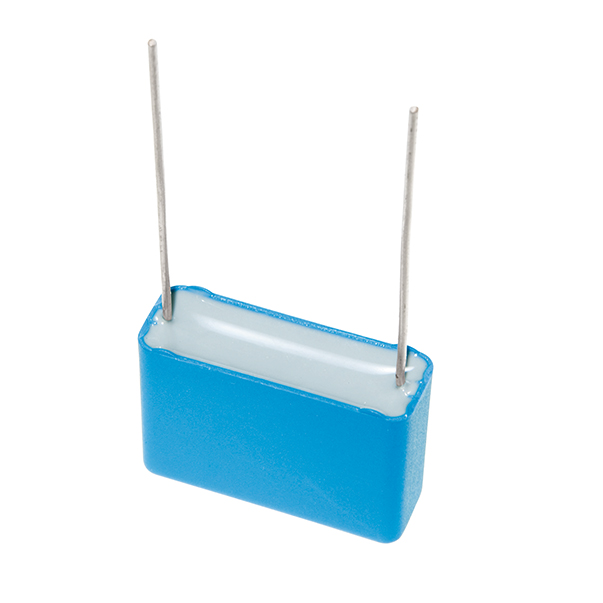
Even in complex, hard-to-access part geometries, electronics must be protected. As the miniaturisation of products continues, often the tiniest output volumes are required – so-called micro-potting. The mixing and dosing machines dispense the tiniest quantities, down to approx. 0.05 g/s With dosing nozzles of varying length and very fine interior diameters, the mixing head applies minuscule volumes very precisely in often very out-of-the-way part geometries.
The polyurethane-based FERMADUR and silicone-based FERMASIL potting products, with material properties such as hardness, tensile strength and temperature resistance, are flexible in application. They are adjustable to the most varied conditions and requirements of the part to be potted.
There are many reasons why 2-component potting on polyurethane or silicone basis is used in many different branches of industry. For example, electronics and electrical parts are being built ever closer to the engine compartments of vehicles, placing higher demands for temperature resistance and head dissipation. Their employment ranges from automobiles and air-conditioners through electronics to lighting and solar power.
Another reason for potting use is the introduction of digitisation in many product ranges and areas of life. Fault-free and reliable operation of electronics are considered a given by the customer. This makes the protection of highly sensitive electronics necessary. Through potting with cast resins, the electronics are protected from the infiltration of damp, dust, foreign bodies, and water, ensuring a long functional life.
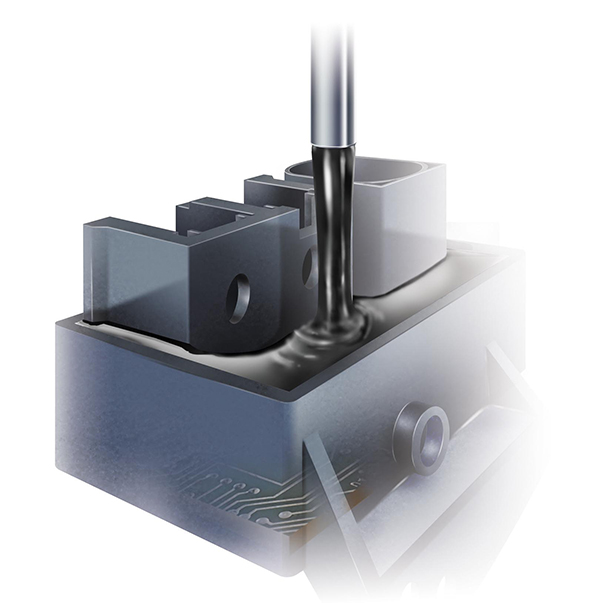
Typical potting applications
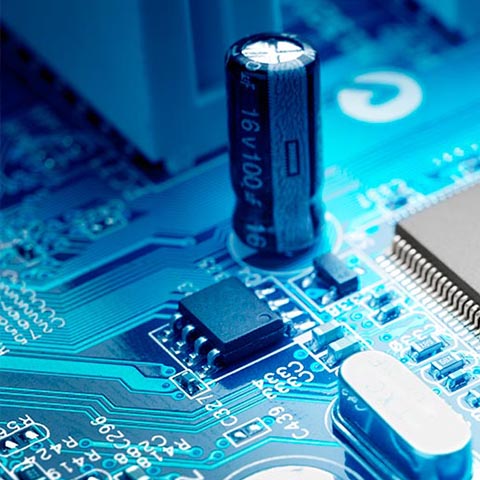
Electronics potting
Potting compounds based on polyurethane or silicone protect the sensitive electrical and electronic parts of devices from variable operating conditions, such as temperature fluctuations and overheating, dust, pressure, damp, shock and vibrations, and even mechanical strain caused by vandalism. Compliance with the listings for the safety level of electronics housings UL 50 / UL 50E must be achieved accordingly.
more...
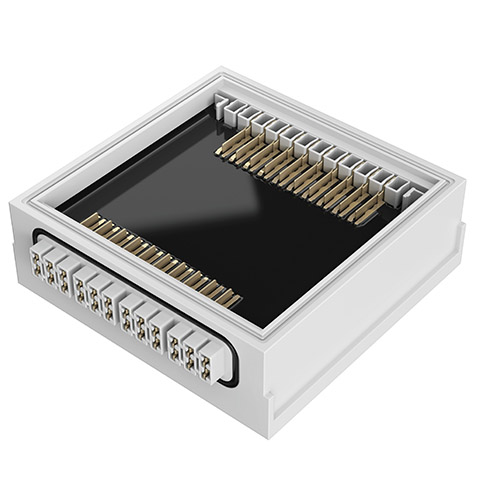
Plug and cable potting
The dimensionally stable cast resins fill, after curing, even the tiniest gaps in plug housings, connectors and power supply units. Before potting, all the air in the potting compound is eliminated by thin film degasification in the pressure tank. The potting can therefore flow freely into all cavities, without air pockets hindering its adhesion to the substrate. Polyurethane potting for plugs is characterised by low shrinkage and excellent high voltage resistance and insulation strength.
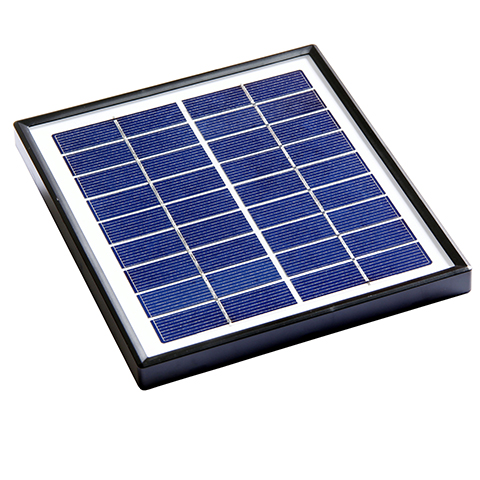
Photovoltaic potting
Our extremely weather-resistant, silicone-based potting protects the electrics of photovoltaic devices, so that they remain sealed after construction and stand up to diverse weather conditions and atmospheric fluctuations. It protects the flat wire connectors in the junction boxes of the photovoltaic system against the infiltration of damp, and thereby from corrosion. The total construction of the junction box with its completely potted interior electronics reaches penetration resistance aac. to IP 67.
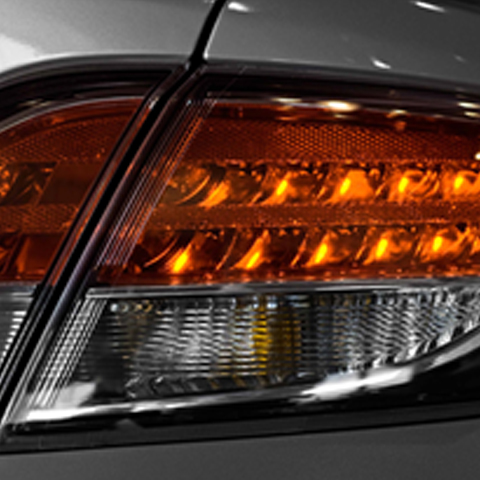
LED potting
For polyurethane and silicone-based LED potting, a bubble-free seal is essential for optimal potting transparency and the high transparency it provides. Air inclusions, rips or unevennesses lead to unstable potting. With thin film degasification in the material pressure tank of the dispensing system, these potting faults are avoided. The air introduced into the potting material during the production process is evacuated from the pressure tank by vacuum.
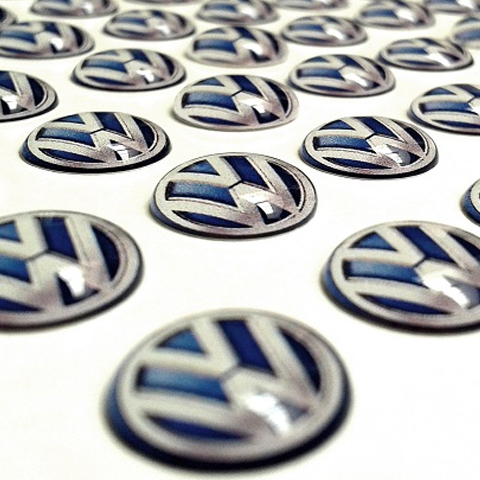
Doming
The production of a domed, decorative upper layer surface (doming) with highly transparent polyurethane potting, achieves a glass-like, three-dimensional appearance for logos and brand names. The potting surfaces are resistant to scratching and tears because the potting compounds return via a “self-healing effect” to their original state. Scratch-protected clear potting layers of polyurethane are used for sensitive surfaces, for example in the interior of cars, or for the preservation or fragile objects.
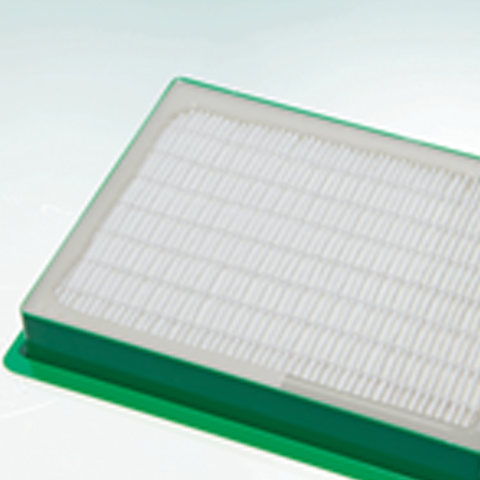
Filter potting
Filters play an important role in many sectors, whether in air-conditioning or industrial systems, cars or vacuum cleaners. The quality of filters, the bonding of filter packets and the leakage-free sealing of the filter frame is essential for clean air in many products and industries.
In the production of air, oil and fuel filters, the filter end-caps are joined with 2-component compact or foamed potting-adhesives, just as the filters are bonded and sealed to the filter frame.