Sealing of battery housings
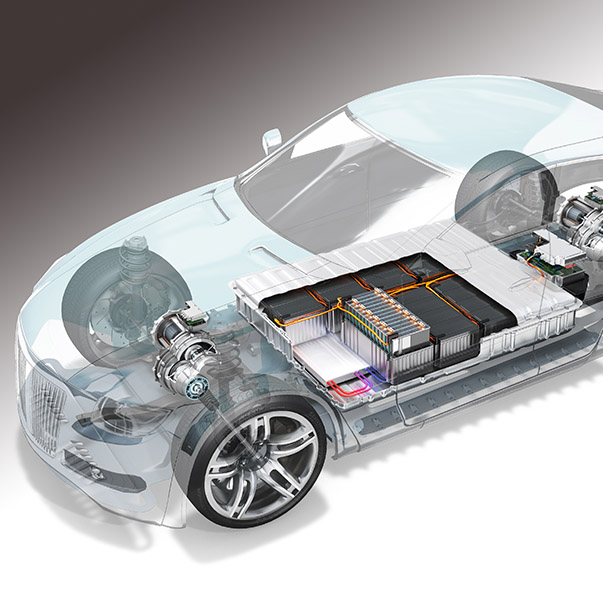
Electrification is key to mobility and to making people’s lives more sustainable. New and revolutionary technologies are driving the biggest transformation the automotive industry has seen in the last hundred years. The car of the future will be primarily electric, as well as connected to its environment and self-driving, in addition to other new types of drive.
The market for e-mobility will continue to grow unabated in the coming years. According to the German government’s National Development Plan, there will be around 2 to 3 million electric vehicles in Germany alone by 2025. To achieve the EU’s goal of climate neutrality by 2050, experts say at least 30 million zero- emission vehicles will need to be on EU roads by 2030, with three million public charging stations and up to 1,000 hydrogen refueling stations.
But what does this radical upheaval mean for you? Does an increased production volume also present you with new challenges time and again? Henkel will be pleased to develop individual automation solutions for you according to your requirements.
Are you also wondering how you can make your production processes more efficient? As process experts, we ensure perfect interaction between our dispensing technology and the sealing system selected from our product portfolio.
Sealing of the battery case of an electric car
In this video you will learn how the battery housing of an electric car is sealed fully automatically and seamlessly with the 2-component polyurethane foam FERMAPOR K31 and our dosing technology. Thanks to the very good resilience of the foam seal and thus a consistently high level of tightness, the housing can be opened and closed again at any time for maintenance purposes.
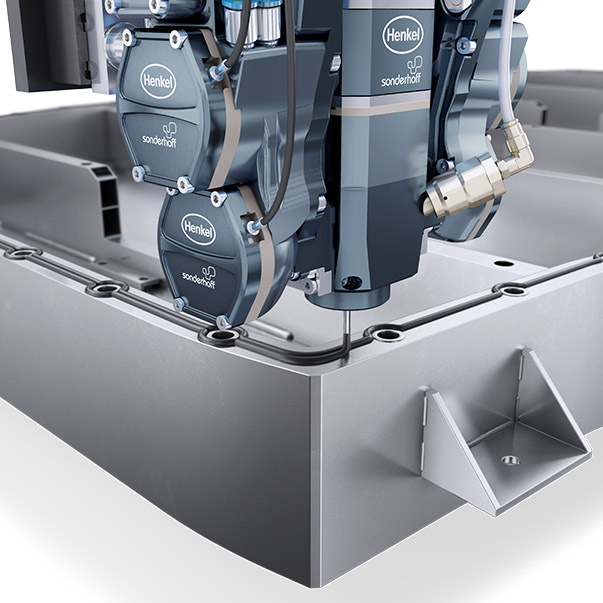
Using FIPFG technology (Formed-In-Place-Foam-Gasket), you benefit from the advantages of efficient, process-stable application processes. As a result, you ensure the high quality of your component sealing.
Special sealing foams from our product portfolio that can be further processed quickly also enable higher production output.
With its Sonderhoff brand, Henkel has many years of experience in sealing battery housings. As a manufacturer of sealing systems, mixing and dosing machines, and as a process expert for material application with FIPFG technology, we combine materials and engineering expertise.
In this way, we offer you individual sealing solutions that improve the longevity of batteries for e-cars.
Production Solutions for Sealing of EV Battery Housings
Mixing and dosing system with mixing head traversing unit for foam application and 6-axis robot for parts handling
Mixing and dosing system with 6-axis robot and conveyor belt for parts feeding
Customized material systems
for safely sealed battery housings
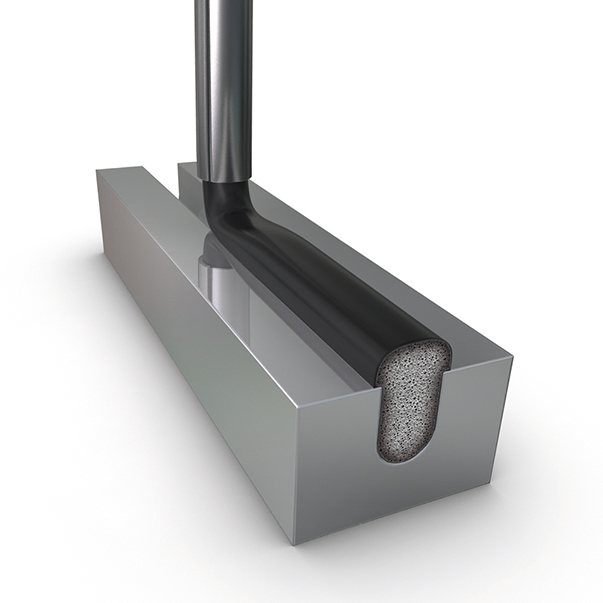
We develop individually for your specific requirements
EV (Electrical Vehicle) batteries for electrically powered vehicles are often exposed to extreme environmental conditions and the harshest vibrations. This requires a perfect seal of the battery case and electrical insulation for the optimal performance of these components.
The polyurethane sealing foams from the FERMAPOR K31 product family, which are used to seal the battery housings, protect the EV batteries from vibrations, thermal shock, moisture, dust and corrosion. This can extend the life of the EV batteries.
The fast-reacting 2-component polyurethane foam FERMAPOR K31 A-7060-5-B / K31-B-N developed for sealing battery housings is tack-free after just 3.5 minutes at room temperature. After the foam has reacted to a seamless foam gasket, the cover can be placed on the housing and screwed on after just 35 minutes.
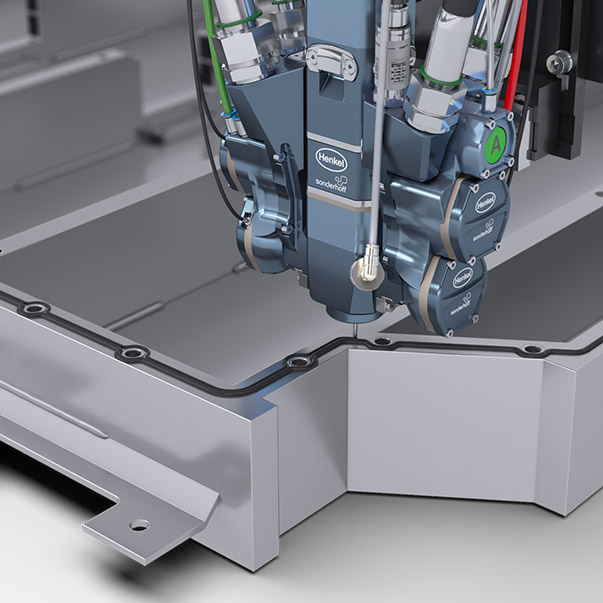
In addition to the polyurethane-based reference product, the 2-component silicone foam seal FERMASIL 40C2-1-UL-FR is a very good alternative. It has a significantly higher temperature resistance.
Our sealing foams can be applied to 2D or 3D components, with and without a groove, have low water absorption and generally good adhesion to steel, cast iron, aluminum and plastics (some with pretreatment).
In addition to the reference products, we develop material systems according to your individual requirements.
For example, we can provide you with special developments such as low-emission polyurethane foams with low VOC values (volatile organic compounds), sealing foams with flame retardancy in accordance with UL 94 HF-1 and potting products icompliant to UL 94 V-0 as well as foamed adhesive sealants that use up to 50% less material need for gluing.
Reference material
FERMAPOR K31-A-7060-5-B | FERMASIL A-40C2-1-UL-FR | |||
FERMAPOR K31-B-N | FERMASIL B-40C2-1-UL-FR | |||
Mixing ratio | 6.4 : 1. | 1 : 1 | ||
Pot life | 30 sec. | 50 sec. | ||
Tack-free time | 3.5 min. | 5.0 min. | ||
Viscosity A component | 63,000 mPas | 130,000 mPas | ||
Foam density | 0.23 g/cm³ | 0.26 g/cm³ | ||
Hardness (Shore 00) | 60 | 40 | ||
Temperature resistance | from -40 bis + 80 °C | from -60 bis +180 °C | ||
Flame resistance | ./. | UL 94 V-0 |
In addition to the reference products, we are developing material systems according to your individual requirements.
Frequent opening and closing of battery housing for maintenance purposes possible without deteriorating seal tightness
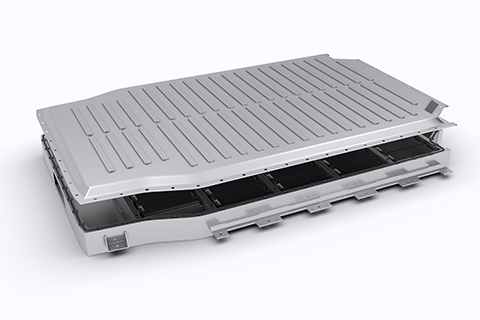
The very good resilience of the foam seal allows the housing to be opened and closed again for maintenance purposes without the tightness deteriorating.
After the screw connection, the housing is tight and the batteries are protected against splashing water and the effects of the weather.
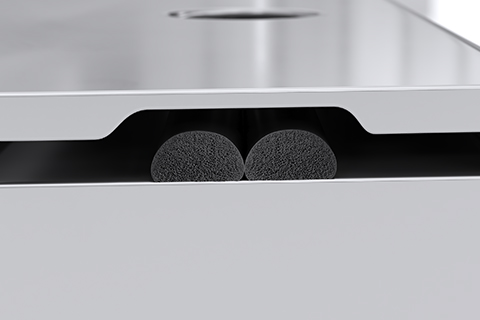
The unpressed foam seal before closing the housing.
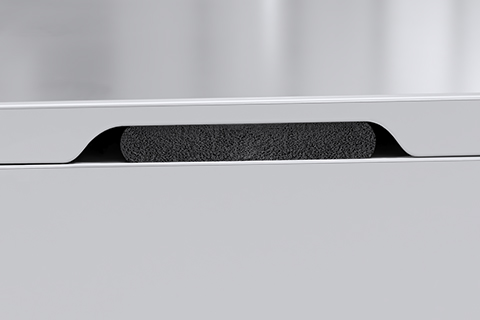
When the battery housing cover is screwed on, the elastic cell structure of the foam seal is compressed. This provides the sealing function of the housing seal - the battery housing is tight.
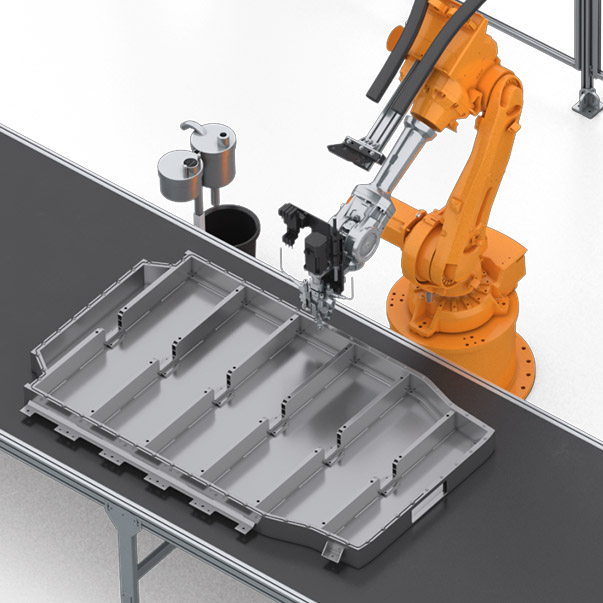
Flexible and fully automatic -
according to your requirements
An important success factor for high-quality sealing of battery housings is the efficiency of the overall solution and thus the optimal integration into your production. As process experts, we advise you competently and innovatively when it comes to automating your manufacturing processes.
For this purpose, we have numerous configuration and equipment options in our portfolio for semi or fully automatic productions, either with the 3-axis linear robots or through the use of 6-axis robots. We would be happy to work with you to develop your individual automation solution according to your requirements.
Mixing and dosing system with mixing head traversing unit for foam application as well as 6-axis robot for parts handling
In the reference configuration shown, the arm of the 6-axis robot grips the battery housing with cover and moves it below the mixing head of the DM 502 mixing and dosing machine for precise dosing. The foam application is precisely applicated and fully automatic with high repeat accuracy. This results in a foam seal that hardens at room temperature on the battery housing cover.
The battery housing with a foam-sealed cover contour is mounted under the underbody of the vehicle. This compresses the foam seal and thus achieves the sealing function.
Thanks to the automatic recording of the dispensing program data, all process data can be traced via the control panel while production is running and can also be evaluated later.
With all solutions, our main focus is on highly reliable system technology, a stable process, minimized maintenance times and consistently high dosing quality.
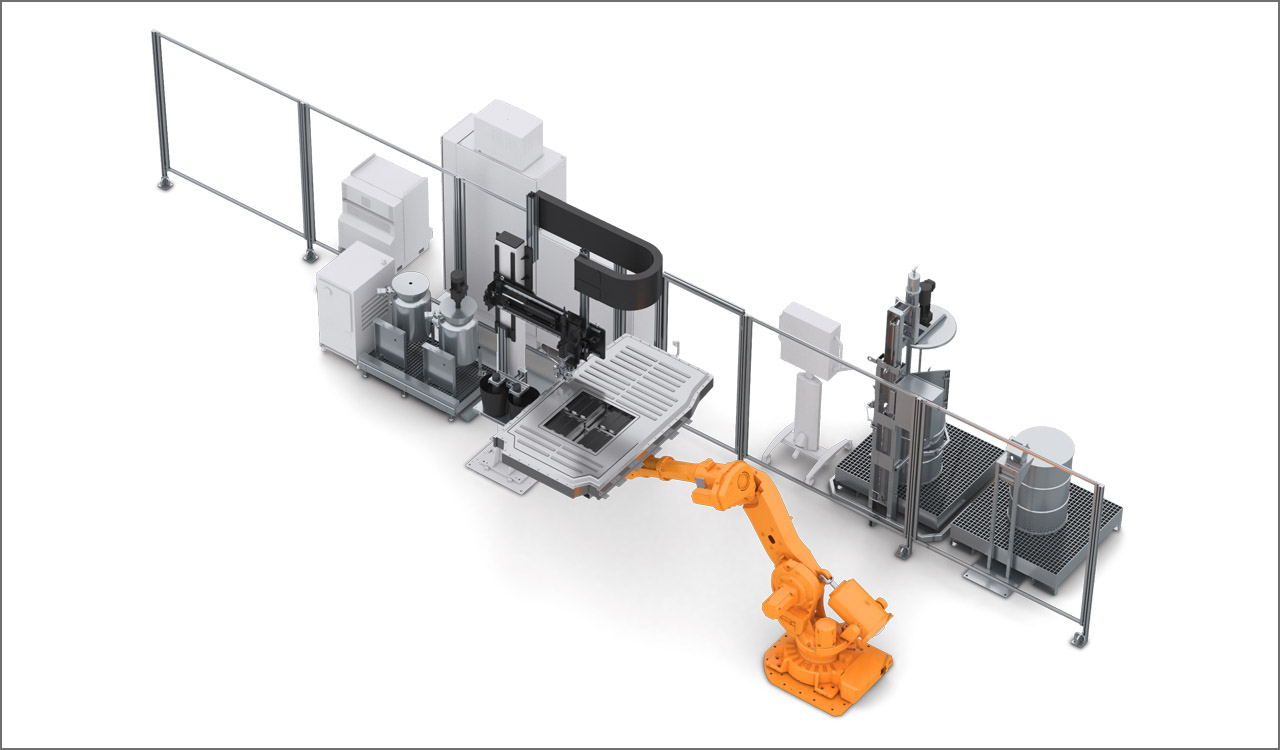
Control cabinet
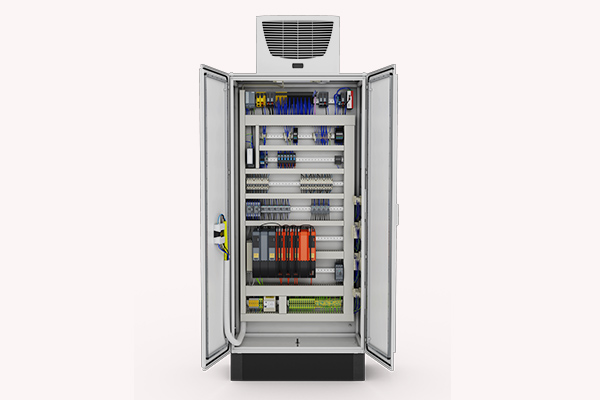
The control electronics, safety engineering and industrial PC are installed in the control cabinet.
More information to our control cabinetsCONTROL 2
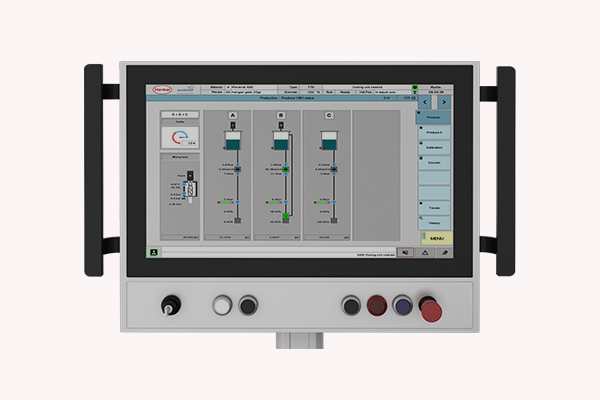
Optionally available: CONTROL touchscreen operating panel (21.5“) for operating the dosing system
More information to our operating panelsElevator
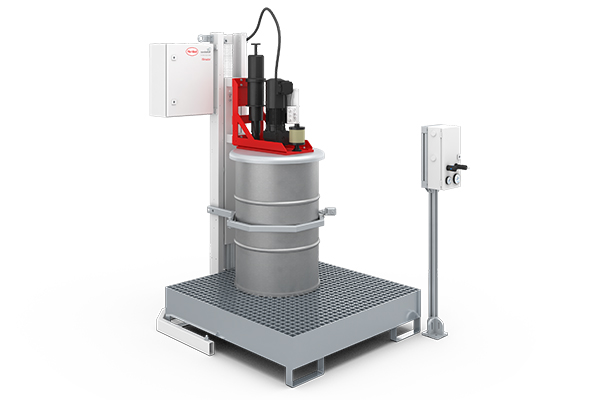
Optional: Automatic ELEVATOR drum refilling station for the A-component with pneumatic lift and agitator
More information to our refilling stationsSupply Tap
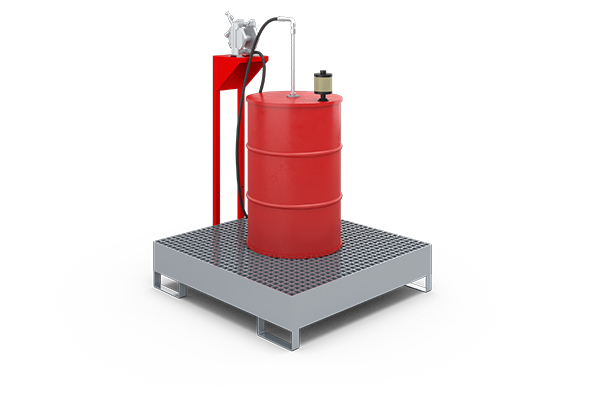
Optional: Automatic SUPPLY TAP drum refilling station for low-viscosity products, e.g. isocyanate (B-component)
More information to our refilling stationsMixing head 825 PRO
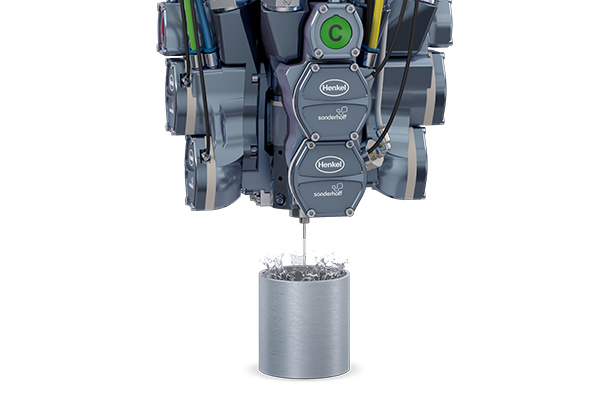
MK 800 PRO precision mixing head with high-pressure water rinsing or alternative component rinsing system
More information to our mixing heads2-axis mixing head traversing unit
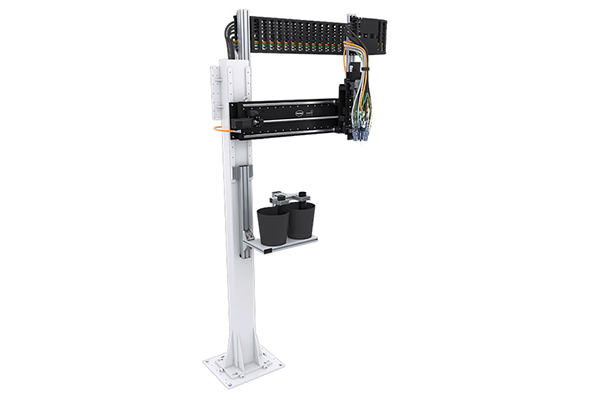
For the precise positioning of mixing heads to different positions for the application of polymeric reactive materials – optionally with electric or pneumatic drive.
More information to our traversing unitMaterial pressure tanks
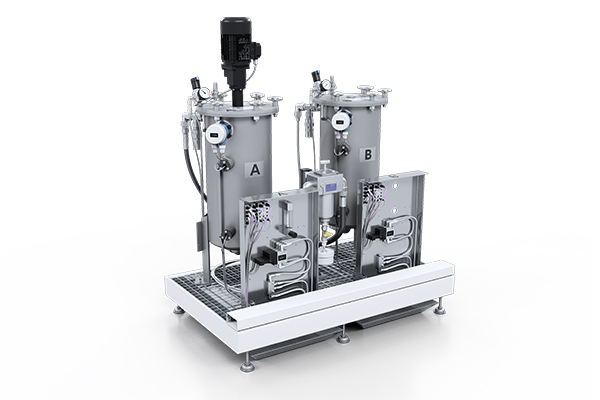
Material pressure tanks (24 l or 44 l, single-walled or double-walled) with minimum level sensors, on a grating platform with adjustable leveling feet and drip tray
More information to our material Pressure TanksDosing machine cabinet
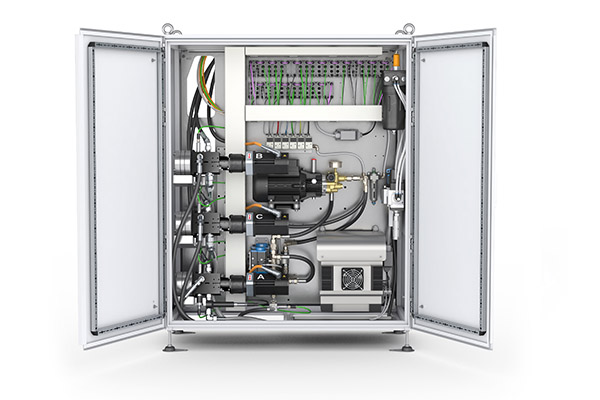
The dosing machine cabinet contains the components of the dosing periphery, e.g. the dosing pumps.
More information to our dosing machine cabinetsMixing and dosing system with 6-axis robot and conveyor belt for parts feed
In the reference configuration shown, the battery housing is fed to the DM 502 mixing and dosing system on a conveyor belt system at a defined cycle. For the dosing application of the polyurethane foam, the 6-axis robot guides the mixing head precisely over the contour of the housing. The sealing foam is applied precisely and fully automatically with high repeat accuracy.
This results in a foam seal that hardens at room temperature on the housing contour. When the battery housing cover is screwed on, the elastic cell structure of the foam seal is compressed. This provides the sealing function of the housing seal - the battery housing is tight and can be installed in the vehicle underbody.
Thanks to the automatic recording of the dispensing program data, all process data can be traced via the control panel while production is running and can also be evaluated later.
With all solutions, our main focus is on highly reliable system technology, a stable process, minimized maintenance times and consistently high dosing quality.
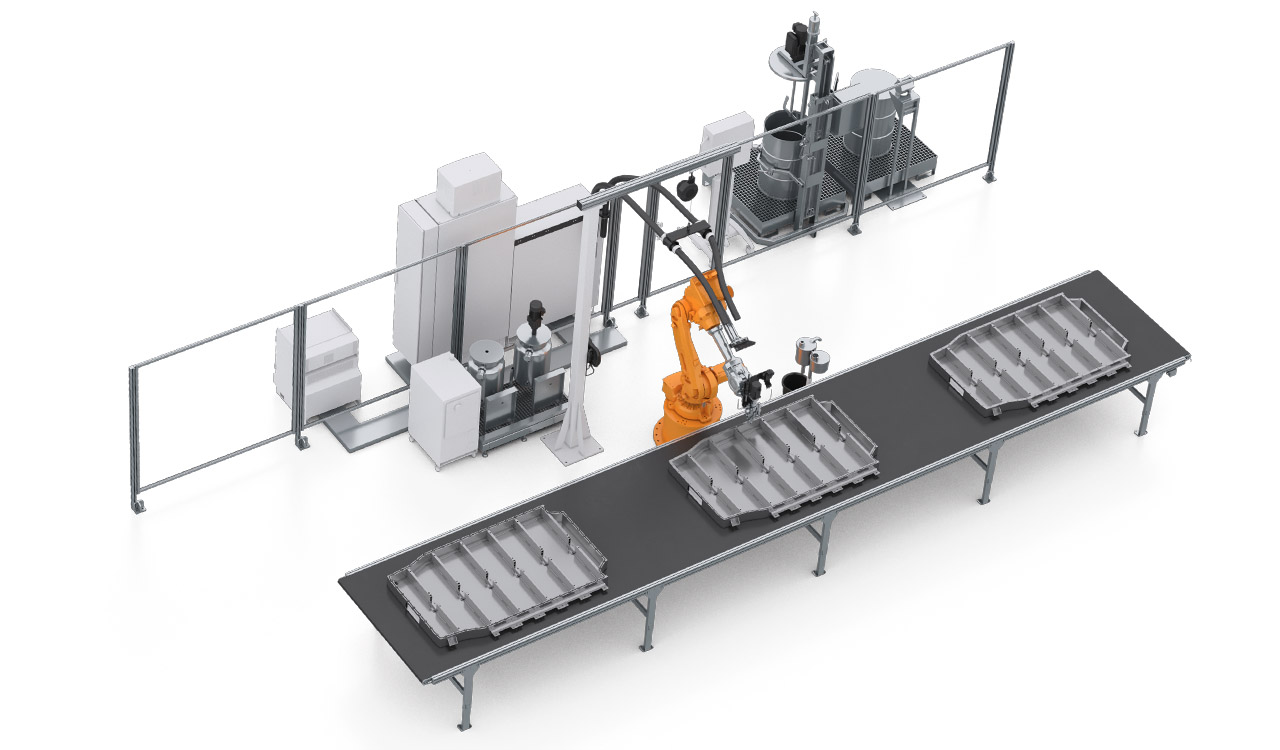
Control cabinet
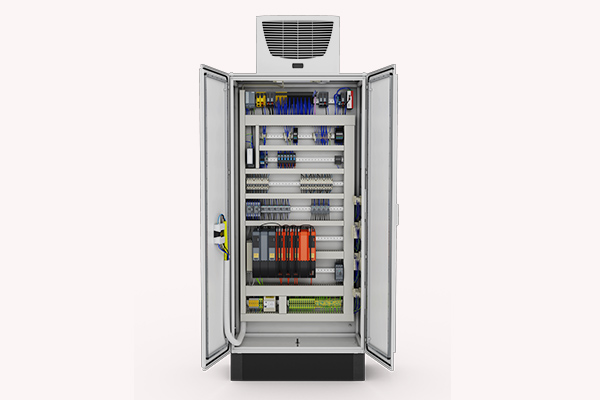
The control electronics, safety engineering and industrial PC are installed in the control cabinet.
More information to our control cabinetsDosing machine cabinet
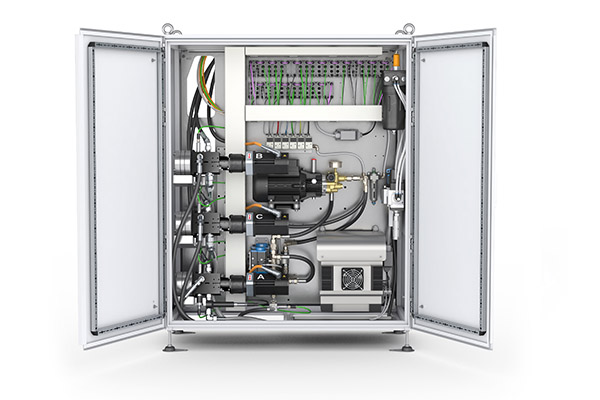
The dosing machine cabinet contains the components of the dosing periphery, e.g. the dosing pumps.
More information to our dosing machine cabinetsCONTROL 2
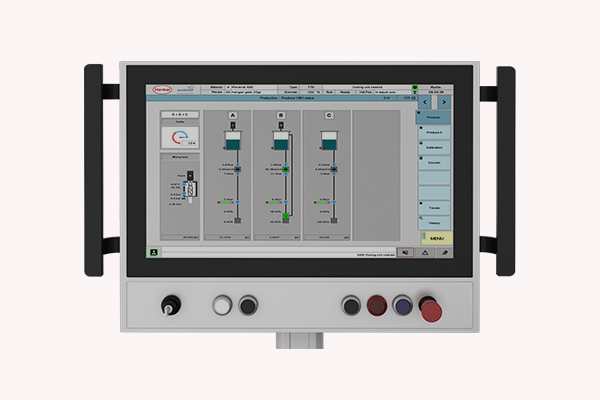
Optionally available: CONTROL touchscreen operating panel (21.5“) for operating the dosing system
More information to our operating panelsElevator
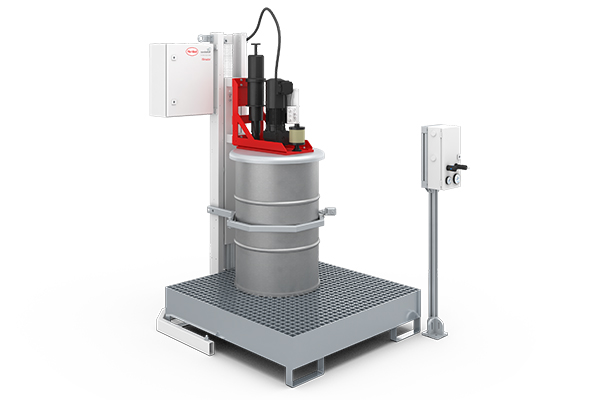
Optional: Automatic ELEVATOR drum refilling station for the A-component with pneumatic lift and agitator
More information to our refilling stationsSupply Tap
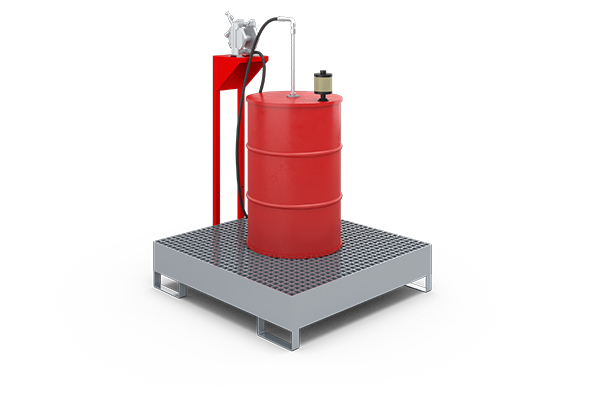
Optional: Automatic SUPPLY TAP drum refilling station for low-viscosity products, e.g. isocyanate (B-component)
More information to our refilling stationsMixing head 825 PRO
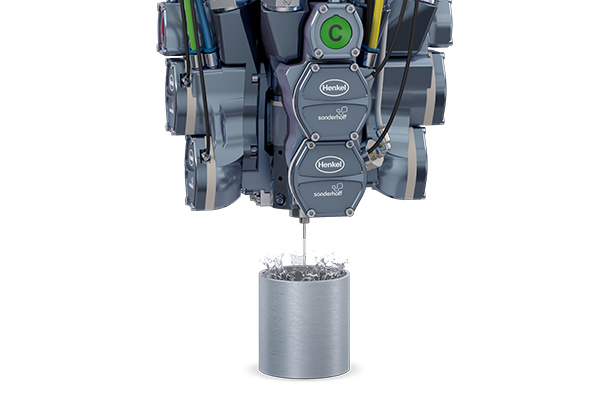
MK 800 PRO precision mixing head with high-pressure water rinsing or alternative component rinsing system
More information to our mixing headsMP 2 mobile panel
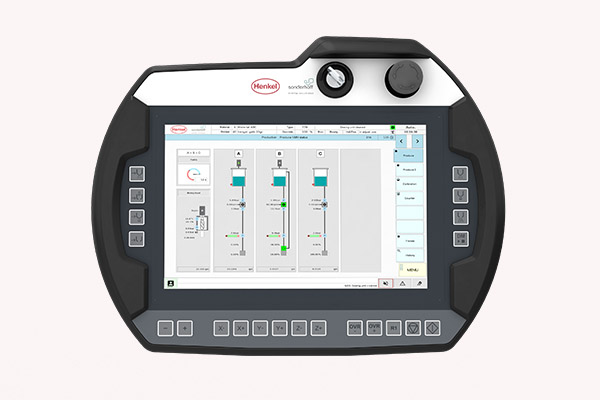
Optionally available: CONTROL touchscreen operating panel (21.5“) for operating the dosing system
More information to our operating panelsMaterial pressure tanks
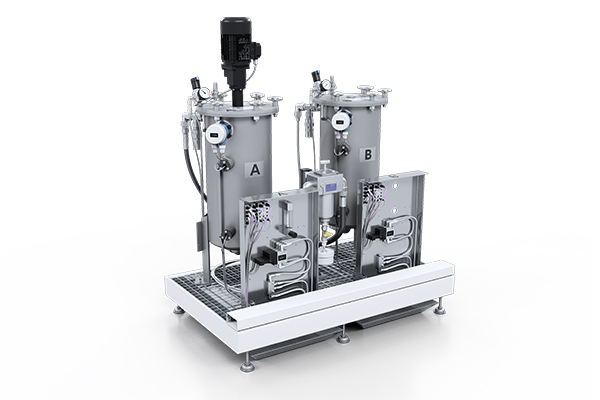
Material pressure tanks (24 l or 44 l, single-walled or double-walled) with minimum level sensors, on a grating platform with adjustable leveling feet and drip tray
More information to our material Pressure Tanks