Customized solutions for foam sealing
and bonding of V-filters
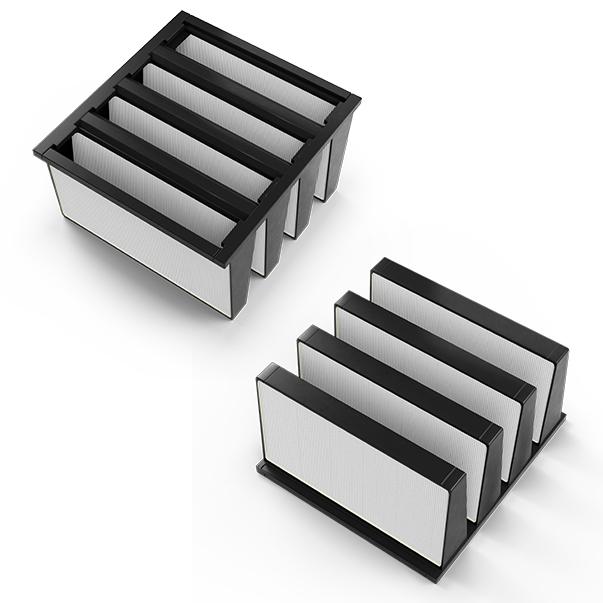
We develop individually for your specific requirements
In the pharmaceutical and microchip industries, manufacturing in clean rooms with clean air is a critical production factor - air quality is also vital in operating theaters and intensive care units.
The air filters required for clean rooms, from HEPA (High-Efficiency Particulate Air filter) to Super ULPA (Ultra-Low Penetration Air) filters, must not only be manufactured to the highest quality standards but also have a leakage-free fit when installed.
Compact V-shaped filters are used for ventilation systems or similar industrial applications. They are designed for high volume flows and long service lives.
As the filter surface is significantly increased thanks to very fine filter pleating, V-shaped filters are suitable for larger air flows and are also available in higher filter classes (M5 to F9 to EN 779).
Animation for sealing and bonding of
V-filters with the Sonderhoff DM 50x
Materials for bonding and foam gasketing of V-Filters
Our material systems ensure maximum stability and tightness and have high mechanical strength and very good adhesion properties.
The plastic filter frame is sealed with FERMAPOR K31 2-Component polyurethane sealing foam on the front and underside of the frame. After dispensing, the material foams up and forms a seamless soft foam seal at room temperature.
When the V-filter is installed in the ventilation system, the foam seal is compressed, and a leak-free filter seat is achieved.
The material and machine are precisely matched to each other, resulting in optimum interaction between the dispensing process and CNC-controlled motion sequences. This results in high-quality bonding of the filter and sealing of the filter frame as well as efficient production processes.
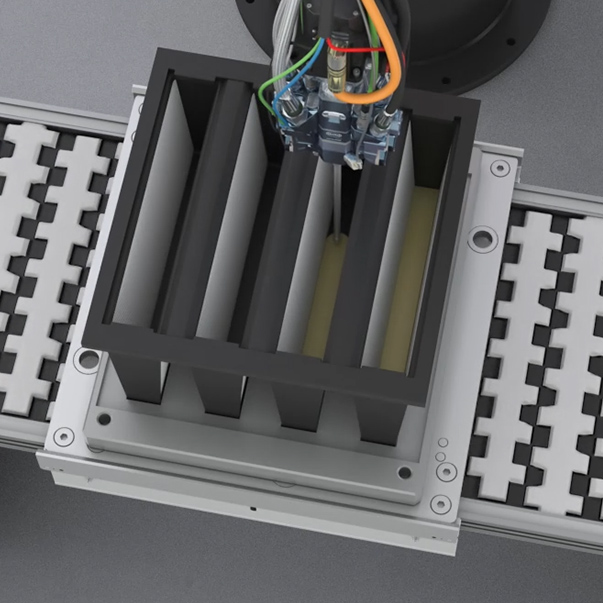
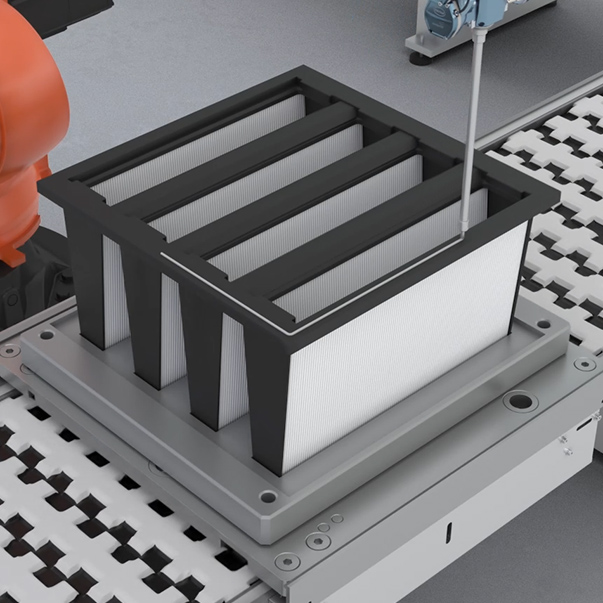
Reference sealing foam
FERMAPOR K31-A-3030-1-MX | FERMAPOR K31-A-6045-2-B-MX | ||
FERMAPOR K31-B-N | FERMAPOR K31-B-4 | ||
Mixing ratio | 6,0 : 1 | 4,0 : 1 | |
Pot life | 35 Sec. | 28 Sec. | |
Tack-free time | 5 Min. | 3 Min. | |
Viscosity A-comp. | 33,000 mPas | 56,000 mPas | |
Density Foam (DIN EN ISO 845) | 0.20 g/cm³ | 0.28 g/cm³ | |
Hardness (Shore 00) | 26 | 55 | |
Temperature resistance | from -40 to + 80 °C | from -40 to+ 80 °C | |
Field of application | V-filter with groove | V-filter without groove |
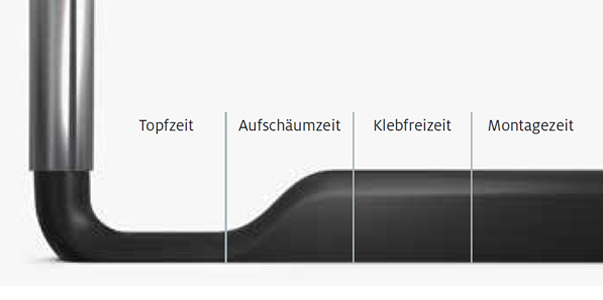
The various reaction phases of the sealing foam in chronological order
Reference adhesive material
FERMADUR A-196-7-VP9 | ||
FERMADUR B-RF | ||
Mixing ratio | 3.0 : 1 | |
Pot life | 160 Sec. | |
Tack-free time | 9 Min. | |
Viscosity A-Comp. | 5,200 mPas | |
Foam density (DIN EN ISO 845) | 1.27 g/cm³ | |
Hardness (Shore A) | 93 | |
Hardness (Shore D) | 30 | |
Temperature resistance | from -40 to + 80 °C |
In addition to the reference products, we develop material systems according to your individual requirements. The influencing factors include the pot life until the start of foam formation, the curing time as well as the viscosity, hardness and adhesion properties.
Production layout for sealing and bonding of V-filters
The system for sealing and bonding V-filters consists of two DM 502 dosing systems and two 6-axis robots, on each of which the Sonderhoff MK 800 PRO mixing head is mounted.
The material pressure tanks are supplied via automatic refill stations.
The control system and electronics are in two separate control cabinets. The operation of the system is done by the two mobile control panels CONTROL 2.
The V-filters on the workpiece carriers are fed and discharged via the circulating transfer belt system.
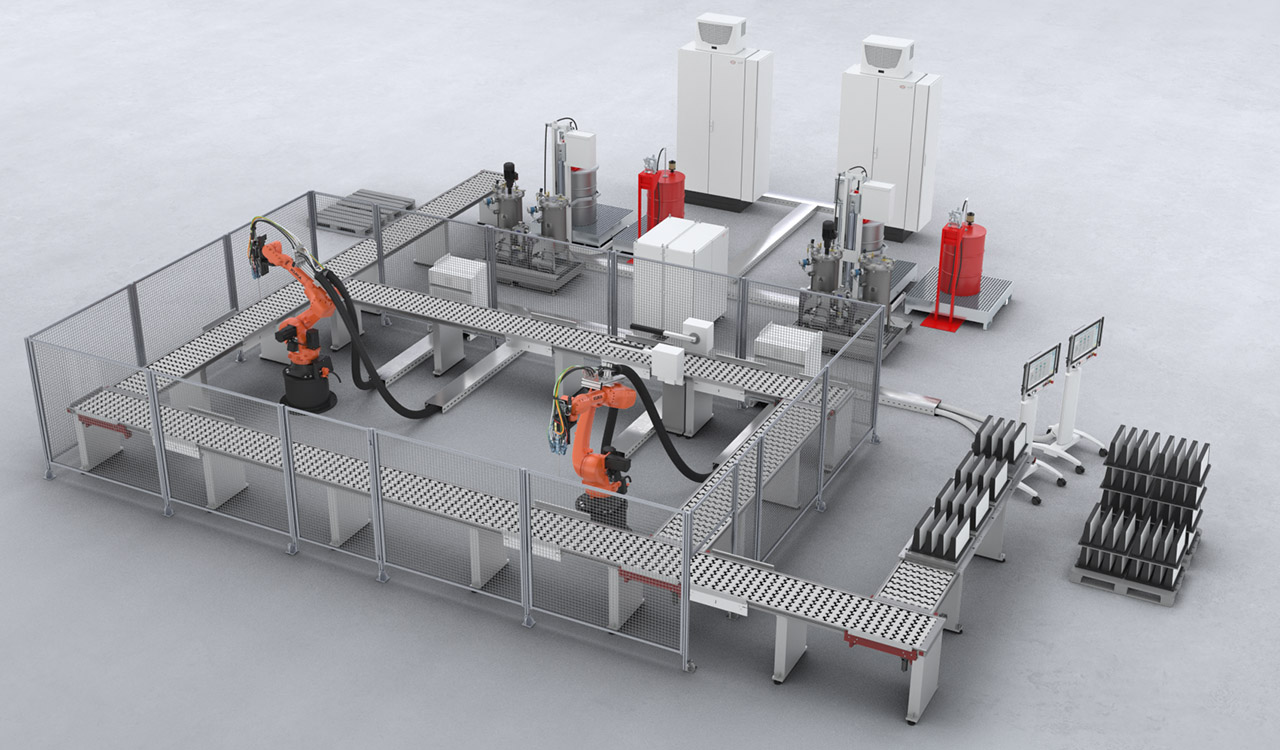
Touchscreen operating panel CONTROL 2
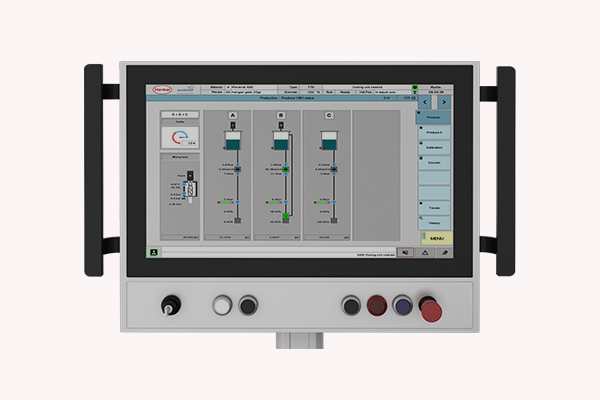
Optionally available: CONTROL touchscreen operating panel (21.5“) for operating the dosing system
More information to our operating panelsControl cabinet
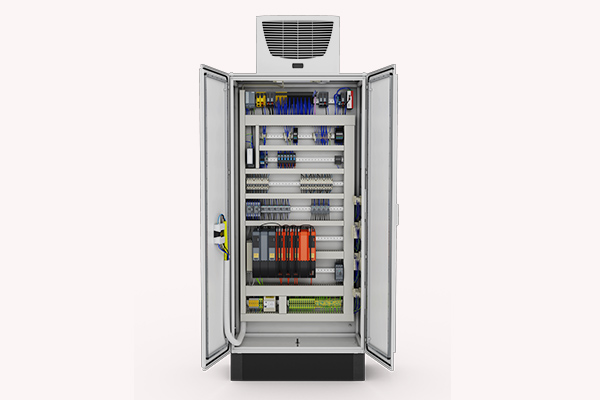
The control electronics, safety engineering and industrial PC are installed in the control cabinet.
More information to our control cabinetsControl cabinet
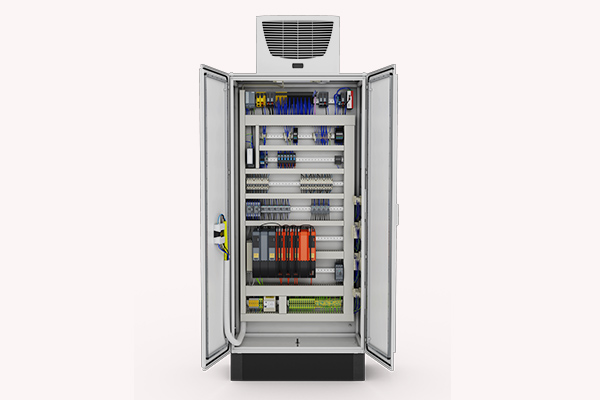
The control electronics, safety engineering and industrial PC are installed in the control cabinet.
More information to our control cabinetsDosing machine cabinet
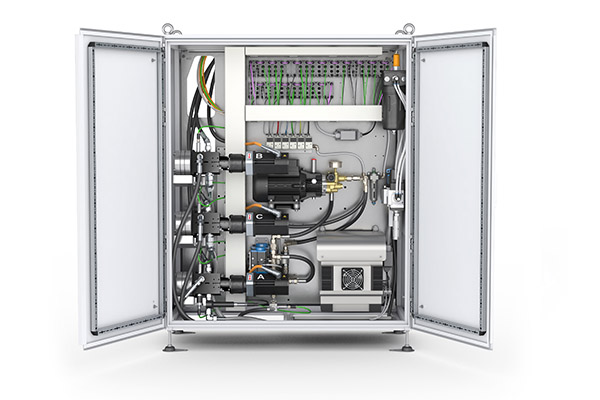
The dosing machine cabinet contains the components of the dosing periphery, e.g. the dosing pumps.
More information to our dosing machine cabinetsElevator
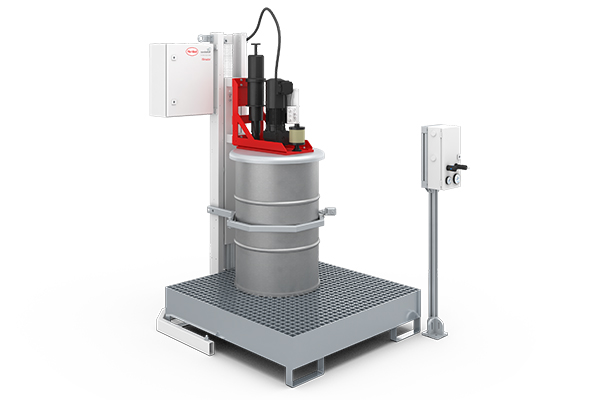
Optional: Automatic ELEVATOR drum refilling station for the A-component with pneumatic lift and agitator
More information to our refilling stationsElevator
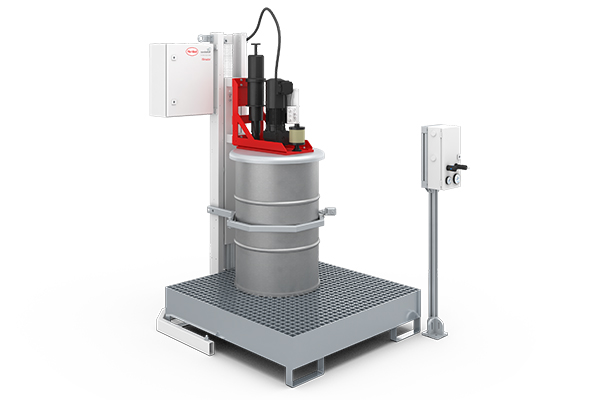
Optional: Automatic ELEVATOR drum refilling station for the A-component with pneumatic lift and agitator
More information to our refilling stationsSupply Tap
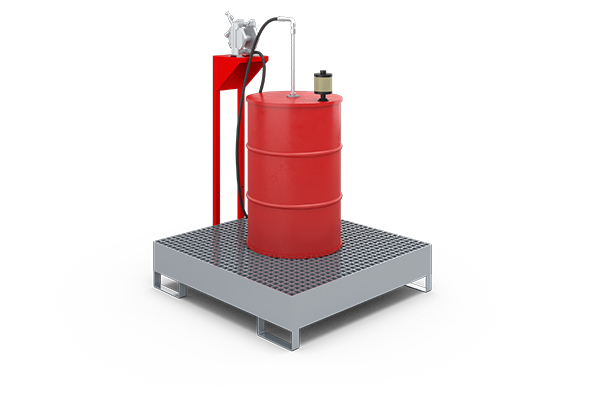
Optional: Automatic SUPPLY TAP drum refilling station for low-viscosity products, e.g. isocyanate (B-component)
More information to our refilling stationsSupply Tap
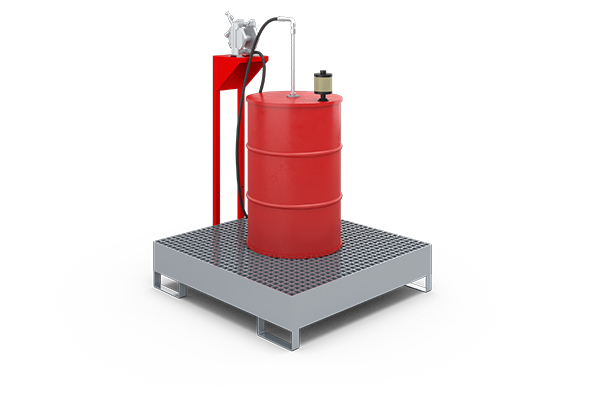
Optional: Automatic SUPPLY TAP drum refilling station for low-viscosity products, e.g. isocyanate (B-component)
More information to our refilling stationsMixing head MK 800 PRO
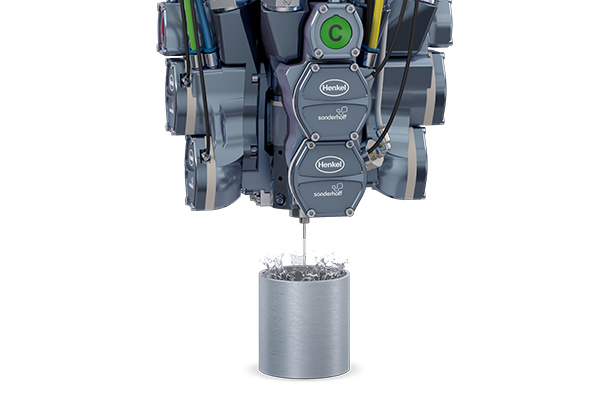
MK 800 PRO precision mixing head with high-pressure water rinsing or alternative component rinsing system
More information to our mixing headsMixing head MK 800 PRO
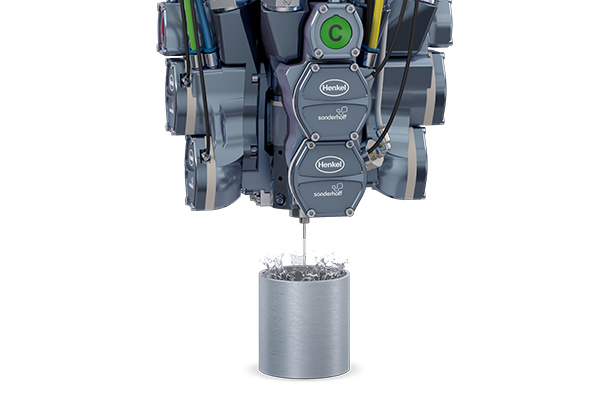
MK 800 PRO precision mixing head with high-pressure water rinsing or alternative component rinsing system
More information to our mixing headsThe process for sealing the filter frames and bonding the filter packs into the V-shaped frames begins with the manual insertion of the V-filter frames into the workpiece carriers on the transfer belt.
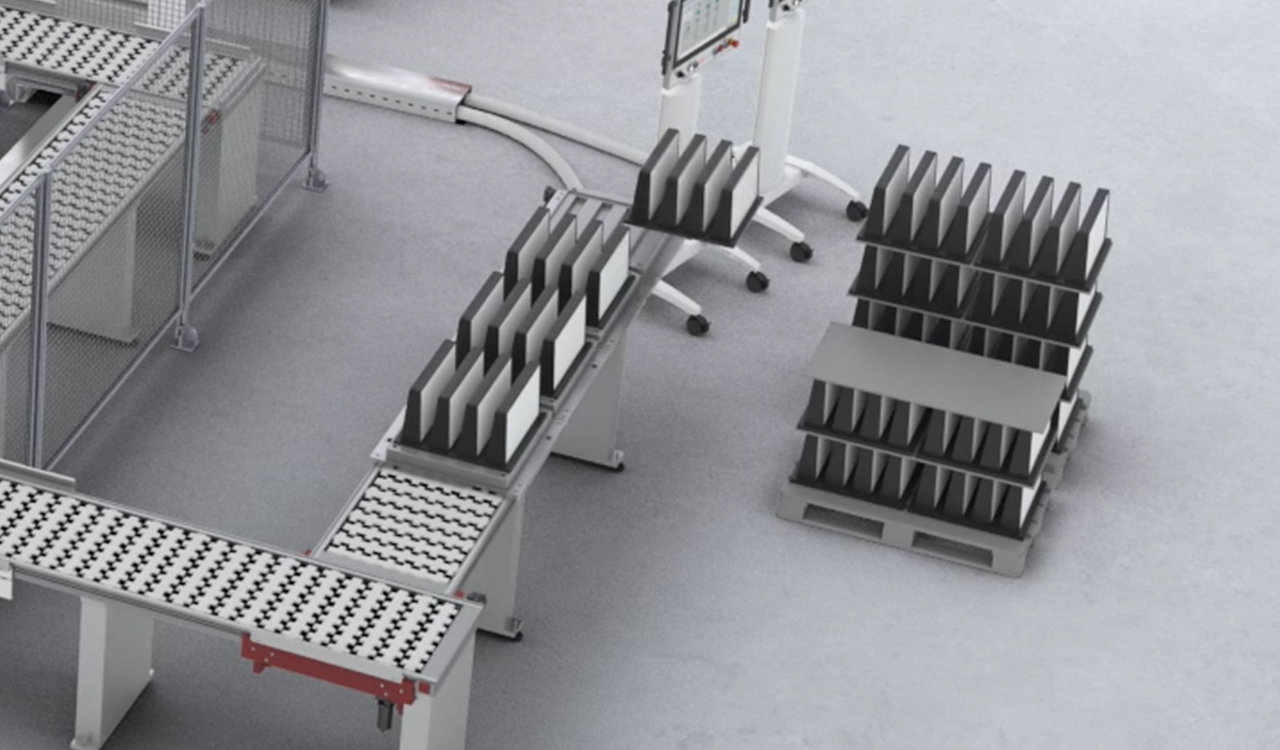
In the first step, the mixing head mounted on the 6-axis robot moves along the outside of the V-frame and dispenses the 2-component polyurethane sealing adhesive FERMADUR to bond the filters to the frame.
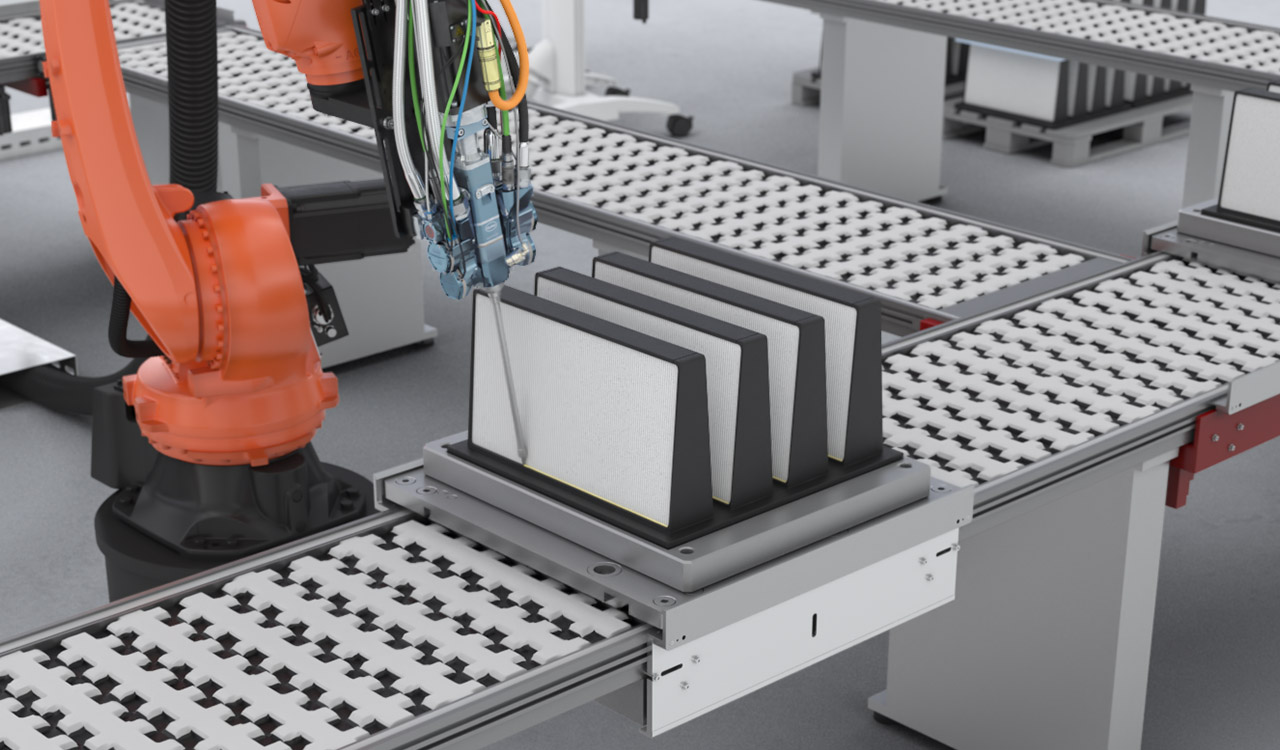
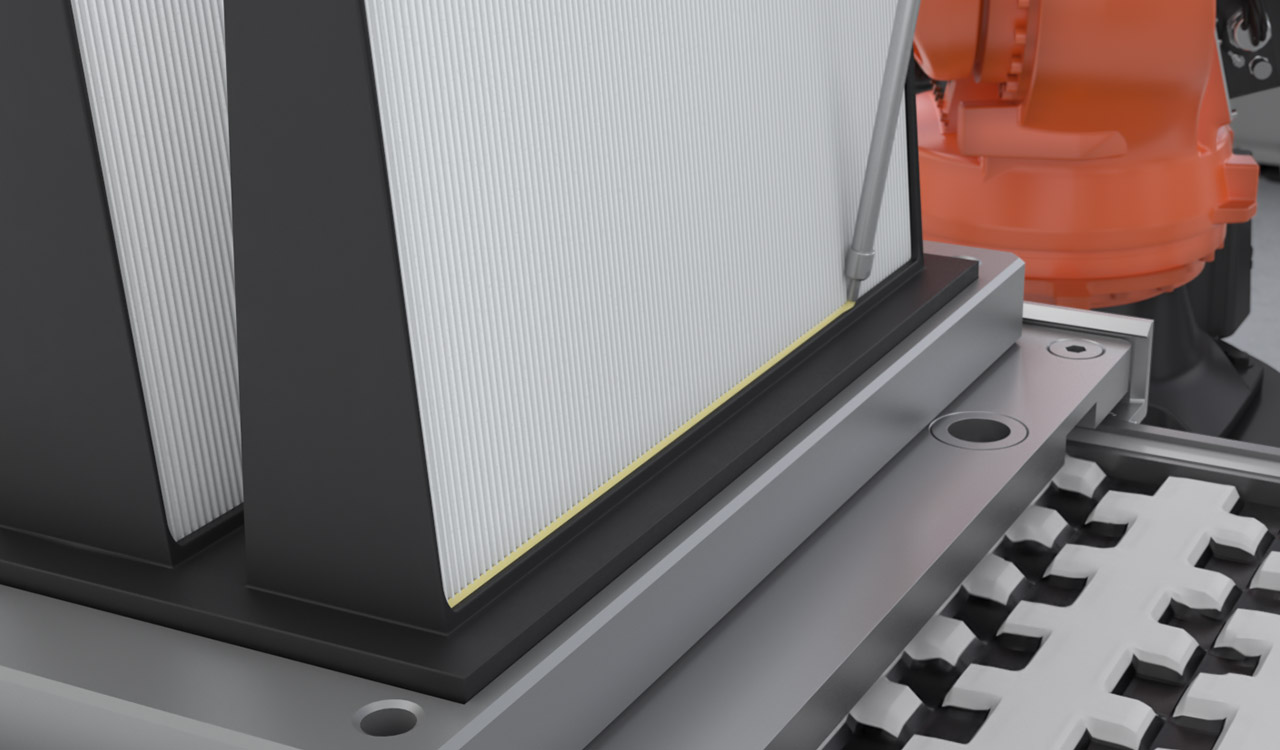
At the second station, the 2K polyurethane sealing foam FERMAPOR K31 is applied to the contour of the filter frame. To do this, the second 6-axis robot moves the mixing head around the V-frame with repeat accuracy.
The pasty sealing material foams up and forms a soft foam seal at room temperature, which is seamlessly sealed with an almost invisible joint.
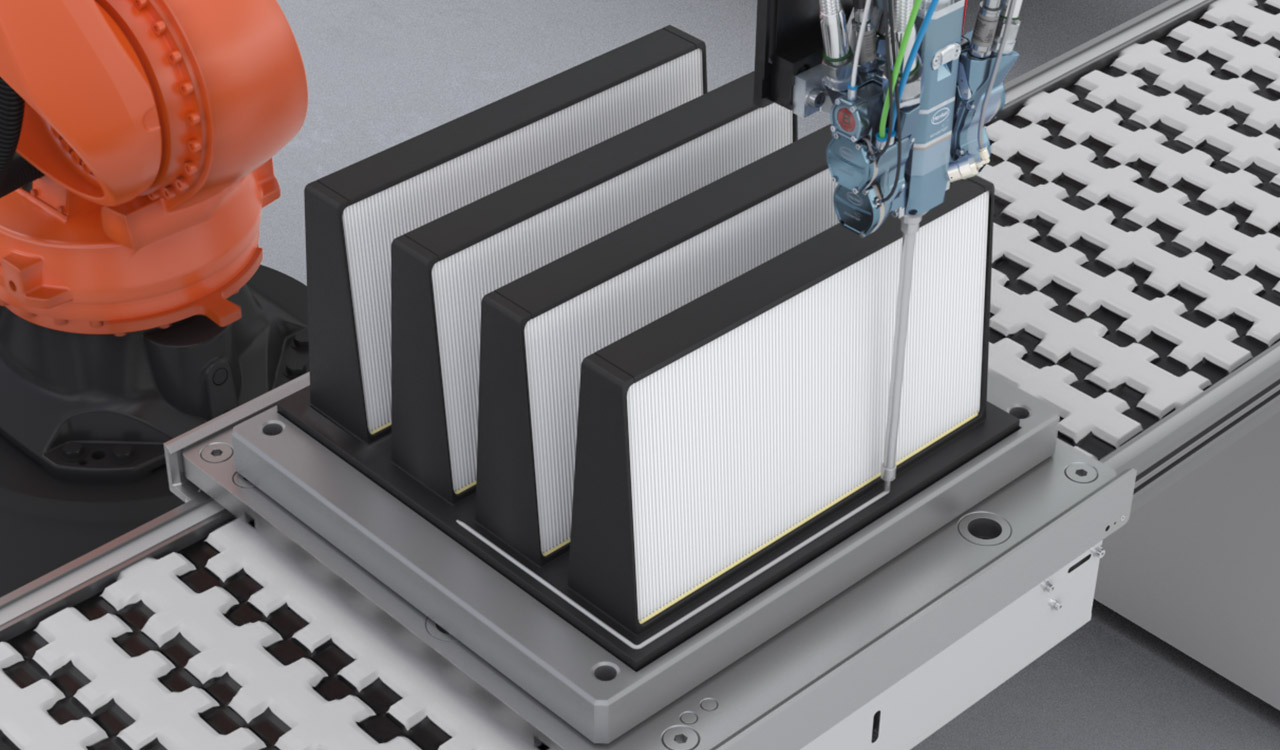
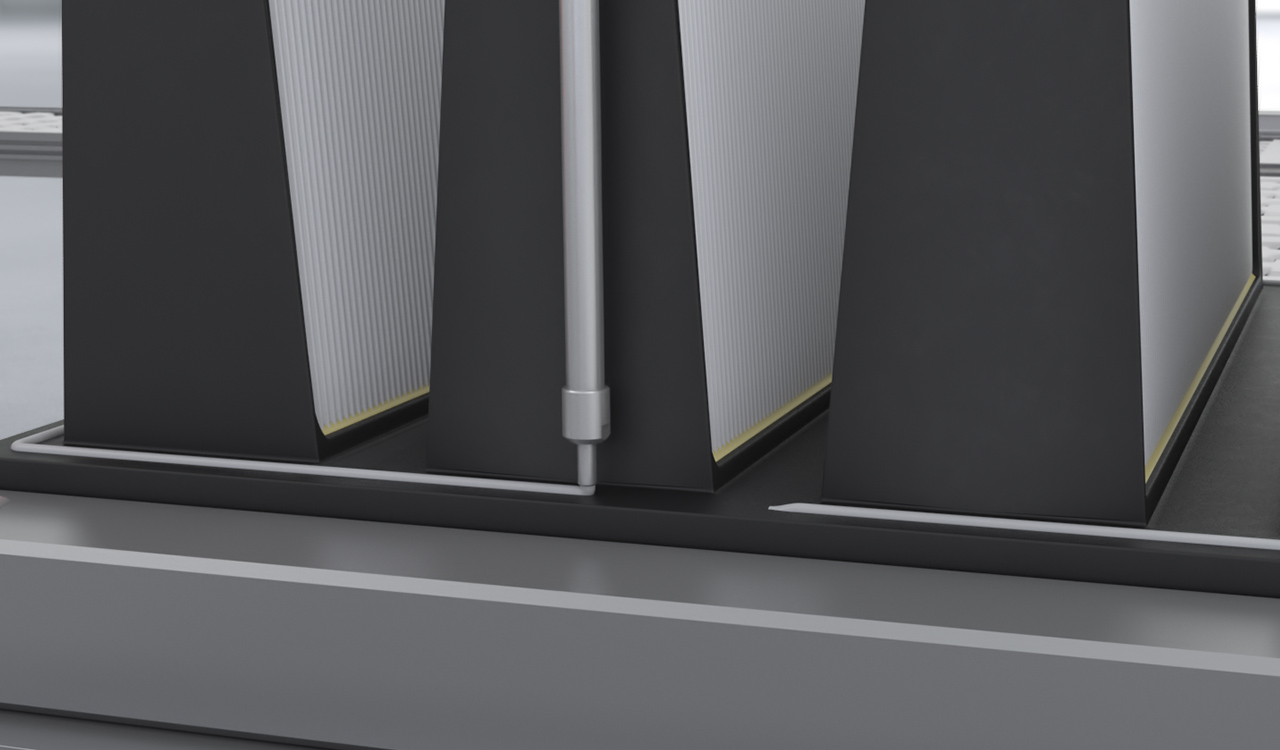
To bond and seal the undersides as well, the V-filter is turned 180° at the next station and conveyed to the next dosing station.
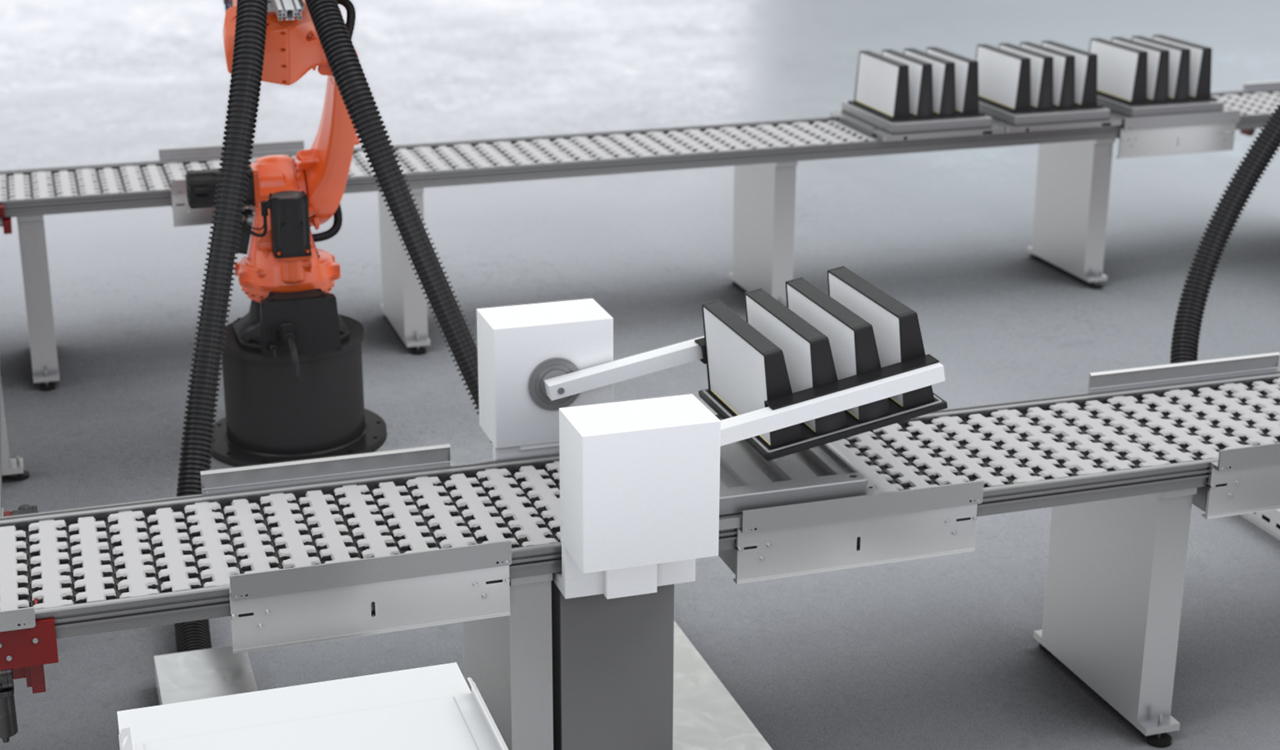
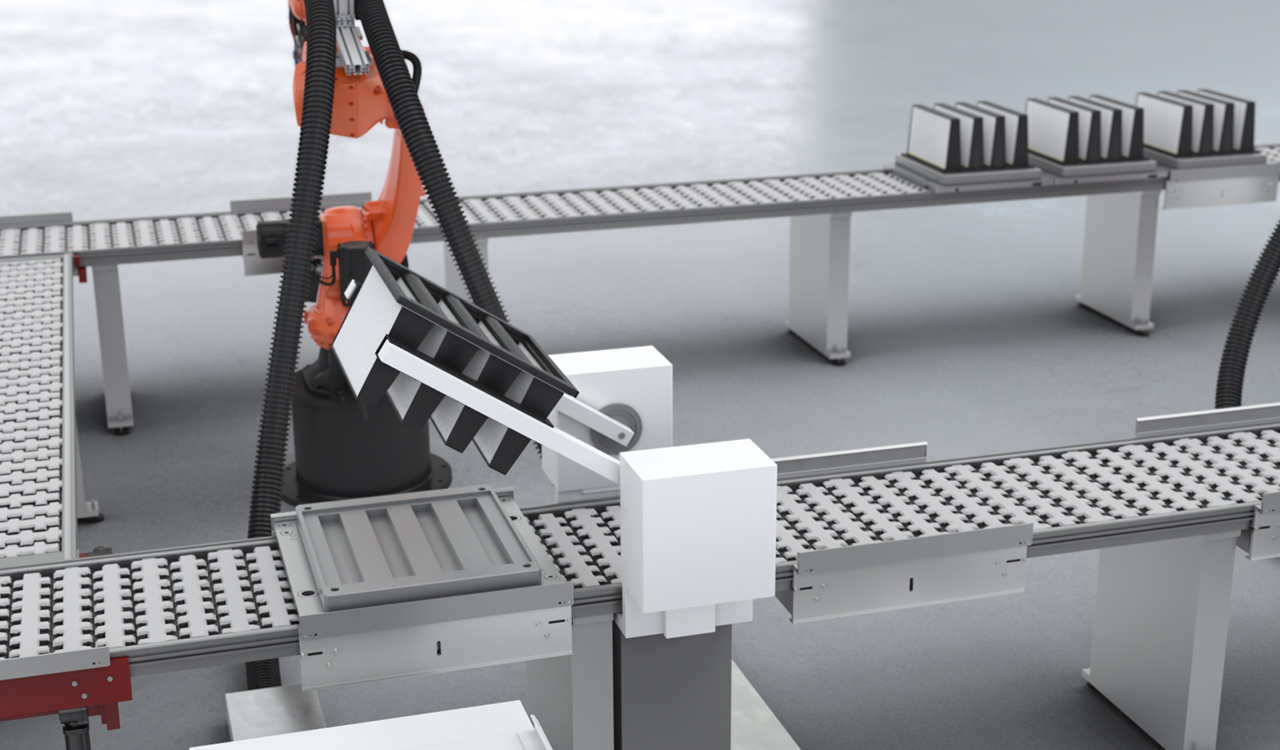
Once at the next station, the workpiece carrier is fixed in place, and the mixing head applies the 2K polyurethane sealing adhesive FERMADUR to the bottom of the V-filter to bond the filters to the opposite inner sides.
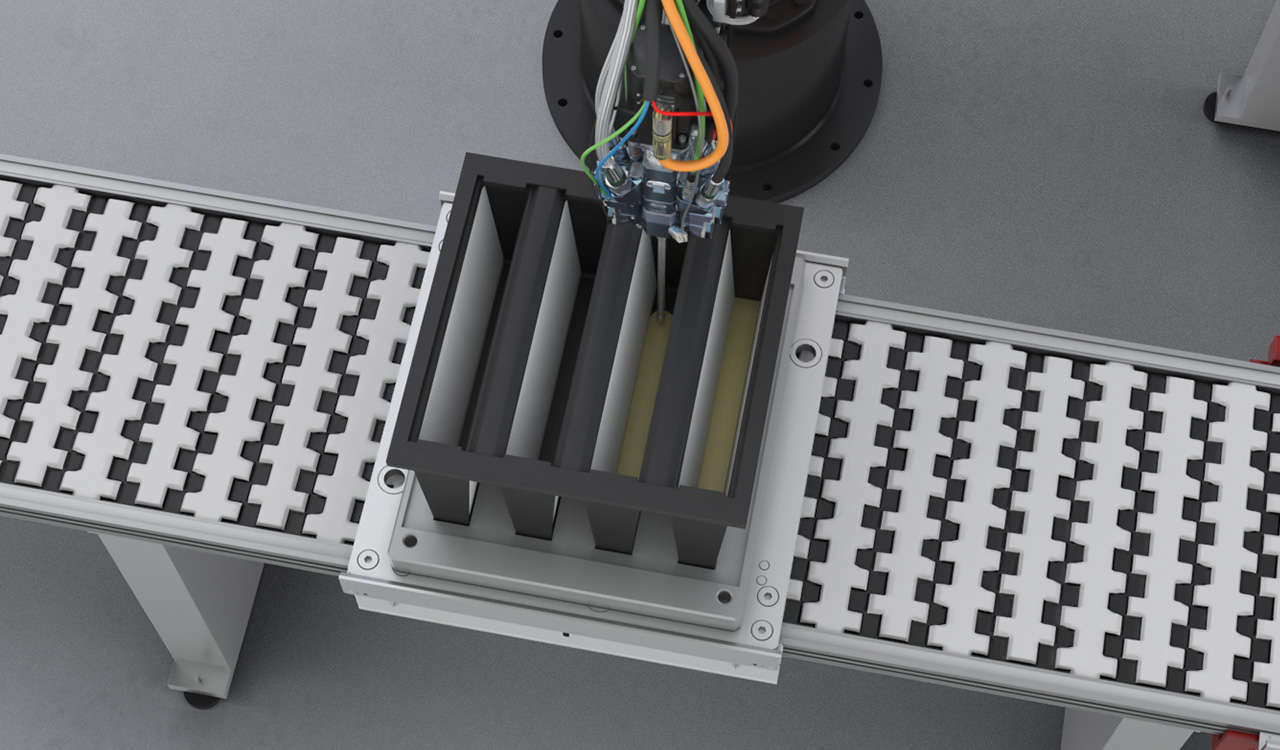
In the next process step, the second polyurethane sealing foam is applied to the frame contour seamlessly and precisely.
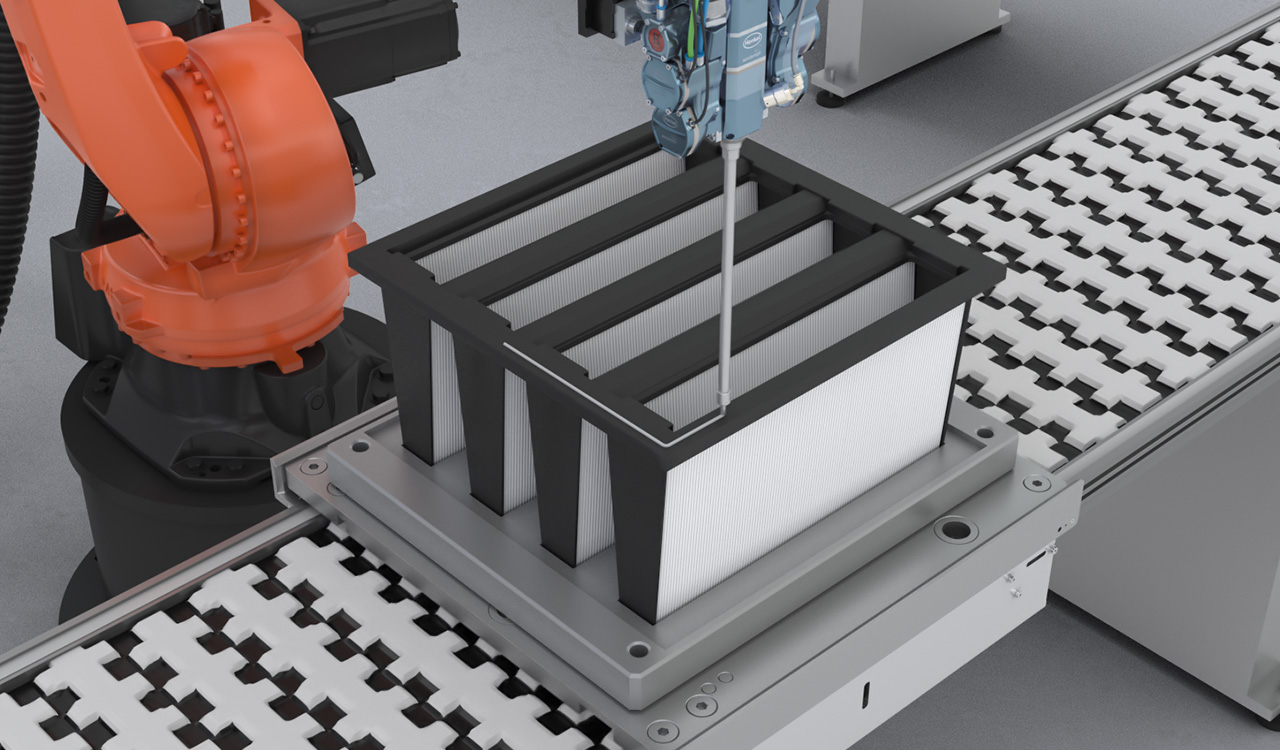
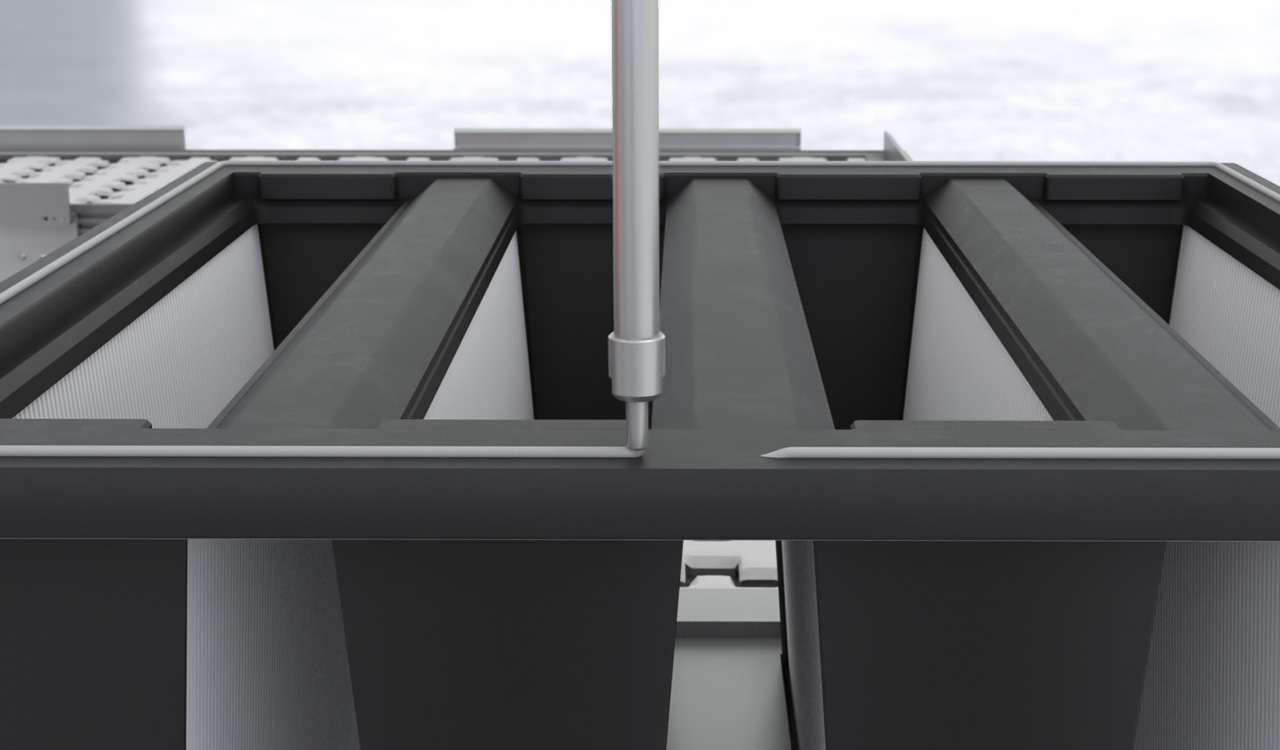
Once the second seal has been applied, the production process is complete, and the sealed and bonded V-filters are removed from the conveyor belt and stacked on a pallet.
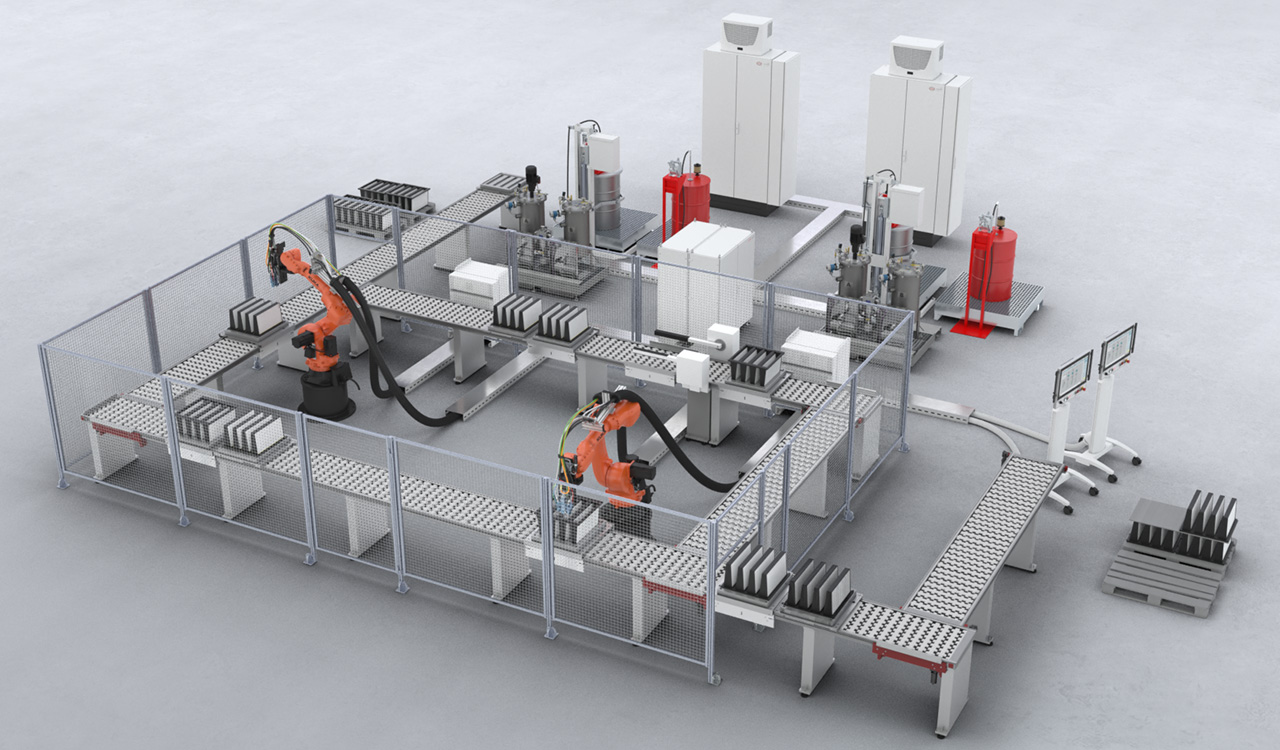